Пленочные конденсаторы. Пленка в конденсаторе
Пленочные конденсаторы, теория и примеры
Определение и общие сведения о пленочных конденсаторах
Часто диэлектриком в пленочных конденсаторах служат: тефлон, поликарбонат, металлизированная бумага, полиэстер. Плёночные конденсаторы разделяют в зависимости от материала диэлектрика, например, выделяют полистирольные, фторопластовые, полипропиленовые и другие конденсаторы. Электродами в таких конденсаторах часто служит фольга. Иногда диэлектрик не разделяют слоями фольги, а металлизируют.
Емкости данного типа конденсаторов изменяются от нескольких пикофарад до сотен микрофарад.
Как известно, электрическая емкость конденсатора зависит от площади его обкладок. Для компактного вмещения наибольшей площади и применяют пленочные конденсаторы. При этом используют принцип многих слоев, создавая конденсатор из множества слоев диэлектрика, разделенного обкладками. Рабочее напряжение пленочных конденсаторов варьируется в широком диапазоне. Иногда конденсаторы рассматриваемого типа имеют номинальное напряжение более чем 2 кВ.
По способу размещения слоев диэлектрика и обкладок пленочные конденсаторы делят на радиальные и аксиальные.
Одним их самых важных свойств пленочных конденсаторов считается их способность к самовосстановлению. Данное свойство обеспечивает высокую надежность этого типа конденсаторов, в сравнении с другими конденсаторами. Кроме этого пленочные конденсаторы обладают высокой тепловой стабильностью. Пленочные конденсаторы технологически изготовлены так, что они имеют высокое постоянство основных параметров при изменении приложенного напряжения. Они имеют высокую нагрузку по переменному току, что имеет большое значение для уменьшения нагрева элемента во время работы. Пленочные конденсаторы — это одно из лучших решений при наличии высокочастотных импульсных токов.
Примеры решения задач
Понравился сайт? Расскажи друзьям! | |||
ru.solverbook.com
Виды конденсаторов и их применение
Конденсатор - это электрический (электронный) компонент, состоящий из двух проводников (обкладок), разделенных между собой слоем диэлектрика. Существует много видов конденсаторов. В основном они делятся по материалу из которого изготовлены обкладки и по типу используемого диэлектрика между ними.
Виды конденсаторов
Бумажные и металлобумажные конденсаторы
У бумажного конденсатора диэлектриком, разделяющим фольгированные обкладки, является специальная конденсаторная бумага. В электронике бумажные конденсаторы могут применяться как в цепях низкой частоты, так и в высокочастотных цепях.
Хорошим качеством электрической изоляции и повышенной удельной емкостью обладают герметичные металлобумажные конденсаторы, у которых вместо фольги (как в бумажных конденсаторах) используется вакуумное напыление металла на бумажный диэлектрик.
Бумажный конденсатор не имеет большую механическую прочность, поэтому его начинку помещают в металлический корпус, служащий механической основой его конструкции.
Электролитические конденсаторы
В электролитических конденсаторах, в отличии от бумажных, диэлектриком является тонкий слой оксида металла, образованный электрохимическим способом на положительной обложке из того же металла.
Вторую обложку представляет собой жидкий или сухой электролит. Материалом, создающим металлический электрод в электролитическом конденсаторе, может быть, в частности, алюминий и тантал. Традиционно, на техническом жаргоне «электролитом» называют алюминиевые конденсаторы с жидким электролитом.
Но, на самом деле, к электролитическим также относятся и танталовые конденсаторы с твердым электролитом (реже встречаются с жидким электролитом). Почти все электролитические конденсаторы поляризованы, и поэтому они могут работать только в цепях с постоянным напряжением с соблюдением полярности.
В случае инверсии полярности, может произойти необратимая химическая реакция внутри конденсатора, ведущая к разрушению конденсатора, вплоть до его взрыва по причине выделяемого внутри него газа.
К электролитическим конденсаторам так же относится, так называемые, суперконденсаторы (ионисторы) обладающие электроемкостью, доходящей порой до нескольких тысяч Фарад.
Алюминиевые электролитические конденсаторы
В качестве положительного электрода используется алюминий. Диэлектрик представляет собой тонкий слой триоксида алюминия (Al2O3),
Свойства:
- работают корректно только на малых частотах;
- имеют большую емкость.
Характеризуются высоким соотношением емкости к размеру: электролитические конденсаторы обычно имеют большие размеры, но конденсаторы другого типа, одинаковой емкости и напряжением пробоя были бы гораздо больше по размеру.
Характеризуются высокими токами утечки, имеют умеренно низкое сопротивление и индуктивность.
Танталовые электролитические конденсаторы
Это вид электролитического конденсатора, в которых металлический электрод выполнен из тантала, а диэлектрический слой образован из пентаоксида тантала (Ta2O5).
