Как мы осваивали вакуумное магнетронное напыление плёнок. Магнетронное напыление тонких пленок
Как мы осваивали вакуумное магнетронное напыление плёнок / Хабр
Поскольку у нас прошёл относительно законченный этап в освоении технологии вакуумного напыления тонких плёнок, то у меня логично родилась мысль поделиться накопленным опытом с вами. Конечно, вам может показаться, что здесь было мало чего лежащего на самом острие науки и техники в этом движении. Однако на наш взгляд полезным может быть сам пройденный опыт.
Итак, история началась немного ранее, когда у нас появилась вакуумная камера. Путь её к нам был неблизок и может быть описан отдельным рассказом, но это, как говорится, «совсем другая история». Скажу только, что ещё раньше она приносила людям какую-то пользу в одной из лабораторий Гёттингенского университета.
Первое, на чём мы начали эксплуатировать вакуумную камеру, стало испробывание способа термического осаждения металлов на подложки. Способ прост и стар, как мир. В молибденовый тигель помещается мишень распыляемого металла, например, серебра. Вокруг него размещён нагревательный элемент. Мы использовали проволоку из вольфрамрениевого сплава, которую наматывали в виде спирали.
Полностью устройство для термического напыления выглядит следующим образом:
Оснастка для термического напыления металлов. а. В сборе (защитный экран и задвижка сняты). Обозначения: 1 – тигель, 2 – нагревательный элемент, 3 – паропровод, 4 – токоподвод, 5 – термопара, 6 – рамка для образца.
После пропускания тока (в вакуумную камеру идёт через гермовводы) спираль раскаляется, нагревает лодочку, в которой также нагревается материал мишени и испаряется. Облако металлического пара поднимается по паропроводу и окутывает тело, на которое необходимо осадить металлическую плёнку.
Сам по себе способ простой и хороший, однако есть и минусы: большое энергопотребление, трудно располагать в облаке пара поверхности (тела), на которые нужно осаждать плёнку. Адгезия тоже не самая лучшая. Наносили на разные материалы, в том числе на металлы, стекло, пластик и др. В основном — для исследовательских целей, поскольку мы только осваивали вакуумное оборудование.
Теперь настал черёд рассказать про вакуумную систему. Эксперименты мы проводили в вакуумной камере, оснащенной вакуумной системой, состоящей из роторного форвакуумного и турбомолекулярного насоса и обеспечивающей остаточное давление 9,5•10 -6 – 1,2•10 -5 мм.рт.ст. Если на первый взгляд кажется, что она не сложная, то на самом деле это не так. Во-первых, сама камера должна иметь герметичность, необходимую для поддержания высокого вакуума. Это достигается применением герметизации всех функциональных фланцев и отверстий. Верхний и нижний фланцы-крышки имеют такие же, по-принципу, резиновые уплотнения, как и самые малые отверстия, предназначенные для установки окон, датчиков, устройств, гермовводов и др. фланцевых крышек, только диаметром гораздо большим. Например, для надежной герметизации такого отверстия
Требуется фланец, прокладка и крепеж, как на этой фотографии.
Вот этим датчиком производится измерение вакуума в камере, сигнал с него поступает на прибор, который показывает уровень высокого вакуума.
Вакуум необходимого уровня (например 10-5 мм.рт.ст.), достигается следующим образом. Вначале форвакуумным насосом откачивается низкий вакуум до уровня 10-2. По достижении этого уровня включается высоковакуумный насос (турбомолекулярный), ротор которого может вращаться со скоростью 40 000 об/мин. При этом форвакуумный насос продолжает работать — он откачивает давление из самого турбомолекулярного насоса. Последний является довольно капризным агрегатом и его «тонкое» устройство и сыграло определенную роль в этом повествовании. Мы используем японский турбомолекулярный насос фирмы Osaka vacuum.
Откачиваемый из камеры воздух с парами масла рекомендуется сбрасывать в атмосферу, поскольку мелкодисперсные капельки масла могут «забрызгать» все помещение.
Разобравшись с вакуумной системой и отработав термическое напыление мы решили опробовать другой способ нанесения пленок — магнетронный. У нас был длительный опыт общения с одной крупной лабораторией, которая нам наносила функциональные нанопокрытия для некоторых наших разработок как раз способом магнетронного напыления. Кроме того у нас имеются довольно тесные связи с некоторыми кафедрами МИФИ, МВТУ и других вузов, которые также помогали нам освоить эту технологию.
Но со временем мы захотели использовать побольше возможностей, которые предоставляет вакуумная камера.
В скором времени у нас появился небольшой магнетрон, который мы и решили приспособить для нанесения пленок.
Именно магнетронный вакуумный метод напыления тонких металлических и керамических пленок считается одним из самых производительных, экономичных и простых в эксплуатации среди всех физических методов напыления: термического испарения, магнетронного, ионного, лазерного, электронно-лучевого. Магнетрон устанавливается в один из фланцев, как удобно для использования. Однако для напыления этого еще недостаточно, поскольку он требует подведения определенного напряжения, охлаждающей воды, а также газов для обеспечения поджига плазмы.
Теоретический экскурс
Упрощённо, магнетрон устроен следующим образом. На основании, которое одновременно служит магнитопроводом, помещены сильные магниты, которые образуют сильное магнитное поле. С другой стороны магниты закрываются металлической пластиной, которая служит источником распыляемого материала и называется мишенью. На магнетрон подается потенциал, а на корпус вакуумной камеры — земля. Разница потенциалов, образуемая между магнетроном и корпусом камеры в условиях разряженной атмосферы и магнитного поля приводит к следующему. Атом плазмообразующего газа аргона попадает в действие силовых линий магнитного и электрического поля и ионизируется под их действием. Выбившийся электрон притягивается к корпусу камеры. Положительный ион притягивается к мишени магнетрона и, разогнавшись под действием силовых линий магнитного поля, ударяется о мишень, выбивая из нее частицу. Та вылетает под углом обратным тому углу, под которым в мишень попал ион атома аргона. Частица металла летит от мишени в сторону расположенной напротив нее подложки, которая может быть сделана из любого материала.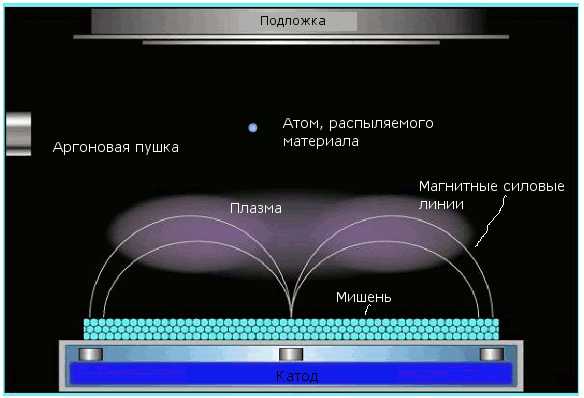
Наши вузовские друзья изготовили для этого магнетрона DC источник питания на мощность порядка 500 Вт.
Также мы соорудили систему газонапуска для плазмообразующего газа аргона.
Для размещения предметов, на которые будут напыляться плёнки, мы соорудили следующее приспособление. В крышке камеры имеются технологические отверстия, в которые можно устанавливать разные приспособления: гермовводы электроэнергии, гермовводы движения, прозрачные окошки, датчики и прочее. В одно из этих отверстий мы установили гермоввод вращающегося вала. Снаружи камеры на этот вал мы подвели вращение от небольшого электромоторчика. Установив скорость вращения барабана порядка 2-5 герц мы добились хорошей равномерности нанесения плёнок по окружности барабана.
Снизу, т.е. внутри камеры, мы укрепили на вал лёгкую металлическую корзину, на которую можно навешивать предметы. В канцелярском магазине такой стандартный барабан продаётся как корзина для мусора и стоит порядка 100 рублей.
Теперь у нас было в наличии практически всё необходимое для напыления плёнок. В качестве мишеней мы использовали следующие металлы: медь, титан, нержавейку, алюминий, сплав медь-хром.
И начали пылить. Через прозрачные окна в камеру можно было наблюдать свечение плазмы на поверхности мишени магнетрона. Так мы контролировали «на глазок» момент поджига плазмы и интенсивность напыления.
Способ контроля толщины напыления придумали достаточно простой. Размещали на барабане один и тот же кусочек фольги с замеренной площадью поверхности и измеряли его массу до и после сеанса напыления. Зная плотность напыляемого металла легко вычисляли толщину наносимого покрытия. Регулировали толщину покрытия либо изменением времени напыления, либо регулируя напряжение на источнике питания магнетрона. На этом фото видны прецизионные весы, позволяющие замерять массу образцов с точностью до десятитысячных долей грамма.
Наносили мы на различные материалы: дерево, металлы, фольга, пластики, бумага, полиэтиленовые плёнки, ткани, короче на всё, что можно было разместить в камере и прикрепить к барабану. В основном мы ориентировались на получение эффектов декоративного характера – изменение цвета или тактильного восприятия поверхности. На этих образцах органического и неорганического происхождения можно увидеть разницу в цвете до и после нанесения различных металлических плёнок.
Ещё более рельефно разница в цвете до и после напыления видна на тканях и плёнках. Здесь правый кусочек обычной полиэтиленовой плёнки – не напыленный, а левая покрыта слоем меди.
Ещё один эффект, который может быть использован для различных нужд – это проводимость тонких плёнок на подложках. На этом фото показано сопротивление кусочка бумаги (в омах), на который нанесена плёнка из титана толщиной чуть больше микрона.
Для дальнейшего развития мы выбрали несколько направлений. Один из них – улучшать эффективность напыления плёнок магнетронами. Собираемся «замахнуться» на собственную разработку и изготовление более мощного магнетрона высотой с камеру и мощностью в 2 раза больше, чем показанный в этом очерке. Также мы хотим опробовать технологию реактивного напыления, когда вместе с плазмообразующим газом аргоном в камеру подаются, например, кислород или азот и в ходе напыления плёнок на поверхности подложки образуются не чисто металлические плёнки, а оксиды или нитриды, которые имеют другой спектр свойств, нежели чистые металлические плёнки.
habr.com
Техника магнетронного распыления пленок
10. Техника магнетронного распыления тонких пленок. Газофазное осаждение тонких пленок.