Свойства:
- высокая устойчивость к внешнему воздействию;
- компактный размер: для небольших (от нескольких сотен микрофарад), размер сопоставим или меньше, чем у алюминиевых конденсаторов с таким же максимальным напряжением пробоя;
- меньший ток утечки по сравнению с алюминиевыми конденсаторами.
Полимерные конденсаторы
В отличие от обычных электролитических конденсаторов, современные твердотельные конденсаторы вместо оксидной пленки, используемой в качестве разделителя обкладок, имеют диэлектрик из полимера. Такой вид конденсатора не подвержен раздуванию и утечки заряда.
Физические свойства полимера способствуют тому, что такие конденсаторы отличаются большим импульсным током, низким эквивалентным сопротивлением и стабильным температурным коэффициентом даже при низких температурах.
Полимерные конденсаторы могут заменять электролитические или танталовые конденсаторы во многих схемах, например, в фильтрах для импульсных блоков питания, или в преобразователях DC-DC.
Пленочные конденсаторы
В данном виде конденсатора диэлектриком является пленка из пластика, например, полиэстер (KT, MKT, MFT), полипропилен (KP, MKP, MFP) или поликарбонат (KC, MKC).
Электроды могут быть напыленными на эту пленку (MKT, MKP, MKC) или изготовлены в виде отдельной металлической фольги, сматывающейся в рулон или спрессованной вместе с пленкой диэлектрика (KT, KP, KC). Современным материалом для пленки конденсаторов является полифениленсульфид (PPS).
Общие свойства пленочных конденсаторов (для всех видов диэлектриков):
- работают исправно при большом токе;
- имеют высокую прочность на растяжение;
- имеют относительно небольшую емкость;
- минимальный ток утечки;
- используется в резонансных цепях и в RC-снабберах.
Отдельные виды пленки отличаются:
- температурными свойствами (в том числе со знаком температурного коэффициента емкости, который является отрицательным для полипропилена и полистирола, и положительным для полиэстера и поликарбоната)
- максимальной рабочей температурой (от 125 °C, для полиэстера и поликарбоната, до 100 °C для полипропилена и 70 °С для полистирола)
- устойчивостью к электрическому пробою, и следовательно максимальным напряжением, которое можно приложить к определенной толщине пленки без пробоя.
Конденсаторы керамические
Этот вид конденсаторов изготавливают в виде одной пластины или пачки пластин из специального керамического материала. Металлические электроды напыляют на пластины и соединяют с выводами конденсатора. Используемые керамические материалы могут иметь очень разные свойства.
Разнообразие включает в себя, прежде всего, широкий диапазон значений относительной электрической проницаемости (до десятков тысяч) и такая величина имеется только у керамических материалов.
Столь высокое значение проницаемости позволяет производить керамические конденсаторы (многослойные) небольших размеров, емкость которых может конкурировать с емкостью электролитических конденсаторов, и при этом работающих с любой поляризацией и характеризующихся меньшими утечками.
Керамические материалы характеризуются сложной и нелинейной зависимостью параметров от температуры, частоты, напряжения. В виду малого размера корпуса - данный вид конденсаторов имеет особую маркировку.
Конденсаторы с воздушным диэлектриком
Здесь диэлектриком является воздух. Такие конденсаторы отлично работают на высоких частотах, и часто выполняются как конденсаторы переменной емкости (для настройки).
Пленочные конденсаторы | Основы электроакустики
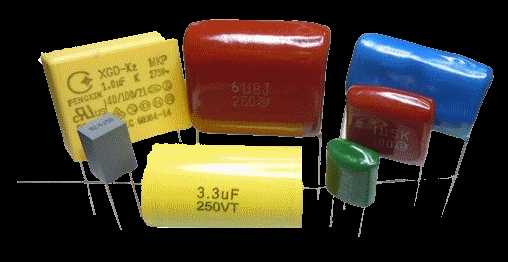
Конденсаторы рассчитаны на работу в цепях постоянного, переменного и пульсирующего токов, выпускаются на номинальное напряжение 35 и 50 В и включают 45 типономиналов с емкостью от 22 пФ до 0,1 мкф по шкале Е-12. Тангенс угла потерь этих конденсаторов в нормальных условиях ЫО-3. Срок службы до 5000 ч.
Малогабаритные металлопл ен очные конденсаторы К71П-2 выпускают на номинальное напряжение постоянного тока 100 В. Секции конденсаторов размещены в алюминиевых корпусах прямоугольной формы. Два вывода (более длинных) служат токо-отводами, а два других (коротких) — для крепления к плате. Эти конденсаторы применяют для аппаратуры с печатным монтажом. Кроме того, они могут работать в цепях переменного или пульсирующего тока частотой до 1 МГц, однако при значительном снижении амплитуды напряжения, устанавливаемого для каждой номинальной емкости. Сопротивление изоляции между выводами 50000 МОм; тангенс угла потерь 1,5 -10~3; ТКЕ в диапазоне рабочих темперааур от — 60 до +85 °С равен 120-10~6 1гС. Срок службы конденсаторов 5000 ч, хранения — 12 лет.