С появлением и развитием магнетронных источников магнетронное распыление прочно вошло в практику получения металлизации современных гибридных интегральных схем Магнетронное распыление применяется в большом числе различных напылительных установок, как вновь разрабатываемых, так и модернизируемых вакуумных установках предыдущих годов выпуска. Подробнее о магнетронном распылении и магнетронных установках будет рассказано дальше.
Принцип действия магнетронного источника распыления
Магнетронными называются системы, в которых используются неод-нородные скрещенные электрическое и магнитное поля Магнетрон- ные распылительные системы получили свое название от СВЧ-прибо- ров магнетронного типа, хотя, кроме наличия скрещенных электричес¬кого и магнитного полей, ничего общего с ними не имеют Электричес¬кие параметры разряда в магнетронной системе в значительной степе¬ни зависят от рабочего давления, величины и конфигурации магнитно¬го поля, конструктивных особенностей распылительной системы [1] Магнетронные системы относятся к системам ионного распы¬ления, в которых распыление материала происходит за счет бомбар¬дировки поверхности мишени ионами рабочего газа (обычно арго¬на), образующихся в плазме аномального тлеющего разряда Высо¬кая скорость распыления, характерная для этих систем, достигается увеличением плотности ионного тока за счет локализации плазмы у распыляемой поверхности мишени с помощью сильного поперечно¬го магнитного поля
Принцип действия магнетронной распылительной системы показан на рис. 21. Основными элементами устройства являются катод-мишень, анод и магнитная система. Силовые линии магнитного поля замыкаются между полюсами магнитной системы. Поверхность мишени, расположенная между местами входа и выхода силовых линий магнитного поля, интенсивно распыляется и имеет вид замкнутой дорожки, геометрия которой определяется формой полюсов магнитной системы. При подаче постоянного напряжения между мишенью (отрицательный потенциал) и анодом (положительный или нулевой потенциал) возникает неоднородное электрическое поле и возбуждается аномальный тлеющий разряд. Наличие замкнутого магнитного поля у распыляемой поверхности мишени позволяет локализовать плазму разряда непосредственно у мишени.
Рис. 21.Схема магнетронной распылительной системы с плоской мишенью: 1 — катод-мишень; 2 — магнитная система; 3 - источник питания; 4 - анод; 5 — траектория движения электрона; 6 — зона распыления; 7 — силовая линия магнитного поля
Эмитированные с катода под действием ионной бомбардировки электроны совершают движение по замкнутым траекториям у поверхности мишени. Электроны оказываются как бы в ловушке, создаваемой с одной стороны магнитным полем, возвращающим электроны на катод, а с другой стороны — отрицательно заряженной поверхностью мишени, отталкивающей их. Электроны совершают циклическое движение в этой ловушке до тех пор, пока не произойдет несколько ионизирующих столкновений с атомами рабочего газа, в результате которых электрон потеряет полученную от электрического поля энергию и диффундирует на границу плазмы по направлению к аноду. Таким образом, большая часть энергии электрона, прежде чем он попадет на анод, используется на ионизацию и возбуждение атомов рабочего газа (чаще всего — аргона), что значительно увеличивает эффективность процесса ионизации и приводит к возрастанию концентрации положительных ионов у поверхности мишени. Это в свою очередь обусловливает увеличение интенсивности ионной бомбардировки мишени и значительный рост скорости распыления, а, следовательно, и скорости осаждения пленки. Средние скорости осаждения различных материалов с помощью магнетронной распылительной системы, имеющей плоскую дисковую мишень диаметром 150 мм при мощности источника 4 кВт и расположении подложки на расстоянии 60 мм от поверхности мишени, составляют от 10 до 70 нм/с.
Следует отметить, что плазма разряда существует, в основном, в области магнитной ловушки в непосредственной близости от мишени, и ее форма определяется геометрией и величиной магнитного поля. Создание магнитной ловушки у распыляемой поверхности мишени представляет собой простое, но весьма эффективное решение проблемы увеличения скорости распыления в плазменных распылительных системах. Но помимо этого достоинства магнетронная распылительная система обладает рядом специфических свойств, основным из которых является отсутствие бомбардировки подложки высокоэнергетическими вторичными электронами.
Известно, что при распылении материалов в плазме тлеющего разряда высокоэнергетические вторичные электроны с мишени являются основным источником нагрева подложек. В магнетронной распылительной системе вторичные электроны захватываются маг-нитной ловушкой и не бомбардируют подложку, что обеспечивает ее сравнительно низкую температуру. Источниками нагрева подложки в этой системе служат кинетическая энергия и энергия конденсации осаждаемых атомов, энергия отраженных от мишени нейтрализованных ионов и энергия ионов вторичной плазмы, а также излучение плазмы.
Энергия конденсации составляет 3-9 эВ/атом, кинетическая энергия в зависимости от распыляемого материала от 5 (для алюминия) до 20 эВ/атом (для вольфрама), а излучение плазмы 2-10 эВ/атом. Энергия вторичных ионов в зависимости от конструкции магнетрона и подложкодержателя может составлять 30-50 эВ/ион. Плотность ионного тока на подложку зависит только от концентрации вторичной плазмы в области подложки, а она, в свою очередь, зависит от мощности магнетронного разряда и конфигурации и напряжённости магнитного поля магнетрона. Магнетроны условно подразделяются на «сбалансированные» и «разбалансированные» с разной степенью разбалансированности. Эту степень разбалансированности можно характеризовать отношением плотности тока вторичных ионов на подложку к плотности потока падающих на нее распыленных атомов.
От степени разбалансированности магнетрона зависит и крутизна вольтамперной характеристики разряда, и термическая нагрузка на подложки, и во многих случаях, качество и структура напыляемых пленок.
Сравнение этих результатов с данными, полученными для метода термического испарения в вакууме, показывает (рис. 22), что при сравнительно низких скоростях испарения последний характеризуется более высокой тепловой энергией на подложку. Это объясняется тем, что в данном случае основным источником нагрева подложки является радиационное излучение с поверхности расплавленного материала. Однако при высоких скоростях испарения начинает преобладать нагрев за счет энергии конденсации. Во многих случаях нагрев подложки в магнетронных системах сравним, а при испарении тугоплавких материалов даже ниже, чем при методе термического испарения. Это дает возможность использовать магнетронные системы для нанесения пленок на подложки из материала с низкой термостойкостью (пластики, полимеры, оргстекло и бумагу).
Рис. 22.Удельная тепловая энергия, рассеиваемая на подложке при электронно-лучевом испарении (диаметр тигля 5 см) различных металлов. Горизонтальными линиями показаны средние значения энергии при распылении тех же материалов в магнетронной системе.
Основные рабочие параметры магнетронных распылительных систем — напряжение на электродах, ток разряда, плотность тока на мишени и удельная мощность, величина индукции магнитного поля и рабочее давление. От величины и стабильности перечисленных параметров, которые взаимно связаны между собой, зависят стабильность разряда и воспроизводимость процесса нанесения пленок.
Магнетронные системы относятся к низковольтным системам распыления. Напряжение питания постоянного тока не превышает 700—800 В. Однако, для удобства поджига разряда, особенно при низких давлениях, применяется «поджигающее» напряжение, которое составляет обычно от 1200 до 1350 В. Источник «поджигающего» напряжения имеет круто падающую вольтамперную характеристику и при токе магнетрона более 100—200 мА напряжение на разряде становится «рабочим».
Рабочее напряжение обычно составляет 300—700 В, причем на мишень подается отрицательный потенциал, а анод обычно имеет нулевой потенциал. Однако в магнетронных системах с плоским катодом для более полного улавливания вторичных электронов реко-мендуется на анод подавать небольшое положительное смещение (40— 50 В). В некоторых системах предусматривается подача отрицательного напряжения смещения на подложку (до 100 В) для реализации осаждения со смещением.
Ток разряда зависит от многих факторов, например, от рабочего напряжения, давления и рабочего газа, индукции магнитного поля, конфигурации магнетронной системы, распыляемого материала, и определяется мощностью источника питания. Плотность тока на мишени очень велика и для систем с плоским катодом может достигать — 200 мА/см2, причем максимальные плотности тока в централь¬ной части зоны распыления могут быть значительно выше. Значения удельной мощности выделяемой на поверхности мишени за счет ионной бомбардировки в магнетронных системах с плоским катодом — 100 Вт/см2и выше. Предельно допустимая мощность определяется условиями охлаждения мишени и теплопроводностью распыляемого материала.
Магнетронная распылительная система может работать в диапазоне давлений от 10-2до 1 Па и выше. Важнейшими параметрами, во многом определяющими характер разряда в ней, являются геометрия и величина магнитного поля, индукция которого у поверхности мишен 0,03-0,1T.
studfiles.net
Магнетронное распыление - технология и установки тонких пленок мишени метод реактивное недостатки видео
Магнетронное распыление — технология и установки.
Магнетронное распыление — технология нанесения тонких плёнок на подложку с помощью катодного распыления мишени в плазме магнетронного разряда — диодного разряда в скрещенных полях. Напыление металлов и сплавов производят в среде инертного газа, как правило, аргона.
Описание
Преимущества
Применение
Описание:
Магнетронное распыление — технология нанесения тонких плёнок на подложку с помощью катодного распыления мишени в плазме магнетронного разряда — диодного разряда в скрещенных полях. Технологические устройства, предназначенные для реализации этой технологии называют магнетронными распылительными системами или, сокращённо, магнетронами.
Напыление металлов и сплавов производят в среде инертного газа, как правило, аргона.
Принцип магнетронного распыления основан на образовании над поверхностью катода кольцеобразной плазмы в результате столкновения электронов с молекулами газа (чаще всего аргон). Мишень устройства магнетронного распыления является источником распыляемого материала. Положительные ионы, образующиеся в разряде, ускоряются в направлении катода — мишени, бомбардируют его поверхность, выбивая из неё частицы материала.
Тяжелый ион аргона (белый шарик) разгоняется в электрическом поле и выбивает из мишени атом материала (красный шарик), который высаживается на поверхности подложки, образуя на ее поверхности пленку.
Покидающие поверхность мишени частицы осаждаются в виде плёнки на подложке, а также частично рассеиваются на молекулах остаточных газов или осаждаются на стенках рабочей вакуумной камеры.