Конденсаторы К74-8 выпускают для. работы в цепях постоянного и пульсирующего тока. При работе в цепях пульсирующего тока амплитуда напряжения переменной составляющей при частоте 50 Гц не должна превышать 20 % номинального напряжения (при 500 Гц — 7,5%, при 1000 Гц — 5% и выше 1000 Гц до 10 кГц — 2,5 %), а сумма амплитуды напряжения переменной составляющей и постоянного напряжения — номинального напряжения. Тангенс угла потерь у этих конденсаторов при номинальной температуре составляет 0,01, диапазон рабочих температур от — 60 до +85 °С, срок службы — до 6000 ч.
audioakustika.ru
Пленочный конденсатор
Изобретение относится к электротехнике, а более конкретно к слоистым пленочным электродам для электролитических конденсаторов, слои которых имеют существенные отличия по составу и физической структуре. Техническим результатом изобретения является увеличение удельной емкости. Согласно изобретению пленочный конденсатор содержит многослойную анодную фольгу с высокоразвитой поверхностью, на которой адгезионно закреплена оболочка диэлектрика, покрытая твердым электролитом. В слое диэлектрика толщиной 2-100 нм диспергированы кластеры металла размером 0,5-50 нм, при этом между анодной фольгой и слоем твердого электролита размещено, как минимум, два слоя диэлектрика, разделенных прослойкой из кластеров металла, причем слой диэлектрика сформирован осаждением кластеров металла из гидрозоля посредством импульсных дуговых разрядов последовательно кластеров серебра и кластеров алюминия и/или титана, которые затем на поверхности оболочки окисляют, соответственно, в количестве (мас.%): 1-30 и 70-99. 2 з.п. ф-лы, 2 ил.
Изобретение относится к электротехнике, а более конкретно к слоистым пленочным электродам для электролитических конденсаторов, слои которых имеют существенные отличия по составу и физической структуре, один из которых являющийся основой, выполнен из металла, а другой, расположенный рядом с ним, выполнен из пористого материала.
Уровень данной области техники характеризует анодная пленка, изготовленная по рулонной технологии электролитических конденсаторов с использованием ионно-плазменного осаждения в вакууме вентильного металла в форме губчатого слоя на пленочную подложку слоеной основы, описанная в патенте US 6865071 В2, Н 01G 9/00, 2002 г.
Особенностью описанной анодной пленки для конденсатора является то, что на развитой поверхности алюминиевой подложки, которая предварительно очищена и протравлена посредством ионной бомбардировки, сформировано нанокомпозитное оксидное покрытие, включающее пористый вентильный металл, преимущественно алюминий, осажденный из паровой фазы в вакууме.
Автономные включения пористого алюминия дополнительно развивают рабочую поверхность токоведущего слоя анодной пленки, чем увеличивается площадь взаимодействия с электролитом и, как следствие, удельная емкость электролитического конденсатора.
Однако недостатком этой анодной пленки является функциональная ненадежность из-за возможных отслоений автономных включений пористого вентильного металла по границам раздела, через которые во время эксплуатации проходят миграционные процессы (взаимодиффузия), что в результате приводит к нестабильности показателей назначения электролитического конденсатора и заметно сокращает срок службы.
Отмеченные недостатки устранены в пленочном конденсаторе, описанном в патенте RU 2308112, Н01G 9/04, В32В 15/04, 2007 г., который по технической сущности и числу совпадающих признаков выбран в качестве наиболее близкого аналога предложенному.
Известный пленочный конденсатор представляет собой слой твердого электролита, адгезионно связанный с оксидным покрытием, имеющим включения вентильного металла, которое размещено на многослойной анодной пленке.
Анодная пленка содержит токопроводящую физически активированную подложку с развитой поверхностью и оксидное покрытие на конформном слое электрохимически активного алюминия, имеющего регулируемую объемную пористость, связанного с поверхностью подложки посредством гетероперехода, представляющего собой наноструктурированную композицию из материала подложки и напыленного вентильного металла.
Выполнение включений пористого алюминия в виде конформного слоя, подобного профилю подложки, в оксидном покрытии кратно увеличивает контактную поверхность взаимодействия с твердым электролитом пленочного конденсатора.
Оксидное покрытие в структуре пленочного конденсатора выполняет функции диэлектрика.
Под термином «диэлектрик» следует понимать непроводящий материал (например Аl2О3, полимер), так и двойной электрический слой, возникающий между двумя примыкающими средами (анодом и катодом в виде твердого электролита по описываемому варианту технического выполнения пленочного конденсатора).
Вентильный металл в виде слоя покрытия обеспечил открытость высокопористой поверхности, доступную для заполнения электролитом, что позволяет использовать в конденсаторе твердый электролит, расширяя тем самым технологические возможности применения.
Технологическое обеспечение средствами ионно-плазменного напыления вентильного металла электрохимической активности в итоге направлено на создание более толстого слоя качественного оксида для увеличения рабочего напряжения пленочного конденсатора повышенной емкости.
Наличие объемной пористости и создание ионной обработкой радиационных дефектов в слое вентильного металла приводит к повышению электрохимической активности материала, которая управляемо меняется за счет регулирования количества и размера пор в объеме напыляемого алюминия.
Сформированная таким образом пористая структура напыленного алюминиевого слоя более легко подвергается электрохимическому оксидированию, формируя слой диэлектрика, менее механически напряженного.
Пленочный конденсатор за счет улучшения механических характеристик, пластичности и адгезионной прочности монолитных соединений структурных составляющих имеет повышенную удельную емкость, напряжение функционирования более 600 В.
Однако дальнейший рост удельной емкости известного пленочного конденсатора ограничен закономерностями электротехники.
Задачей, на решение которой направлено настоящее изобретение, является усовершенствование конструкции пленочного конденсатора для повышения показателей назначения, а именно увеличения его удельной емкости.
Требуемый технический эффект достигается тем, что в известном пленочном конденсаторе, содержащем многослойную анодную фольгу с высокоразвитой поверхностью, на которой адгезионно закреплена оболочка диэлектрика, покрытая твердым электролитом, согласно изобретению, в слое диэлектрика толщиной 2-100 нм диспергированы кластеры металла размером 0,5-50 нм, при этом между анодной фольгой и слоем твердого электролита размещено, как минимум, два слоя диэлектрика, разделенных прослойкой из кластеров металла, причем слой диэлектрика сформирован осаждением кластеров металла из гидрозоля посредством импульсных дуговых разрядов последовательно кластеров серебра и кластеров алюминия и/или титана, которые затем на поверхности оболочки окисляют, соответственно в количестве (мас.%): 1-30 и 70-99.
Отличительные признаки обеспечили кратное повышение удельной электрической емкости пленочного конденсатора, выполняемого по штатной рулонной технологии на действующем оборудовании.
Каждый слой диэлектрика формируется толщиной 2-100 нм для увеличения электрической емкости анодной фольги. Функциональный слой на анодной фольге из алюминия формируется осаждением из технологического гидрозоля кластеров металлов размером 0,5-50 нм.
Минимальный размер осаждаемых кластеров металла ограничен для практического формирования оболочки диэлектрика, в которой исключены касания примыкающих слоев, нижерасположенного слоя металлического анода и вышерасположенного проводящего слоя - твердого электролита.
Толщина оболочки диэлектрика 100 нм является минимальной для гарантированного размещения в ней кластеров металла размером 50 нм.
Формировать слой диэлектрика более 100 нм нецелесообразно, потому что при этом электрические характеристики губчатого металла существенно не изменяются.
Нанесение кластеров металлов на металлическую подложку осуществляют осаждением из технологического гидрозоля, поэтому кластеры металлов размером 100 нм образуют седиментационно неустойчивую взвесь.
Кластеры металлов менее 2 нм не обеспечивают сплошности формируемого слоя, причем их изготовление технически затруднительно.
Оболочку диэлектрика толщиной менее 2 нм в виде равномерного слоя без сквозных отверстий по используемой технологии изготовить не представляется возможным.
Разделение слоев в оболочке диэлектрика прослойками из кластеров металла обеспечивает соответствующее повышение его диэлектрической проницаемости за счет увеличения поляризуемости и, как следствие, рост удельной электрической емкости изделия. Многослойность диэлектрической оболочки расширяет функциональные и технологические возможности пленочного конденсатора.
Выполнение конформного слоя диэлектрика на поверхности губчатого металла анодной пленки последовательным осаждением кластеров серебра (1-30 мас.%), а затем кластеров алюминия и/или титана (70-99 мас.%), которые с поверхности оболочки окисляют, обусловлено следующим.
Нетоковедущий слой оксидов служит матрицей диэлектрика, в которой распределены кластеры металла.
Кластеры серебра служат барьерным слоем, формирующим четкую границу примыкающих различных по функциям материалов: губчатый металл-серебро-диэлектрик, который образуется окислением алюминия и титана, расположенных на поверхности оболочки диэлектрика.
Содержание серебра менее 1 мас.% заметно не увеличивает электрофизических характеристик диэлектрика (в частности, диэлектрической проницаемости) и не образует барьерного слоя на границе раздела.
При увеличении массового содержания серебра в слое свыше 30% снижается пробивное напряжение, что ухудшает показатели назначения пленочного конденсатора.
Следовательно, каждый существенный признак необходим, а их совокупность является достаточной для достижения новизны качества, не присущей признакам в разобщенности, то есть поставленная в изобретении техническая задача решена не суммой эффектов, а новым сверхэффектом суммы признаков.
Сущность изобретения поясняется чертежами, где схематично изображены:
на фиг.1 - структура и профиль развитой поверхности пленочного конденсатора;
на фиг.2 - вид I на фиг.1.