При столкновении ионов с поверхностью мишени происходит передача момента импульса материалу. Падающий ион вызывает каскад столкновений в материале. После многократных столкновений импульс доходит до атома, расположенного на поверхности материала, который отрывается от мишени и высаживается на поверхности подложки. Среднее число выбитых атомов на один падающий ион аргона называют эффективностью процесса, которая зависит от угла падения, энергии и массы иона, массы испаряемого материала и энергии связи атома в материале. В случае испарения кристаллического материала эффективность также зависит от расположения кристаллической решетки.
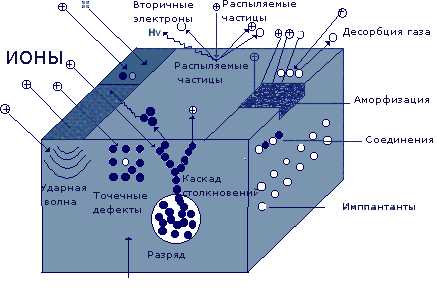
Для эффективной ионизации аргона, распыляемый материал(мишень) размещают на магните. В результате эмиссионные электроны, вращающиеся вокруг магнитных силовых линий локализуются в пространстве и многократно сталкиваются с атомами аргона, превращая их в ионы.
При бомбардировке поверхности мишени ионами генерируются несколько процессов:
- — ионное(катодное) распыление материала мишени,
- — вторичная электронная эмиссия,
- — десорбция газа,
- — имплантация дефектов,
- — ударная волна,
- — аморфизация.
Магнетронное распыление позволяет получать высокую плотность ионного тока, а значит, и высокие скорости распыления при относительно низких давлениях порядка 0,1 Па и ниже.
Преимущества:
— покрытия полученные данным способом характеризуются высокой равномерностью, относительно низкой пористостью и высоким уровнем адгезии к подложке,
— возможность нанесения покрытия сложного состава,
— возможность наносить покрытия на большие площади,
— относительно дешевый метод осаждения,
— низкие температуры подложки,
— хорошая однородность покрытия,
— хорошая управляемость,
— возможность нанесения нескольких покрытий в одном технологическом цикле.
Применение:
— в электронике: для осаждения тонких пленок, полупроводников, диэлектриков, металлов,
— в оптике: для нанесения проводящих, отражающих, поглощающих покрытий,
— в машиностроении: для нанесения специальных покрытий, улучшающих свойства используемых материалов,
— в легкой промышленности: для получения металлизированных тканей.
РЕКОМЕНДАЦИИ ПО ИСПОЛЬЗОВАНИЮ ТЕХНОЛОГИЙ
ЗВОНИТЕ: +7-908-918-03-57
либо воспользуйтесь поиском аналогов технологий:
ПОИСК АНАЛОГОВ ТЕХНОЛОГИЙ
или пиши нам здесь...карта сайта
Войти Регистрация
Виктор ПотехинПоступил вопрос касательно санации трубопровода. Дан ответ. В частности указана более инновационная технология.
2018-05-17 18:10:26Виктор ПотехинПоступил вопрос касательно сотрудничества, а именно: определения направлений развития предприятия и составления планов будущего развития. В настоящее время ведутся переговоры. Будет проанализирована исходная информация, совместно выберем инновационные направления и составим планы.
2018-05-18 10:34:05Виктор ПотехинПоступил вопрос касательно электрохимических станков. Дан ответ.
2018-05-18 10:35:57Виктор ПотехинПоступил вопрос относительно пиролизных установок для сжигания ТБО. Дан ответ. В частности, разъяснено, что существуют разные пиролизные установки: для сжигания 1-4 класса опасности и остальные. Соответственно разные технологии и цены.
2018-05-18 11:06:55Виктор ПотехинК нам поступают много заявок на покупку различных товаров. Мы их не продаем и не производим. Но мы поддерживаем отношения с производителями и можем порекомендовать, посоветовать.
2018-05-18 11:08:11Виктор ПотехинПоступил вопрос по гидропонному зеленому корму. Дан ответ: мы не продаем его. Предложено оставить заявку в комментариях для того, чтобы его производители выполнили данную заявку.
2018-05-18 17:44:35Виктор ПотехинПоступает очень много вопросов по технологиям. Просьба задавать эти вопросы внизу в комментариях к записям.
2018-05-23 07:24:36Andrey-245Не совсем понятно. Эту батарейку можно вообще не заряжать что ли? Сколько вольт она выдает? И где ее купить? И можно ли такие соединить последовательно-параллельно, собрав нормальный аккумулятор, например, для электромобиля?
2018-08-23 10:09:48Виктор ПотехинАндрей, какую батарейку?
2018-08-24 08:33:25SergeyShefДобрый день! Интересна вышеописанная установка. Как можно её заказать ? Какие условия сотрудничества у автора?
2018-08-27 17:07:42Виктор ПотехинСергей, кидайте сюда ссылку на установку. Или пишите мне [email protected]
2018-08-27 18:52:14SergeyShefЯ у Вас спрашивал, как и где её можно купить?
2018-08-27 21:07:41SergeyShefКто изготовил тот образец, который у Вас на фото и могут ли изготавливать на заказ?
2018-08-27 21:10:05Виктор Потехинне могу понять, что за установка. скиньте сюда ссылку
2018-08-27 23:15:16Виктор Потехинне обладаем такой информацией
2018-08-28 21:45:17npc-sesДобрый день! SergeyShef изделие подобное тому, что изображено в заголовке, да и в принципе любое изделие по технологии LTCC можно изготовить на нашем производстве АО "НПЦ "СпецЭлектронСистемы". Находимся в г. Москва. Можете написать мне на электронную почту [email protected]
2018-08-29 18:41:34npc-sesНа нашем производстве имеется пожалуй самый полный комплект оборудования в России, который позволяет производить 3D микросборки, в том числе по технологии LTCC, в замкнутом цикле, начиная от входного контроля материалов, всех промежуточных производственных процессов...
2018-08-29 18:47:20DjahanКРИОГЕЛЬ ДЛЯ РОСТА И РАЗВИТИЯ РАСТЕНИЙ В НЕБЛАГОПРИЯТНЫХ УСЛОВИЯХ. кто производит, как найти, чтобы купить?
2018-08-30 23:48:23Виктор Потехинкупить можно у производителя
2018-09-01 20:58:09Andrey-245Здравствуйте, Виктор. Я задавал вопрос (2018-08-23) имелось в виду про углеродную батарейку, которая служит более 100 лет.
2018-09-18 12:15:33Виктор Потехинвся информация, что есть по батарейке, написана в соответствующей статье.
2018-09-18 20:47:11Виктор ПотехинЧтобы получить информацию о сайтах производителей технологий, напишите внизу страницы - в комментариях Вконтакте
2018-09-29 20:58:40DenssikВсем доброго дня! Я руководитель центра в котором разработан данный робот, по всем вопросам касательно сотрудничества можете писать на почту [email protected]
2018-10-03 17:19:46Виктор ПотехинDenssik, Напишите пжл о каком работе идет речь?
2018-10-03 19:10:33Для публикации сообщений в чате необходимо авторизоваться
реактивное магнетронное распыление установка тонких пленок металлов аморфные сплавывакуумные установки метод мишень для магнетронного распыленияаргон в магнетронном распыленииметод магнетронного распыления для полимеровмагнетронное напыление ассестированное катодным распылениеммишень для магнетронного распыления молибденовая круглая
Похожие записи
Коэффициент востребованности 375
comments powered by HyperCommentsxn--80aaafltebbc3auk2aepkhr3ewjpa.xn--p1ai
Магнетронное распыление — Википедия Переиздание // WIKI 2
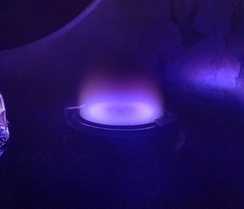
Магнетронная распылительная система (магнетрон)
Магнетронное распыление — технология нанесения тонких плёнок на подложку с помощью катодного распыления мишени в плазме магнетронного разряда — диодного разряда в скрещенных полях. Технологические устройства, предназначенные для реализации этой технологии, называются магнетронными распылительными системами или, сокращённо, магнетронами (не путать с вакуумными магнетронами — устройствами, предназначенными для генерации СВЧ колебаний).
Магнетронный разряд
Магнетронным разрядом называют диодный газовый разряд в скрещенных полях (существует область пространства в разрядном объёме, где электрическое и магнитное поля ортогональны друг другу B⊥E{\displaystyle \mathbf {B} \perp \mathbf {E} }; силовые линии магнитного поля направлены поперёк линий тока).
История открытия
В 1898 году британский исследователь Филлипс описал появление кольцеобразного электрического разряда, возникающего вокруг зазора между стержневыми электродами в стеклянной колбе при пониженном давлении при включении осевого магнитного поля. В 1913 году проф. Струтт интерпретировал филлипсовский разряд как электрический разряд в скрещенных полях — аксиальном магнитном поле и радиальном электрическом. Он предположил, что радиальное электрическое поле создаётся положительным зарядом, накопленным за время предыдущего разряда на стенке колбы напротив зазора между электродами, а ионизация газа вызвана отрицательными частицами за время их удлинённого пробега поперёк магнитного поля от оси к стенке колбы. Струтт установил кольцевой анод вокруг торцов стержневых электродов и получил устойчивый кольцевой разряд. Наибольший вклад в изучение магнетронного разряда был внесён голландским физиком Ф. М. Пеннингом. Наряду с другими применениями магнетронного разряда (в качестве ионного источника, датчика измерения вакуума, ионного насоса), им было предложено применение магнетронного разряда для распыления и нанесения покрытий[1].
Физические основы
С точки зрения механизма эмиссии электронов, магнетронный разряд постоянного тока представляет собой аномальный тлеющий разряд. Электроны покидают поверхность катода за счёт ионно-электронной эмиссии под действием ионной бомбардировки. В связи с тем, что коэффициент ионно-электронной эмиссии весьма мал, ионный ток на катод превышает электронный как минимум на порядок. Баланс заряженных частиц в плазме обеспечивается ионизацией нейтральных атомов газа электронами, ускоренными электрическим полем в тёмном катодном пространстве.