Предложенный пленочный конденсатор представляет собой многослойную структуру, где последовательно соединены в монолитном единстве:
1 - полимерная основа;
2 - гетеропереход «основа-подложка»;
3 - подложка из вентильного металла, алюминия;
4 - губчатый слой из пористого алюминия;
5 - гетеропереход «подложка-губчатый слой»;
6 - слой кластеров алюминия;
7 - слой кластеров оксидов алюминия и/или титана;
8 - оболочка диэлектрика;
9 - твердый электролит.
Пример выполнения пленочного конденсатора, который носит чисто иллюстративный характер и не ограничивает объема притязаний совокупности существенных признаков формулы.
Пленочный рулонный материал на полиэтилентерефталатной основе 1, предварительно модифицированный рифлением поверхности и сквозными порами размером 0,2-6 мкм, помещают в вакуумную камеру на роликах, которые обеспечивают перемотку материала относительно ионно-плазменных источников для осаждения алмазоподобного нанослоя, металлического покрытия из меди или алюминия и губчатого слоя вентильного металла.
Затем вакуумную камеру закрывают и откачивают до давления 10-5 мм рт.ст.
В изолированном вакуумном объеме в ионно-лучевой источник подают углеводород в виде пара или газа (пиклогексан или метан). При работе с циклогексаном рабочее давление составляет 10-3 мм рт.ст., напряжение разряда - 3 кВ и ток, в зависимости от габаритов источника, в диапазоне от 200 мА до 500 мА.
Ионно-лучевой источник обеспечивает равномерную по ширине пленки из полиэтилентерефталата область осаждения алмазоподобного покрытия на ее поверхность.
Перемещение пленки происходит с заданной скоростью, которая определяет массу осаждаемого алмазоподобного покрытия и соответственно его толщину в пределах 5-50 нм.
Затем полимерная пленка с нанесенным алмазоподобным нанослоем поступает в другой изолированный объем, где через гетеропереход 2 происходит нанесение слоя 3 алюминия толщиной 25-250 нм.
Изоляция вакуумных объемов осуществляется с помощью специального щелевого затвора, который обеспечивает транспортировку пленки из одного объема в другой без изменения состава паровой или газовой фазы.
Нанесение слоя алюминия производят в атмосфере аргона при давлении 8×10-4-2×10-3 мм рт.ст. с помощью магнетронного устройства.
Режим работы для алюминия, серебра и меди: ток порядка 15-20 А, напряжение 500-600 В при длине магнетронного источника 420 мм.
Доращивание толщины слоя 3 вентильного металла проводят за счет электрофореза из жидкой среды, в которой находятся кластеры соответствующего металла.
Практически в качестве металлического покрытия 3 полимерной пленки 1 используется алюминий. Медь и серебро могут применяться в тех случаях, когда надо иметь более высокую теплопроводность или электрическую проводимость для снижения внутреннего сопротивления пленочного конденсатора с описываемой анодной фольгой.
Затем полимерная пленка 1 с алмазоподобным нанослоем, на который осажден слой 3 металла - подложка, поступает в следующую изолированную вакуумную камеру, где происходит нанесение губчатого слоя 4 вентильного металла толщиной 0,5-20 мкм.
Губчатый слой 4 металла, в частности алюминия, представляет собой высокопористый материал, включающий поры диаметром от десятков нанометров до микрометров в зависимости от назначения.
Для получения слоя 4 губчатого металла на основе алюминия в изолированном вакуумном объеме повышают давление в несколько раз, до 6×10-3 мм рт.ст., изменяют состав газовой смеси, добавляя в нее 30-40 об.% кислорода.
Режим работы магнетронного источника при этом: напряжение разряда 400-600 В, ток разряда 25-40 А. давление в камере рабочих модулей изменяется в диапазоне от 0,1 до 0,0001 мм рт.ст.
При этом растущий слой 4 осаждаемого на материале подложки 3 вентильного металла обрабатывается ионами аргона и кислорода, в результате чего создается гетеропереход 5 в виде наноструктурной композиции, включающей атомы пористого вентильного металла и материала подложки. Ионно-уплотненный гетеропереход обеспечивает высокую адгезию соединения осаждаемого губчатого слоя 4 алюминия с монолитным алюминием подножки 3 и служит барьером, предотвращающим миграционные процессы.
При ассистировании магнетронного напыления губчатого слоя 4 алюминия ионами инертного газа аргона стимулируется диффузия композиции гетероперехода 5, что обеспечивает равномерность взаимного распределения структурных элементов примыкающих слоев 3, 4. При этом наночастицы, состоящие из атомов токопроводящего металла подложки 3, прорастают в наночастицы напыляемого алюминия, которые образуют гетеропереход 5, адгезионный слой с барьерными свойствами.
Ассистирование ионами кислорода, химически активного газа, обеспечивает достижение управляемой электрохимической активности слоя вентильного металла. В результате на гетеропереходе 5 формируется объемно пористый слой алюминия, характеризующийся кратным увеличением поверхности подложки 3, что необходимо для взаимодействия анода с электролитом конденсатора.