Принцип работы магнетрона
В отличие от тлеющего разряда, где электрон, не испытывающий столкновений, будет свободно ускоряться электрическим полем, пока не покинет область катодного падения потенциала (тёмное катодное пространство), наличие поперечного магнитного поля заставляет электрон искривлять свою траекторию под действием силы Лоренца. При достаточной величине магнитного поля электрон вернётся на катод с почти нулевой энергией и вновь начнёт ускоренное движение под действием электрического поля. Траекторией его движения будет циклоида, электрон дрейфует вдоль поверхности катода в направлении, перпендикулярном как электрическому, так и магнитному полю. Электрон находится в «ловушке», покинуть которую он может, только совершив столкновение с другой частицей. Тогда он перейдёт на новую траекторию, расположенную чуть дальше от катода и так до тех пор, пока не ослабнут поля, магнитное — за счёт удаления от полюсов магнитной системы, электрическое — за счёт плазменной экранировки. За счёт наличия ловушки многократно возрастает эффективность ионизации эмитированными электронами, что позволяет, в отличие от обычного диодного разряда, получать высокую плотность ионного тока, а значит, и высокие скорости распыления при относительно низких давлениях порядка 0,1 Па и ниже. Для того, чтобы ловушка работала эффективно, необходимо исключить утечку электронов на анод вдоль силовых линий магнитного поля, а траектории дрейфа должны быть замкнуты.
Основы технологии
Технологическое значение магнетронного распыления заключается в том, что бомбардирующие поверхность катода (мишени) ионы распыляют её. На этом эффекте основаны технологии магнетронного травления, а благодаря тому, что распылённое вещество мишени, осаждаясь на подложку, может формировать плотную плёнку наиболее широкое применение получило магнетронное напыление.
Распыление мишени
При столкновении ионов с поверхностью мишени происходит передача момента импульса материалу[2][3]. Падающий ион вызывает каскад столкновений в материале. После многократных столкновений импульс доходит до атома, расположенного на поверхности материала, и который отрывается от мишени и высаживается на поверхности подложки. Среднее число выбитых атомов на один падающий ион аргона называют эффективностью процесса, которая зависит от угла падения, энергии и массы иона, массы испаряемого материала и энергии связи атома в материале. В случае испарения кристаллического материала эффективность также зависит от расположения кристаллической решетки.
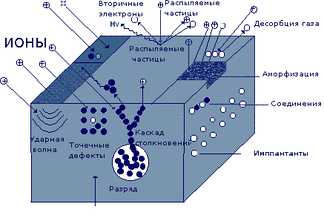
Физические процессы, происходящие в материале при его бомбардировке
Покидающие поверхность мишени частицы осаждаются в виде плёнки на подложке, а также частично рассеиваются на молекулах остаточных газов или осаждаются на стенках рабочей вакуумной камеры.
Напыление металлов и сплавов
Напыление металлов и сплавов производят в среде инертного газа, как правило, аргона. В отличие от технологии термического испарения, при магнетронном распылении не происходит фракционирования мишеней сложного состава (сплавов).
Реактивное напыление
Для напыления сложных соединений, например оксидов и нитридов, применяется так называемое реактивное магнетронное напыление. К плазмообразующему газу (аргону) добавляют реактивный газ (например, кислород или азот). В плазме магнетронного разряда реактивный газ диссоциирует, высвобождая активные свободные радикалы, которые взаимодействуют с осаждёнными на подложку распылёнными атомами, формируя химическое соединение.
Магратрон
В советской литературе некоторое время встречался также термин «Магратрон». Слог «Маг» сокращённо означало магнетронное, «ра» — распылительное, «трон» — электроразрядное устройство. В связи с его непереводимостью на иностранные языки, термин не прижился, вместо него стали использовать слово «магнетрон».
См. также
Примечания
Литература
Эта страница в последний раз была отредактирована 10 апреля 2018 в 12:35.wiki2.org
Технология напыления тонких пленок
2 марта
В настоящее время на производственных предприятиях микроэлектронной промышленности выявляется потребность в нанесении тонких металлических и диэлектрических пленок на различные поверхности. Тонкие пленки широко применяются в качестве упрочняющих, светоотражающих, проводящих и диэлектрических покрытий. Чаще всего данные виды работ ведутся в НИИ для получения и исследования новых перспективных материалов как для микроэлектронной промышленности, так и для устройств наноэлектроники.
С
амое простое применение тонких пленок — декоративное — создание зеркал и покрытий для ювелирных изделий. Однако, в основном, покрытия малых толщин используются в НИИ для изучения электрических свойств новых материалов при формировании контактов; при нанесении резистивных и проводящих покрытий в промышленности и при изготовлении элементов интегральных микросхем в микроэлектронике; в создании светофильтров, отражающих и светопроводящих покрытий оптоэлектроники; современных литографических процессах.
Современные методы получения тонкопленочных структур
В последние годы, благодаря интенсивным экспериментальным и теоретическим исследованиям, в технологии тонких пленок достигнут значительный прогресс. В зависимости от решаемой задачи, в распоряжении исследователей имеются различные методики получения образцов, гарантирующие воспроизводимые и стабильные характеристики конечного продукта.
Таблица 1. Методы нанесения тонкопленочных покрытий |
||||
Наименование метода |
Условия реализации метода |
Основные виды покрытий |
Преимущества метода |
Недостатки метода |
Термовакуумное (резистивное) испарение |
Рабочая среда: вакуум 10-2...10-3 Па. Испарение металлов резистивным нагреванием |
Металлические покрытия: Al, Ag, Cu, Zn, Cd, Cr, Ni, Co, Si |
Высокая скорость осаждения. Возможность получения толстых покрытий |
Недостаточно плотная структура покрытий. Невысокие механические свойства |
Электронно-лучевое испарение |
Рабочая среда: вакуум 10-4...10-3 Па реактив. газы N2, O2, Ch5. Испарение металлов сфокусированным электронным пучком с дополнительной ионизацией |
Металлические покрытия: Al, Ag, Cu,Ti, Cr, Ni, Co, Si Керамические покрытия: TiN, ZrN, TiC, ZrC, TiCN, ZrCN, Al2O3, TiO2, SiO2, ZrO2, ZrO2/Y2O3 |
Высокая скорость осаждения. Возможность получения толстых покрытий (до 200 мкм). Высокая чистота покрытий (минимум примесей) |
Трудно обеспечить равномерность толщины и стехиометрии на изделиях сложной конфигурации. Низкая степень загрузки изделиями объема рабочей камеры |
Лазерное испарение (абляция) |
Рабочая среда: вакуум 10-5...10-3 Па. Испарение материалов различного состава лазерным импульсом длительностью от мкс до фс. |
Покрытия для микроэлектроники: Sb2S3, As2S3, SrTiO3, BaTiO3, GaAs Алмазоподобные покрытия (DLC) с высокими характеристиками |
Получение покрытий сложных соединений Высокая чистота покрытий (минимум примесей) |
Сложность реализации |
Вакуумно-дуговое испарение |
Рабочая среда: вакуум 10-3...10-2 Па. Реактив. газы N2, O2, Ch5; Р = 0,01...1 Па, Т = 300...600°С. Испарение металлов в катодном пятне дугового разряда. Осаждение покрытий с высокой степенью ионного воздействия |
Металлические покрытия: Ti, Zr, Hf, Cr, Ta, Ni, Co,Si, MCrAlY (M=Ni, Co) Керамические покрытия: TiN, ZrN, CrN, TiC, TiCN, ZrCN, TiAlN, AlCrN, TiO2, ZrO2 Нанокомпозиты: TiAlN/Si3N4, AlCrN/Si3N4. Покрытия DLC |
Высокая скорость осаждения. Относительная простота технической реализации. Эффективная ионная очистка изделий перед нанесением покрытий. Высокие свойства керамических покрытий |
Наличие в структуре покрытий микрокапельной металлической фазы. Относительно высокие температуры осаждения покрытий |
Магнетронное распыление |
Рабочая среда: чистые газы Ar, N2, O2, Ch5; Р = 0,05– 1 Па, Т = 60...6000°С Ионное распыление металлов в магнетронном разряде |
Полный спектр металлических покрытий: Al, Ag, Au,Cu, Zn, Sn, Cd Ti, Zr, Hf, Cr, Ta, Ni, Co, Si, MCrAlY (M=Ni, Co) и др. Керамические покрытия: TiN, ZrN, CrN, TiC, TiCN, ZrОN, TiAlN, AlCrN, TiBN CrAlTiYN, TiO2, ZrO2, Al2O3, SiO2. Нанокомпозиты: 3D: TiAlN/Si3N4, TiN/BN, AlCrN/Si3N4, ZrN/Cu, ZrO2/Al2O3. 2D: TiN/NbN, TiN/CrN, TiN/AlN, CrN/AlN, TiN/CN. Покрытия DLC |
Плотная микро- (нано-) кристаллическая структура металлических и керамических покрытий при полном отсутствии капельной фазы Возможность нанесения покрытий на термочувствительные материалы при низких температурах Наиболее широкий спектр покрытий различного назначения; высокая скорость осаждения; высокие свойства металлических и керамических покрытий |
Относительная сложность технической реализации метода при получении реактивных (керамических) покрытий. Относительно высокая стоимость оборудования |
Параметры магнетронного распыления установки CS-1000 | Параметры термовакуумного испарения установки CS-1000 |
Скорость осаждения Cu для 300 Вт — 125 Å/мин Скорость осаждения Ni и Cr для 200 Вт — 45 Å/мин |
Скорость осаждения Cu, V и др. для 70% мощности — 0,33 Å/с Скорость осаждения Ni для 25% мощности — 0,25 Å/с |
Методы получения пленок подразделяются на физические (PVD — Physical Vapor Deposition), химические и промежуточные газофазные химические методы (CVD — Chemical Vapor Deposition). Все методы нанесения пленок характеризуются такими параметрами как скорость получения покрытий и диапазон достигаемых толщин. Для РVD и CVD эти параметры, соответственно, обычно находятся в пределах 1…1000 мкм/ч и 0,01…10 (100) мкм. Для химических методов они составляют 100…1000 мкм/ч и 0,1…1000 мкм; для взрывных (детонационных) и плазменных методов — до 10…100 мм/ч и 0,1…10 мм, соответственно.