Толщина слоя 4 пористого алюминия с регулируемым размером и количеством пор составляет от 0,05 до 30 мкм.
Визуально формирование губчатого слоя 4 контролируется по цвету: слой 3 монолитного алюминия имеет выраженный серебристый цвет, а губчатый слой 4 алюминия - черный.
Далее измеряется пористость и рабочие параметры изготовленной анодной фольги в зависимости от целевого применения. Пористость губчатого слоя металла может варьироваться и достигать 80-85% от общего объема слоя.
При использовании в качестве электродов для пленочных электролитических конденсаторов измеряют удельные емкостные характеристики. Для анодной фольги они не должны быть меньше 800 мкФ/см2/мкм, то есть при толщине губчатого слоя в 1 мкм и напряжении 0,5 В емкость на одном квадратном сантиметре составляет 800 мкФ.
После формовки удельная емкость для анодной фольги при напряжении 2В составляет не ниже 400 мкФ на 1 мкм толщины.
Затем проводят операцию формирования оболочки 8 диэлектрика на поверхности губчатого слоя 4 алюминия.
Полученный электродный полуфабрикат помещают в специальную ванну, содержащую гидрозоль кластеров металлов. В жидкости (дистиллированная вода или вода с ПАВ) взвешены кластеры серебра, алюминия или титана.
Размер кластеров металла выбран в диапазоне от 0,5 до 50 нм.
После этого на проводящий слой изготовленного электродного полуфабриката подают напряжение и посредством воздействия импульсных дуговых разрядов наносят тонкий слой 6 кластеров серебра, создавая барьерный слой - границу раздела между губчатым слоем 4 алюминия и оболочкой 8 диэлектрика, которую формируют далее.
Слой 6 серебра конформно располагается по поверхности губчатого слоя 4 алюминия, с которым он монолитно связывается.
После этого сверху осаждают кластеры алюминия или титана, или их смесь, которые далее подвергают оксидированию с поверхности, формируя слой 7 диэлектрика.
Затем технологическую последовательность осаждения кластеров серебра и алюминия и/или титана повторяют, формируя дополнительные слои 6 и 7, которые образуют между анодной фольгой из слоев 3, 4 алюминия и слоем 9 твердого электролита, как минимум, два слоя 7 диэлектрика (оксиды алюминия, титана), разделенных прослойкой 6 из кластеров металла (серебра).
Первый слой 7 диэлектрика получают за счет процесса электрохимического окисления (анодирования) слоев алюминия и/или титана.
Далее наносится слой жидкой керамики (Аl2О3, TixOy) по золь-гель технологии, формируя оболочку 8 заданной толщины в диапазоне 2-100 нм.
Для формирования оболочки 8 диэлектрика с использованием полимерного материала поверхность приготовленной анодной фольги обрабатывают в плазме для улучшения заполнения перового пространства при вакуумной пропитке.
Полимерную массу, содержащую кластеры металла, наносят методом полива. Затем растворитель испаряют, формируя функциональную оболочку 8.
После операций формирования оболочки 8 диэлектрика на ее поверхность наносят слой 9 твердого электролита, завершая изготовление многослойного пленочного конденсатора, как самодостаточного электротехнического устройства, пригодного для использования в приборах различного назначения.
Проведенный сопоставительный анализ предложенного технического решения с выявленными аналогами уровня техники, из которого изобретение явным образом не следует для специалиста по электротехнике, показал, что оно не известно, а с учетом возможности промышленного серийного изготовления пленочного конденсатора с многослойным анодом, можно сделать вывод о соответствии критериям патентоспособности.
1. Пленочный конденсатор, содержащий многослойную анодную фольгу с высокоразвитой поверхностью, на которой адгезионно закреплена оболочка диэлектрика, покрытая твердым электролитом, отличающийся тем, что в слое диэлектрика толщиной 2-100 нм диспергированы кластеры металлов размером 0,5-50 нм.
2. Пленочный конденсатор по п.1, отличающийся тем, что между анодной фольгой и слоем твердого электролита размещено как минимум два слоя диэлектрика, разделенных прослойкой из кластеров металла.
3. Пленочный конденсатор по п.1 или 2, отличающийся тем, что слой диэлектрика сформирован осаждением кластеров металла из гидрозоля посредством импульсных дуговых разрядов, последовательно кластеров серебра и кластеров алюминия и/или титана, которые затем на поверхности оболочки окисляют соответственно в количестве, мас.%: 1-30 и 70-99.
www.findpatent.ru
Пленочный конденсатор
Изобретение относится к электротехнике, а более конкретно к слоистым пленочным накопителям электрической энергии - электролитическим конденсаторам, композиционные слои которых существенно отличаются по составу и физической структуре. Пленочный конденсатор содержит разделенные диэлектриком пакетные электроды, полимерное основание которых выполнено из высокопористого рифленого материала, покрытого токопроводящим слоем, оснащенным токоотводом. Полимерная основа конденсаторной структуры выполнена из углеродных волокон бусофита, металлизированных с поверхности пористым слоем титана толщиной 0,2-2 мкм, а токоотводы толщиной 5-20 мкм выполнены композитными: бусофит и титановый слой с покрытием из высокопроводного металла, преимущественно меди, серебра. Повышение удельной энергоемкости многослойной пленочной структуры конденсатора (не менее 40 Вт·час/кг), при снижении внутреннего омического сопротивления, является техническим результатом изобретения. 1 ил.
Изобретение относится к электротехнике, а более конкретно к слоистым пленочным накопителям электрической энергии - электролитическим конденсаторам, композиционные слои которых существенно отличаются по составу и физической структуре.
Уровень данной области техники характеризует описанный в патенте RU 2296055 С2, H01G 9/00; B82B 1/00, 2007 г. пленочный анод электролитического конденсатора из наноструктурированного композитного материала на основе высокомолекулярных соединений с использованием углерода.
Наноструктурированное токоведущее покрытие несущей углеродной основы пленочного анода выполнено из полиэтилентерефталата с высокоразвитой поверхностью, включающей рифления глубиной 10-30 нм и/или поры 0,2-6 мкм суммарным объемом 10-60%, при этом 1/5-1/3 часть пор выполнена сквозными.
Покрытие несущей основы связано непосредственно со слоем (5-50 нм) аморфного углерода sp-3 гибридизированного состояния атомов углерода и дополнительно имеет слой металла толщиной 25-250 нм, осаждаемого из паровой фазы в среде аргона, обеспечив максимальную адгезию с основой.
На токоведущее покрытие из алюминия или меди нанесен твердый электролит, формируя анод для компактных и электрически емких конденсаторов, в которых приложенная энергия запасается в тонком слое объемного заряда на границе электрод-электролит.
Электролитические конденсаторы, в которых используются аноды из полиэтилентерефталатной пленки с наноструктурированным композитным покрытием на модифицированной поверхности, характеризуются высокой удельной мощностью и стабильностью зарядно-разрядных характеристик в широком температурном интервале эксплуатации.
Недостатком описанного конденсатора является функциональная ненадежность из-за возможных отслоений автономных включений пористого вентильного металла по границам раздела, через которые во время эксплуатации проходят миграционные процессы взаимодиффузии, что приводит к нестабильности показателей назначения электролитического конденсатора и заметно снижает срок его службы.
Более совершенным пленочным конденсатором является описанный в патенте RU 2308112, H01G 9/04; B32B 15/04, 2007 г., который содержит размещенный на многослойной анодной пленке слой твердого электролита, адгезионно связанный с оксидным покрытием, имеющим включения вентильного металла.
Анодная пленка включает физически активированную токопроводящую подложку с развитой поверхностью и оксидное покрытие на конформном слое электрохимически активного алюминия, имеющего регулируемую объемную пористость, связанного с поверхностью подложки посредством гетероперехода, представляющего собой наноструктурированную композицию из материала подложки и напыленного вентильного металла.
Выполнение включений пористого алюминия в виде конформного слоя, подобного профилю подложки, в оксидном покрытии кратно увеличивает контактную поверхность взаимодействия с твердым электролитом пленочного конденсатора.
Оксидное покрытие в структуре пленочного конденсатора выполняет функции диэлектрика.
Под диэлектриком здесь следует понимать и двойной электрический слой, возникающий между двумя примыкающими средами - анодом и катодом в виде твердого электролита.
Вентильный металл в виде слоя покрытия обеспечил открытость высокопористой поверхности, доступной для заполнения электролитом, что позволяет использовать в конденсаторе твердый электролит, расширяя тем самым технологические возможности применения.
Наличие объемной пористости и создание ионной обработкой радиационных дефектов в слое вентильного металла приводит к повышению электрохимической активности материала, которая управляемо меняется за счет регулирования количества и размера пор в объеме напыляемого алюминия.
Сформированная таким образом пористая структура напыленного алюминиевого слоя более легко подвергается электрохимическому оксидированию, формируя слой диэлектрика, менее механически напряженного, что повышает функциональность конденсатора в целом.
При этом активность вентильного металла обеспечивает создание более толстого слоя качественного оксида для увеличения рабочего напряжения пленочного конденсатора повышенной емкости.
Этот пленочный конденсатор за счет улучшения механических характеристик, пластичности и адгезионной прочности монолитных соединений структурных составляющих имеет повышенную удельную емкость и напряжение функционирования более 600 B.
Однако дальнейший рост удельной емкости описанного пленочного конденсатора ограничен закономерностями электротехники.
Отмеченный недостаток исключен в пленочном конденсаторе усовершенствованной конструкции, выполняемой по штатной рулонной технологии действующего электродугового вакуумного оборудования, характеризующимся кратно повышенной удельной электрической емкостью, является описанный в патенте RU 2402830 C1, H01G 4/33; B82B 1/00, 2009 г., который по технической сущности и числу совпадающих признаков выбран наиболее близким аналогом предложенному
Известный пленочный конденсатор содержит многослойную анодную фольгу с высокоразвитой поверхностью, на которой адгезионно закреплена оболочка диэлектрика, покрытая твердым электролитом.