Процесс получения пленочных покрытий сопровождается рядом специфических явлений. Рост пленки происходит в два этапа: образование зародыша на поверхности подложки и рост зародыша. При взаимодействии двух атомов друг с другом между ними может возникнуть химическая связь. В результате атомы дольше остаются на поверхности и успевают присоединить следующий атом и т.д. Так образуются скопления адсорбированных атомов, более длительное время связанных с подложкой и имеющих тенденцию к дальнейшему росту, который происходит за счет присоединения мигрирующих по поверхности атомов, падающих атомов и более мелких кластеров. Таким образом, на поверхности формируется сеть объединенных кластеров, затем происходит их объединение, и образуется сплошная пленка. При этом в зависимости от скорости осаждения, природы подложки и типа осаждаемого материала возможны три типа роста пленки:
– островковый рост;
– послойный рост;
– послойно-островковый, или смешанный рост.
Тип роста определяется взаимодействием атомов пленки с атомами подложки и между собой. Островковый рост происходит, если осаждаемые атомы напыляемой пленки сильнее взаимодействуют между собой, чем с атомами подложки. Послойный рост происходит при образовании больших по площади двумерных зародышей на поверхности подложки вследствие того, что атомы напыляемого материала сильнее связываются с атомами подложки. Послойно-островковый рост имеет место, когда островки начинают расти после того, как сформируется пленка толщиной в несколько атомных монослоев.
Рассмотрим особенности методов магнетронного распыления и термовакуумного испарения на примере установки CS-1000 Sputter & PVD Deposition System фирмы Asia Pacific Systems Inc. (см. рис. 1, 2).
Рис. 1. Внешний вид установки CS-1000 Sputter & PVD Deposition System |
Рис. 2. Схематическое изображение основных узлов установки CS-1000 Sputter & PVD Deposition System |
![]() |
Установка CS-1000 обеспечивает реализацию двух методов нанесения — термовакуумного и магнетронного.
Преимущества и недостатки этих методов
Магнетронное распыление
Работа магнетронного распылительного устройства (см. рис. 3) основана на свойствах катодной области аномального тлеющего газового разряда, в которой катод (мишень) распыляется под действием ионной бомбардировки. Приложенное в области катода перпендикулярно электрическому магнитное поле позволяет снизить рабочее давление плазмообразующего газа без уменьшения интенсивности ионной бомбардировки и улучшить условия транспортировки распыляемого вещества к подложке. Это происходит благодаря уменьшению рассеяния, вызванного соударениями с молекулами газа. Между катодом и подложкой возникает зона низкотемпературной плазмы. Распыляемые частицы осаждаются в виде тонкого слоя, а также частично рассеиваются и осаждаются на стенках рабочей камеры.
Рис. 3. Внешний вид установки CS-1000 Sputter & PVD Deposition System |
При использовании разряда постоянного тока (DC-магнетрон) можно распылять различные металлы и их сплавы (ванадий, хром, никель, титан, медь, серебро, нержавеющая сталь, латунь, бронза и др.), а также получать их химические соединения, добавляя в плазмообразующий газ (аргон) соответствующие реактивные газы (кислород, азот и др.).
Так, если в содержащую титановую мишень систему во время распыления вводить азот, то можно получить пленку нитрида титана, а введение, например, кислорода, позволяет получать на поверхности подложки пленку двуокиси титана.
Варьируя содержание реактивного газа и скорость напыления, удается получать пленки разной толщины, химического и фазового состава.
Используемые газы:
– Ar для напыления Cu, Cr, Ni, V и т.д.;
– O2 для очистки подложек в ВЧ-плазме и напыления оксидов VxOx-y (CuxOx-y и т.д.) в совокупности с Ar;
– N2 для напыления нитридов различных материалов.
DC-магнетрон является современным вариантом устройства катодного распыления материалов в вакууме с использованием источника постоянного тока для нанесения проводящих покрытий на изделия. Принцип его действия основан на явлении физического распыления катода (материала мишени) ускоренными ионами рабочего газа, которые бомбардируют поверхность мишени под действием приложенного отрицательного потенциала.
Характерной особенностью магнетронов является использование специальной магнитной системы, которая создает над распыляемой мишенью замкнутое по контуру туннелеобразное магнитное поле. Благодаря этому полю создаются условия для получения локализованной плазмы высокой плотности и, соответственно, высокой плотности ионных токов, распыляемых мишенью. В результате достигается высокая производительность распыления материалов. Конструктивные принципы построения магнетронных устройств позволяют достаточно просто реализовать задачу нанесения однородных покрытий на широкоформатные поверхности.
Адгезия металлических слоев с подложкой у пленок, полученных магнетронным способом, существенно выше, чем у таких же пленок, полученных термовакуумным напылением, при сравнимых скоростях напыления. Это связано с более высокой энергией конденсирующихся частиц при магнетронном распылении и дополнительной активацией поверхности действием плазмы.
В отличие от других способов нанесения тонкопленочных покрытий, способ магнетронного распыления позволяет достаточно тонко регулировать толщину металлического слоя, а значит, его сопротивление, что очень важно при создании структур с определенной проводимостью.
Метод магнетронного распыления позволяет получать тонкие пленки высокого качества с рекордными физическими характеристиками (толщина, пористость, адгезия и пр.), а также проводить послойный синтез новых структур (структурный дизайн), создавая пленку буквально на уровне атомных плоскостей.
Термовакуумное испарение
Суть процесса термовакуумного испарения (см. рис. 4) состоит в переводе осаждаемого материала с помощью нагрева в парогазовую фазу. Образующийся при этом парогазовый поток в высоком вакууме распространяется прямолинейно, т.к. отсутствует соударение с молекулами остаточного газа — длина свободного пробега молекул в остаточном газе на порядок превышает расстояние от источника до подложки; газ попадает на подложку, поверхность которой холоднее источника пара; при этом происходит конденсация и образование пленки.
Рис. 4. Принцип термовакуумного испарения |
Заключение
В настоящее время Россия входит в этап активного освоения современных технологий производства микроэлектроники и нанотехнологий. Современное производство требует перестройки технологического процесса под реалии современности. Потенциальные возможности применения магнетронных распылительных систем в настоящее время еще далеко не полностью выяснены и реализованы, но уже сейчас применение магнетронных установок весьма широко распространено. Они заняли прочные позиции в технологиях изготовления полупроводниковых приборов и интегральных микросхем. В частности, эти системы применяются для формирования контактов на поверхности полупроводниковых и пассивных элементов схем: например, при изготовлении резистивных пленок гибридных микросхем, магнитных пленок, низкоомных контактов, создании новых многокомпонентных тонкопленочных материалов и т.д.
Компания AP Systems — партнер ЗАО Предприятие Остек — создает индивидуальные установки напыления тонких пленок различными методами под конкретные нужды клиента. Клиент получает новейшее оборудование, отвечающее всем современным стандартам качества. Специалисты компании готовы разработать индивидуальную технологию, специальную оснастку и решить стоящие перед клиентом задачи. Тщательная проработка проекта специалистами Предприятия Остек позволит добиться улучшения эффективности и технологичности производства заказчика.
Александр Иванов, [email protected], старший инженер отдела сервиса направления производства электронных компонентов ЗАО Предприятие Остек. Окончил Рязанский Государственный Радиотехнический университет с красным дипломом, инженер по специальности «физическая электроника». Работал технологом на предприятии производства лазерных и усилительных оптоволоконных систем ООО «ВОЛИУС», последние три года — инженером сервиса в ЗАО «Предприятие Остек». |
Вы можете скачать эту статью в формате pdf здесь.
www.russianelectronics.ru
Магнетронное распыление Википедия
Магнетронная распылительная система (магнетрон)Магнетронное распыление — технология нанесения тонких плёнок на подложку с помощью катодного распыления мишени в плазме магнетронного разряда — диодного разряда в скрещенных полях. Технологические устройства, предназначенные для реализации этой технологии, называются магнетронными распылительными системами или, сокращённо, магнетронами (не путать с вакуумными магнетронами — устройствами, предназначенными для генерации СВЧ колебаний).
Магнетронный разряд
Магнетронным разрядом называют диодный газовый разряд в скрещенных полях (существует область пространства в разрядном объёме, где электрическое и магнитное поля ортогональны друг другу B⊥E{\displaystyle \mathbf {B} \perp \mathbf {E} }; силовые линии магнитного поля направлены поперёк линий тока).
История открытия
В 1898 году британский исследователь Филлипс описал появление кольцеобразного электрического разряда, возникающего вокруг зазора между стержневыми электродами в стеклянной колбе при пониженном давлении при включении осевого магнитного поля. В 1913 году проф. Струтт интерпретировал филлипсовский разряд как электрический разряд в скрещенных полях — аксиальном магнитном поле и радиальном электрическом. Он предположил, что радиальное электрическое поле создаётся положительным зарядом, накопленным за время предыдущего разряда на стенке колбы напротив зазора между электродами, а ионизация газа вызвана отрицательными частицами за время их удлинённого пробега поперёк магнитного поля от оси к стенке колбы. Струтт установил кольцевой анод вокруг торцов стержневых электродов и получил устойчивый кольцевой разряд. Наибольший вклад в изучение магнетронного разряда был внесён голландским физиком Ф. М. Пеннингом. Наряду с другими применениями магнетронного разряда (в качестве ионного источника, датчика измерения вакуума, ионного насоса), им было предложено применение магнетронного разряда для распыления и нанесения покрытий[1].
Физические основы
С точки зрения механизма эмиссии электронов, магнетронный разряд постоянного тока представляет собой аномальный тлеющий разряд. Электроны покидают поверхность катода за счёт ионно-электронной эмиссии под действием ионной бомбардировки. В связи с тем, что коэффициент ионно-электронной эмиссии весьма мал, ионный ток на катод превышает электронный как минимум на порядок. Баланс заряженных частиц в плазме обеспечивается ионизацией нейтральных атомов газа электронами, ускоренными электрическим полем в тёмном катодном пространстве.
Принцип работы магнетронаВ отличие от тлеющего разряда, где электрон, не испытывающий столкновений, будет свободно ускоряться электрическим полем, пока не покинет область катодного падения потенциала (тёмное катодное пространство), наличие поперечного магнитного поля заставляет электрон искривлять свою траекторию под действием силы Лоренца. При достаточной величине магнитного поля электрон вернётся на катод с почти нулевой энергией и вновь начнёт ускоренное движение под действием электрического поля. Траекторией его движения будет циклоида, электрон дрейфует вдоль поверхности катода в направлении, перпендикулярном как электрическому, так и магнитному полю. Электрон находится в «ловушке», покинуть которую он может, только совершив столкновение с другой частицей. Тогда он перейдёт на новую траекторию, расположенную чуть дальше от катода и так до тех пор, пока не ослабнут поля, магнитное — за счёт удаления от полюсов магнитной системы, электрическое — за счёт плазменной экранировки. За счёт наличия ловушки многократно возрастает эффективность ионизации эмитированными электронами, что позволяет, в отличие от обычного диодного разряда, получать высокую плотность ионного тока, а значит, и высокие скорости распыления при относительно низких давлениях порядка 0,1 Па и ниже. Для того, чтобы ловушка работала эффективно, необходимо исключить утечку электронов на анод вдоль силовых линий магнитного поля, а траектории дрейфа должны быть замкнуты.
Основы технологии
Технологическое значение магнетронного распыления заключается в том, что бомбардирующие поверхность катода (мишени) ионы распыляют её. На этом эффекте основаны технологии магнетронного травления, а благодаря тому, что распылённое вещество мишени, осаждаясь на подложку, может формировать плотную плёнку наиболее широкое применение получило магнетронное напыление.
Распыление мишени
При столкновении ионов с поверхностью мишени происходит передача момента импульса материалу[2][3]. Падающий ион вызывает каскад столкновений в материале. После многократных столкновений импульс доходит до атома, расположенного на поверхности материала, и который отрывается от мишени и высаживается на поверхности подложки. Среднее число выбитых атомов на один падающий ион аргона называют эффективностью процесса, которая зависит от угла падения, энергии и массы иона, массы испаряемого материала и энергии связи атома в материале. В случае испарения кристаллического материала эффективность также зависит от расположения кристаллической решетки.
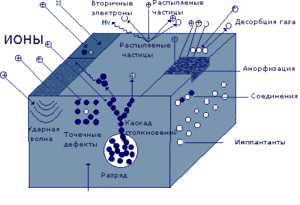
Покидающие поверхность мишени частицы осаждаются в виде плёнки на подложке, а также частично рассеиваются на молекулах остаточных газов или осаждаются на стенках рабочей вакуумной камеры.
Напыление металлов и сплавов
Напыление металлов и сплавов производят в среде инертного газа, как правило, аргона. В отличие от технологии термического испарения, при магнетронном распылении не происходит фракционирования мишеней сложного состава (сплавов).
Реактивное напыление
Для напыления сложных соединений, например оксидов и нитридов, применяется так называемое реактивное магнетронное напыление. К плазмообразующему газу (аргону) добавляют реактивный газ (например, кислород или азот). В плазме магнетронного разряда реактивный газ диссоциирует, высвобождая активные свободные радикалы, которые взаимодействуют с осаждёнными на подложку распылёнными атомами, формируя химическое соединение.
Магратрон
В советской литературе некоторое время встречался также термин «Магратрон». Слог «Маг» сокращённо означало магнетронное, «ра» — распылительное, «трон» — электроразрядное устройство. В связи с его непереводимостью на иностранные языки, термин не прижился, вместо него стали использовать слово «магнетрон».
См. также
Примечания
Литература
- Данилин Б.С., Сырчин В.К. Магнетронные распылительные системы. — М.: Радио и связь, 1982. — 72 с.
- Кузьмичёв А. И. Магнетронные распылительные системы. — Киев: «Аверс», 2008.
- Sigmund P. Mechanisms and theory of physical sputtering by particle impact // Nuclear Instruments and Methods in Physics Research Section B Beam Interactions with Materials and Atoms. — 1987. — Vol. 27. — P. 1—20. — DOI:10.1016/0168-583X(87)90004-8.
- Behrisch R. Sputtering by Particle bombardment: Experiments and Computer Calculations from Threshold to Mev Energies / под ред. Eckstein W.. — Берлин: Springer, 2007.
- Ивановский Г. Ф., Петров В. И. Ионно-плазменная обработка материалов. — М.: Радио и связь, 1986.
- Данилин Б.С. Применение низкотемпературной плазмы для нанесения тонких пленок. — М.: Энергоатомиздат, 1989. — 328 с.
wikiredia.ru
Магнетронное напыление
Магнетронное напыление
Содержание
Введение
Глава 1. Характеристики процесса ионного распыления
.1 Зависимость коэффициента распыления от энергии ионов
.2 Зависимость коэффициента распыления от угла падения ионов
.3 Ионная бомбардировка мишени
.4 Обратное рассеивание (отражение) ионов
.5 Особенности ионного распыления в присутствии реакционного газа
.6 Столкновительный характер движения атомных частиц (ионов) в газе
Глава 2. Вакуумное технологическое оборудование
Глава 3. Исследования поверхности Тi
.1 Освоить процесс магнетронного напыления тонких пленок Тi
.2 Измерения толщины тонких пленок Тi/Si
Заключение
Список литературы
ВВЕДЕНИЕ
Получение высококачественных тонких пленок титана является одной из актуальных задач технологии изготовления различных элементов микроэлектроники.
В настоящее время наиболее перспективными методами нанесения покрытий являются вакуумно-плазменные методы. Это обусловлено их экологической безопасностью, высокой чистотой технологических процессов и качеством продукции. Также известно, что в ионизованном или возбужденном состоянии атомы и молекулы легче взаимодействуют друг с другом, делая процесс нанесения покрытий более эффективным.
Существующие методы осаждения тонких пленок с использованием ионного распыления и дают возможность получать пленки различных материалов (в том числе тугоплавких и многокомпонентного состава), которые практически невозможно получить термовакуумным методом. Ионный методы осаждения пленок дают возможность создания установок и линий непрерывного действия и позволяют осуществить полную автоматизацию всего цикла получения покрытия. Развитие процессов получения тонких пленок идет в направлении повышения качества пленок (снижение загрязнений) и повышения производительности процессов.
Этот метод относится к области высоких технологий и находит самое широкое применение в современном производстве.
На первый план курсовой работы выступает задача получение высококачественных тонких пленок титана, а так же исследования толщины пленки с помощью конфокальной микроскопии. Поэтому абсолютно очевидной является важность изучения и применения модернизированной установке УВН-71-П3
Глава 1. Характеристики процесса ионного распыления
Ионное распыление - это процесс кинетического выбивания атомов с поверхности твёрдого тела (мишени) за счёт передачи импульсов от ионов к атомам мишени при бомбардировке её поверхности ионами. В чистом виде этот процесс изучают, помещая мишень в вакуум и подвергая её бомбардировке ионами из специально сформованного ионного пучка.
Ионное распыление в условиях газового разряда - более сложный процесс, поскольку поверхность мишени подвергается воздействию не только ионов рабочего газа, но и других высокоэнергетичных частиц, включая атомы после перезарядки ионов и фотоны из разрядной плазмы. На поверхности мишени, находящейся в газовой среде, где имеются реакционно-активные добавки, одновременно происходят химические реакции, влияющие на ход процесса распыления. Примером может быть распыление в аргоне не очень высокой чистоты, где примеси кислорода или паров воды окисляют поверхность мишени и изменяют скорость распыления.
Когда речь идёт о системах, где мишень одновременно является катодом газового разряда, часто используют термин катодное распыление, имея в виду при этом, что распыление мишени есть результат воздействия всех частиц, попадающих на катод.
Коэффициент распыления S определяется по формуле
= Na/Ni(1.1)
где Na - количество распылённых атомов, Ni - количество ионов, бомбардирующих распыляемую поверхность.
Если поверхность бомбардируют различные ионы и высокоэнергетичные нейтральные частицы (атомы после перезарядки ионов), то следует определять коэффициенты распыления для отдельных видов бомбардирующих частиц. В табл.1.1 приведено значение коэффициента S для иона Аr + с энергией ?i = 600 эВ.
Ионное распыление начинается, когда энергия ?i превышает пороговое значение ? пор. Величина ? пор слабо зависит от массы сталкивающихся частиц и находится в диапазоне 10- 30 эВ. При ?i < ? пор распыление атомов мишени не происходит, но возможна десорбция поверхностных загрязнений и химические реакции с ними. Коэффициент распыления зависит от многих факторов. Коэффициенты распыления различных материалов Ti=0,6 при ?i=600эВ
1.1 Зависимость коэффициента распыления от энергии ионов
Зависимость S от энергии ионов ?i: на рис. 1.1 приведена зависимость S(?i) для энергий от десятых долей до десятков килоэлектронвольт. Как видно, при энергиях до 70-80 эВ функция S(?i) быстро нарастает, затем скорость роста постепенно снижается, и при 10-40 кэВ наступает насыщение. Энергетическую эффективность процесса ионного распыления можно оценить величиной ?, равной отношению массы материала, распыляемого в единицу времени с единицы площади, к плотности мощности ионной бомбардировки. Последний параметр определяется произведением плотности ионного тока на напряжение, ускоряющее ионы. Максимальное значение я достигается при энергии ионов 300-450 эВ. При этой энергии наибольшая её часть расходуется на процесс распыления материалов.
Рис. 1.1 Зависимости коэффициента ионного распыления от энергии ионов Аr+ для разных металлов (а) и меди (б)
Зависимость S от угла падения ионов ?: при увеличении ? от 0 до 40-70° наблюдается рост S в соответствии с аппроксимационной формулой (1.2):
(?) = S(0)соs-1 ?,(1.2)
где S(0) - коэффициент распыления при нормальном падении ионов на мишень. При дальнейшем увеличении ? величина S снижается и при ? = 90° практически равна нулю. В магнетронном разряде, как правило, ? = 0, поскольку граница разрядной плазмы, служащая эмиттером ионов, идёт параллельно поверхности мишени (катода), а силовые линии электрического поля в слое между катодом и плазмой представляют собой прямые, перпендикулярные поверхности мишени.
1.2 Зависимость коэффициента распыления от угла падения ионов
Зависимость S от массы бомбардирующих ионов Мi : коэффициент распыления S увеличивается с возрастанием Mi и атомного номера иона в области энергий, характерных для магнетронного разряда. На практике чаще всего в качестве рабочего газа, из которого образуют ионы, используют аргон, который достаточно хорошо распыляет материалы и относительно дешёвый.
Зависимость S от атомного номера распыляемого материала имеет сложный периодический характер; в пределах периода таблицы Д.И. Менделеева S возрастает по мере заполнения электронных d-оболочек.
Зависимость S от температуры мишени отсутствует в диапазоне от нуля до нескольких сотен градусов.
Распылённые частицы обладают значительной кинетической энергией (~1-10эВ), благодаря которой они способны перемещаться на большие расстояния от мишени. Если на пути частиц располагается подложка, они конденсируются на ней, образуя слой из распылённого материала мишени. Этот процесс, собственно, и лежит в основе ионной технологии нанесения тонких плёнок.
На рис. 1.2 приведены распределения по энергиям атомов алюминия и вольфрама, распылённых ионами аргона. Энергия распылённых частиц значительно превосходит энергию частиц, полученных путём термовакуумного испарения, которая порядка 0,1 эВ. Повышенная энергия распылённых частиц приводит к энергетической активации процесса конденсации частиц на подложке и существенно влияет на свойства получаемых тонких плёнок. В частности, повышается адгезия плёнок к подложке и уплотняется их структура.
При бомбардировке мишеней сложного состава распылённые частицы могут быть не только в виде отдельных атомов, из которых состоит вещество мишени, но и молекулярных образований. При распылении оксидов и нитридов в инертном газе конденсат на подложке не будет полностью соответствовать химическому составу мишени из-за частичной диссоциации распылённых молекул и потери ими кислорода и азота. Чтобы восстановить стехиометрию состава плёнок распыление проводят в смеси аргона с соответствующим реакционным газом.
Ионная бомбардировка мишени приводит к распылению материала не только в виде нейтральных атомов и молекул, но и в виде ионов. Доля ионов весьма мала и в большинстве случаев ею можно пренебречь, но распылённые нейтральные частицы могут ионизоваться в разрядном промежутке, и в таком случае их доля в потоке вещества, прибывающем к подложке, может достигать десятков процентов.[1]
1.3 Ионная бомбардировка мишени
Ионная бомбардировка мишени приводит к вторичной ион-электронной эмиссии (её часто называют ?-эмиссией, т.к. она определяется коэффициентом ? в известной теории газового разряда Таунсенда). Коэффициент ? определяется отношением тока вторичных электронов к току первичных ионов. Эта эмиссия очень важна для поддержания самостоятельного разряда, если мишень является катодом разряда, используемого для генерации ионов. Условие его самоподдержания выражается уравнением (1.3):
? М = 1,(1.3)
где М - коэффициент генерации ионов в газе, определяемый количеством ионов, приходящих на катод при выходе из него одного ? -электрона. Этот коэффициент характеризует процессы ионизации газа в объёме разряда и прихода ионов на катод.
Вторичная ион-электронная эмиссия имеет две составляющие - потенциальную и кинетическую эмиссии, названные в соответствии с механизмом выхода электронов из твёрдого тела. Первый вид эмиссии происходит под действием поля ионов, подошедших к поверхности тела, и не зависит от энергии ионов. Кинетическая эмиссия обусловлена передачей ионами части своей кинетической энергии электронам; эта составляющая ? -эмиссии пропорциональна ?i , в киловольтовом диапазоне энергий ионов.
На рис. 1.3 приведены зависимости коэффициента у от энергии ионов Не+ и Аr+, бомбардирующих молибденовую мишень.
Как видно, при ?i в диапазоне сотен электронвольт, соответствующих магнетронному разряду, ? - эмиссия практически не зависит от энергии ионов, т.е. является потенциальной, а для ионов аргона величина ? ~ 0,1.
На ? -эмиссию влияют различные факторы: род ионов (см. рис. 1.3), химический состав поверхности мишени (наличие окисных плёнок, диэлектрических включений и других загрязнений) и геометрия её поверхности. Во время газового разряда в реальных технологических устройствах, особенно, в реакционной среде, коэффициент вторичной эмиссии непрерывно изменяется, поэтому литературные данные о величине ? могут использоваться только как ориентировочные.
Надо отметить, что не только ионы вызывают вторичную эмиссию мишени. Она также происходит под воздействием возбуждённых метастабильных частиц и фотонов из разрядной плазмы и вследствие бомбардировки высокоэнергетичными нейтральными частицами. Однако, потенциальная ? -эмиссия играет наибольшую роль.[2]
Ионы, бомбардирующие поверхность мишени, участвуют и в других процессах кроме вышеназванных: они нагревают тело мишени, частью проникают (имплантируются) в него или адсорбируются поверхностью, частью рассеиваются обратно.
Нагрев мишени: основная доля первичной мощности бомбардирующих ионов (~ 80 %) выделяется в виде тепла, поэтому мишени распылительных устройств требуют принудительного охлаждения. Мощность, расходуемая непосредственно на распыление материала мишени, не превышает 5 %, а расход остальной части мощности связан с внедрением ионов в тело мишени, её радиационными повреждениями, обратным рассеиванием ионов, вторичной электронной эмиссией и электромагнитным излучением. Таким образом, энергетический КПД распылительных устройств не высок и составляет всего лишь несколько процентов.
Имплантация ионов в мишень и их адсорбция: поскольку энергия ионов в магнетронном разряде не превышает 1 кэВ, ионы внедряются только в тонкий приповерхностный слой, затем они, а также адсорбированные ионы, освобождаются в нейтрализованном состоянии (в виде атомов) в процессе дальнейшего ионного распыления и десорбируются.[7]
1.4 Обратное рассеивание (отражение) ионов
Обратное рассеивание (отражение) ионов: часть ионов при ударе о поверхность мишени рассеивается обратно в виде нейтральных атомов рабочего газа. Доля же обратно рассеянных ионов, которые сохранили свой заряд, составляет малую величину (~ 10-3), поэтому их можно не принимать во внимание. Коэффициент отражения зависит от энергии первичных ионов, рода ионов и материала мишени. Для ионов аргона в условиях магнетронного разряда его величина может достигать 20 %, а в среднем она порядка нескольких процентов. При нормальном падении ионов обратно рассеянные атомы распределяются по углам вылета по закону косинуса, а спектр их энергий простирается от нуля до энергии первичных ионов ?i. Средняя энергия отражённых частиц достигает 100 эВ. Обратно рассеянные атомы летят в сторону подложки и могут передавать ей значительную энергию. Так, при осаждении алюминия со скоростью 0,6 мкм/мин с помощью магнетронного разряда в среде аргона плотности мощностей, передаваемых подложке, составляет:
за счёт конденсации атомов Al около 1,7 Дж/(мин*см2),
за счёт кинетической энергии распылённых атомов Al примерно 4,4 Дж/(мин*см2),
за счёт кинетической энергии обратно рассеянных атомов Аr - около 1,5 Дж/(мин*см2).[3]
1.5 Особенности ионного распыления в присутствии реакционного газа
Распыление в присутствии реакционного газа (кислорода, азота и др.) применяется для нанесения плёнок оксидов, нитридов и других соединений газообразных химических элементов с металлами и полупроводниками. Подобный процесс называют реакционным распылением. Он необходим вследствие того, что из-за диссоциации распыляемых соединений практически невозможно получить плёнки того же химического состава, как и мишень, если в технологической камере отсутствует соответствующий газ.
Напуск газа в камеру и его активировка в магнетронном разряде способствуют получению плёнок с химическим составом, близком к стехиометрическому (Al2O3, A1N, ТiO2, TiN, SiO2, Si3N4 и т.д.), даже при распылении элементарных мишеней. Однако присутствие реакционного газа сказывается на состоянии поверхности мишени и газовой среды в камере - проявляются эффекты "отравления" мишени и геттерирования (поглощения) реакционного газа. Эти эффекты существенно влияют на процесс распыления мишени. Термин "отравление" означает, что на поверхности мишени образуется слой (плёнка) из продукта реакции распылённого и обратно рассеянного материала мишени (металла) с газом - оксида, нитрида и т.д.
На рис. 1.4 представлены известные из многих работ зависимости парциального давления реакционного газа и скорости распыления металлической мишени от величины потока реакционного газа, подаваемого в камеру. Для примера в качестве такого газа взят кислород. Зависимости имеют три характерных области или режима: режимраспыления металла (М), в котором металлическая мишень практически не "отравлена"; режим (Р) явного реакционного распыления, в котором мишень сильно "отравлена" и распыляется соединение металла с газом; гистерезисная переходная область (П). В режиме М скорость распыления и геттерирование реакционного газа - максимальные. Наоборот, в режиме Р они - минимальные, поскольку коэффициент распыления оксидных и нитридных соединений существенно ниже коэффициента распыления чистого металла. Состав осаждаемой плёнки на подложке: в режиме М - близкий к материалу мишени, но с примесями газового элемента; в режиме Р - близкий к стехиометрическому. Режим П - нестабильный с сильно выраженным гистерезисом. Стрелки на графиках показывают, как ведёт себя распылительная система при увеличении потока напускаемого реакционного газа или его уменьшении. Реальные характеристики зависят от многих факторов (рода газа, материала мишени, плотности тока, параметров откачки, способа стабилизации рабочего режима).[4]
1.6 Столкновительный характер движения атомных частиц (ионов) в газе
Рассмотрение процесса ионного распыления в газовом разряде не будет полным, если не упомянем о столкновительном характере движения ионов в слое пространственного заряда около мишени, а также распылённых частиц и отражённых атомов (нейтрализовавшихся ионов) в газе в направлении подложки.
Ионы, попадающие на мишень, т.е. на катод, ускоряются в прикатодном слое положительного пространственного заряда. Этот слой также называют тёмным катодным пространством, поскольку газ в нём светится намного слабее, чем в разрядной плазме. Слой автоматически образуется около катода в любом разряде из-за малой подвижности ионов, и он обеспечивает ускорение не только ионов, но и катодных электронов в обратном направлении. Падение напряжения на этом слое примерно равно разрядному напряжению U, и если ионы при своём движении не сталкиваются с газовыми молекулами, их энергия на катоде равна qU, где q - заряд иона. При встрече с молекулами газа ионы совершают упругие и неупругие столкновения: первые приводят к их отклонению от первоначального направления движения и потери части кинетической энергии; вторые при тех условиях, которые имеют место в распылительных системах, связаны с перезарядкой ионов, при которой ионы превращаются в нейтральные частицы с сохранением вектора своей скорости, а газовые молекулы превращаются в ионы с начальной энергией, соответствующей тепловой энергии молекул газа. Затем нейтральные частицы летят к мишени-катоду по инерции, а ионы начинают ускоряться до нового столкновения с газовой молекулой или мишенью. Для реакции перезарядки ионов Аr+ в собственном газе можно записать следующее уравнение
+ + Ar0 = Аr0 + Аr(1.4)
Таким образом, движение ионов в катодном слое носит эстафетный характер, а катодное распыление обусловлено бомбардировкой ионами и нейтральными частицами. Чем ниже давление рабочего газа и тоньше катодный слой, тем меньше роль этих эффектов.[6]
Рассмотрим движение распылённых частиц и отражённых нейтрализовавшихся ионов через газ в направлении подложки. Указанные частицы при движении в газе совершают столкновения с газовыми молекулами и рассеиваются с потерей энергии направленного движения. При достаточно больших значениях pdм-п a, где р - давление рабочего газа в пространстве мишень-подложка, dм-п - расстояние между мишенью и подложкой, эти частицы полностью теряют направленное движение и термализуются, т.е. замедлятся до тепловых скоростей, соответствующих температуре газа. После этого распылённые частицы будут двигаться в режиме диффузии по закону "броуновского" движения. Величина pdм-п диф., при которой устанавливается диффузионный режим с термализацией высокоэнергетичных частиц, зависит от соотношения масс распылённых и отражённых высокоэнергетичных частиц и молекул газа. Чем больше масса сталкивающихся частиц, тем быстрее устанавливается такой режим. Ориентировочное значение pdм-п диф. для разных газов и материалов мишени составляет 200-600 Па*см.
При значениях pdм-п < pdм-п диф имеет место обратное рассеивание распылённых и отражённых частиц на газовых молекулах с частичной потерей энергии. Обратное рассеивание с возвратом части распылённых атомов на мишень приводит к уменьшению коэффициента распыления, и в целом оно снижает скорость осаждения тонких плёнок на подложку. Иногда столкновительный режим переноса распылённых атомов применяют для нанесения относительно равнотолщинных слоёв на подложки со сложным рельефом, запыления их обратной стороны, а также для получения нанокластеров из атомов мишени и аэрозолей в газовой фазе. Термализацию высокоэнергетичных частиц применяют в случаях, когда необходимо осаждать слои на структуры, чувствительные к таким частицам.
ионный атомный магнетронный вакуумный
Глава 2. Вакуумное технологическое оборудование
Вакуумные технологические методы широко используются в производстве полупроводниковых материалов, элементов и интегральных схем, поскольку позволяют изолировать технологические процессы от неблагоприятного воздействия атмосферы и существенно улучшить качество получаемой продукции, увеличить выход годных.
В данной работе использовали модернизированную установку вакуумного напыления УВН-71-П3.
Основными элементами установки вакуумного напыления, упрощенная схема которой представлена на рис. 1.5, являются: 1 - вакуумный колпак из нержавеющей стали; 2 - заслонка; 3 - трубопровод для водяного нагрева или охлаждения колпака; 4 - игольчатый натекатель для подачи атмосферного воздуха в камеру; 5 - нагреватель подложки; 6 - подложкодержатель с подложкой, на которой может быть размещен трафарет; 7 - герметизирующая прокладка из вакуумной резины; 8 - магнетрон с размещённой на нём мишенью из распыляемого материала.
Модернизация установки состояла в том, что вместо двух испарителей были установлены магнетроны (рис. 1.6), Так же претерпела изменения система газонапуска (теперь газ поступает на каждый магнетрон в отдельности), усовершенствовалась система управления установкой и конструкция механизма заслонки.[5]
Глава 3. Исследования поверхности Тi
.1 Освоить процесс магнетронного напыления тонких пленок Тi
Изготовление образцов выполнено в установке вакуумного напыления УВН-2М Процесс проведения операции вакуумного напыления включает в себя выполнение следующих действий. В верхнем положении колпака в камеру помешается «карусель» с загруженными на нее подложками. Затем колпак опускается и включается система вакуумных насосов (вначале для предварительного разрежения, затем высоковакуумный). По достижении давления внутри камеры порядка 4,7*10-3 Па включается нагреватель подложек в течение 5 , одновременно с этим на колпак и магнетроны подается охлаждение. По окончанию времени включается блок питания, производится газонапуск и зажигается плазменный разряд. Вначале операция напыления производится на заслонку, что позволяет удалить с поверхности мишени различные окислы и загрязнения. Затем заслонка открывается, и напыление ведется непосредственно на пластины. Магнетронное напыление Ti, происходящее в среде аргона. Данный слой обладает хорошей адгезией с кремниевой подложкой. Длительность процесса составляет от толщины напыляемой пленки для выполнения курсовой необходима напылить 3 образца с разным временем 10,15,25 минутами при напряжении 480 В и токе 2 А
3.2 Измерения толщины тонких пленок Тi/Si
Метод исследования поверхности твердых тел является конфокальная микроскопия, которая позволяет резко увеличить точность измерений неровности поверхности в вертикальном направлении, при этом разрешение в горизонтальном направлении остается на уровне традиционных оптических микроскопов. Такое соотношение в разрешении в двух взаимно перпендикулярных направлениях позволяет получать новую, достаточно уникальную информацию, которую невозможно получить даже при использовании сканирующей электронной микроскопии с высоким разрешением.
В качестве примеров можно привести снимки сечения границы раздела термически напыленного слоя Тi.
На рис. 1.7 и 1.8, видна граница напыленного слоя, находящаяся на буртике, который представляет собой резкое поднятие материала подложки вблизи этой границы. Толщина металлизации составляет примерно 5 мкм для 3-образца а для 2 образца 6мкм. Из рис. 1.9 2.1 видно, что перед краем сплава имеется поднятие материала подложки (образуется буртик), одинаовой длиной 0,6мм а после края (при Х в диапазоне 4 мкм ) имеется снижение уровня поверхности подложки с напыленным слоем сплава.
Рис. 1.7 Сечение слоя сплава на подложке в изометрии
Рис. 1.8 Характерные размеры напыления
Рис. 1.9 Высота буртика(3 образец)
Рис. 2.1 Высота буртика(3 образец)
Заключение
Метод магнетронного распыления различных материалов для нанесения высококачественных тонких плёнок и покрытий является одним из важнейших для электроники, оптики, машиностроения и других отраслей, включая автомобилестроение и архитектуру. Метод хорошо освоен в промышленности и часто применяется в научных исследованиях. Он является серьезной альтернативой электронно-лучевому и вакуумно-дуговому испарению, а также экологически вредному гальваническому осаждению. Имеется большой парк магнетронного оборудования, который постоянно обновляется и совершенствуется. Многие технологические установки полностью автоматизированы и являются системами непрерывного действия. Из-за большой потребности в установках магнетронного распыления их общемировой объём продаж составляет сотни миллионов долларов в год.
Накоплена значительная информация о физических процессах в магнетронном разряде и связи параметров технологического процесса с характеристиками получаемых плёнок и покрытий. Созданы физические и математические модели разряда и технологических процессов.
Однако, несмотря на большие успехи в магнетронной технологии нельзя сказать, что решены все проблемы, которые присущи этому методу. Например, в некоторых случаях применению магнетронного распыления препятствует относительно неравномерное покрытие сложного профиля подложки или невысокая скорость осаждения покрытий, далеко неполное использование материала мишеней или присутствие распыляющего газа в составе конденсатов. Для преодоления этих и других недостатков требуются дополнительные исследования и разработки.
Также нельзя сказать, что уровень понимания физики магнетронного разряда и его математическое описание полностью удовлетворяют инженеров-разработчиков нового технологического оборудования. Поэтому необходимо продолжать изучение этого вида разряда, главным образом, его физики и химии на микроскопическом уровне. Макроскопические параметры и характеристики уже известны. Актуальным является создание программного обеспечения для проектирования МРС (расчётов электрических, газовых и тепловых характеристик, переноса распылённого вещества на подложку, выработки мишеней).
Постоянно возникают новые направления в науке и технике, которые нуждаются в новых технологиях. Так, сейчас на повестке дня стоит задача разработки нанотехнологий для производства объектов с элементами нанометрового размера. Анализ показывает, что магнетронное распыление является потенциально эффективным и в этой области.
Оно позволяет получать одно-, двух- и трёхмерные нанообъекты (нанослои, наноструктурные материалы и нанокомпозиты, наночастицы) для наноэлектроники, нанофотоники, наносенсорной техники, создания "умных" материалов и материалов с модулируемыми свойствами.
Это возможно благодаря высокому уровню управляемости ионного распыления и воздействия на конденсат, неравновесности процессов формирования плёнок и покрытий, возможности формировать импульсные потоки вещества, ограниченные во времени, но имеющие большую плотность.
Таким образом, из всего сказанного можно сделать вполне обоснованное заключение о перспективности магнетронного распыления и важности его дальнейшего развития.
Список литературы
1.Кузьмичёв А.И., Магнетронные распылительные системы, Киев: Аверс, 2008
2.Холлэнд JI., Нанесение тонких плёнок в вакууме, М.: Госэнергоиздат, 1963.
3.Данилин Б.С., Сырчин В.К., Магнетронные распылительные системы, М.: Радио и связь, 1982.
4.Берлин Е., Двинин С., Сейдман Л., Вакуумная технология и оборудование для нанесения и травления тонких пленок, М.: Техносфера, 2007.
.Жуков В.В., Кривобоков В.П., Янин С.Н., Распыление мишени магнетронного диода в присутствии внешнего ионного пучка, Журнал технической физики, 2006, том 76, вып. 4.
.Майссел Л., Глэнг Р., Технология тонких пленок. Справочник, пер, с англ, под ред,, Елинсона М.И., Смолко Г.Г., М.: Советское радио, 1977.
.Моргулис Н. Д., Катодное распыление, Успехи физических наук, 1946, т. 28.
Теги: Магнетронное напыление Курсовая работа (теория) ФизикаПросмотров: 35994Найти в Wikkipedia статьи с фразой: Магнетронное напылениеdiplomba.ru