В слое диэлектрика толщиной 2-100 нм диспергированы кластеры металла размером 0,5-50 нм, при этом между анодной фольгой и слоем твердого диэлектрика размещено, как минимум, два слоя диэлектрика, разделенных прослойкой из кластеров металла.
Слой диэлектрика сформирован осаждением кластеров металла из гидрозоля посредством импульсных дуговых разрядов последовательно кластеров серебра и кластеров алюминия и/или титана, которые затем на поверхности оболочки окисляют, соответственно в количестве (мас.%): 1-30 и 70-99.
Структурно известный пленочный электрод включает полимерную основу с рифленой высокопористой поверхностью алмазоподобного нанослоя, на который через гетеропереходы последовательно нанесены слой токоведущего алюминия и губчатого вентильного металла, прослойки серебра, разделенные диэлектриком (окисью алюминия, полимером) и покрытие из твердого электролита.
Каждый слой диэлектрика формируется толщиной 2-100 нм для увеличения электрической емкости анодной фольги, функциональный слой алюминия которой осаждается из технологического гидрозоля в форме кластеров размером 0,5-50 нм.
Минимальный размер осаждаемых кластеров алюминия ограничен для практического формирования оболочки диэлектрика, в которой исключены касания примыкающих слоев (металлического анода и электролита).
В оболочке диэлектрика толщиной 100 нм гарантированно размещаются кластеры металла размером 50 нм, при этом увеличивать слой диэлектрика нецелесообразно, потому что электрические характеристики губчатого металла существенно не изменяются.
Нанесение кластеров металла на подложку осуществляют осаждением из технологического гидрозоля, поэтому кластеры металлов размером более 100 нм образуют седиментационно неустойчивую взвесь.
Кластеры металлов меньше 2 нм не обеспечивают сплошности формируемого слоя, причем их изготовление технологически затруднительно.
Разделение слоев в оболочке диэлектрика прослойками из кластеров металлов обеспечивает соответствующее повышение его диэлектрической проницаемости за счет увеличения поляризуемости и, как следствие, рост удельной электрической емкости многослойного пленочного конденсатора.
Выполнение конформного слоя диэлектрика на поверхности губчатого металла анодной пленки последовательным осаждением кластеров серебра (1-30 мас.%), а затем кластеров алюминия и/или титана (70-99 мас.%), которые с поверхности окисляют, отработано экспериментально и обусловлено следующим.
Нетоковедущий слой оксидов служит матрицей диэлектрика, в которой распределены кластеры металла.
Кластеры серебра служат барьером, формирующим четкую границу примыкающих различных по функциям материалов: губчатый металл - серебро - диэлектрик, который образуется окислением алюминия и титана, расположенных на поверхности оболочки диэлектрика.
Содержание серебра менее 1 мас.% заметно не увеличивает электротехнических характеристик диэлектрика, в частности диэлектрической проницаемости, и не образует барьерного слоя на границе раздела.
При увеличении массового содержания серебра в слое свыше 30 мас.% снижается пробивное напряжение, что ухудшает показатели назначения пленочного конденсатора.
Продолжением достоинств известного многослойного пленочного конденсатора являются присущие недостатки: технологическая сложность изготовления, при высокой потребительской стоимости из-за больших капитальных вложений в специальное оборудование, и ограничение роста электротехнических параметров конденсатора.
Технической задачей, на решение которой направлено настоящее изобретение, является кратное повышение показателей назначения технологичного пленочного конденсатора, пригодного для серийного изготовления.
Требуемый технический результат достигается тем, что в известном пленочном конденсаторе, содержащем разделенные диэлектриком пакетные электроды, полимерное основание которых выполнено из высокопористого рифленого материала, покрытого токопроводящим слоем, оснащенным токоотводом, согласно изобретению, полимерная основа выполнена из углеродных волокон бусофита, металлизированных с поверхности пористым слоем титана толщиной 0,2-2 мкм, а токоотводы толщиной 5-20 мкм выполнены композитными: бусофит и титановый слой с покрытием из высокопроводного металла, преимущественно меди, серебра.
Отличительные признаки предложенного технического решения кратно повысили удельную энергоемкость конденсаторной структуры (не менее 40 Вт·час/кг), при снижении внутреннего омического сопротивления.
Металлизация поверхности углеродных волокон основы конденсаторной пакетной структуры, состоящей из нескольких слоев, обеспечила кратное увеличение удельной энергоемкости (Вт·час/кг), при снижении внутреннего сопротивления (Ом).
Выполнение полимерной основы пленочного конденсатора из углеродных волокон бусофита 40 обеспечивает высокую удельную энергоемкость электролитической ячейки (более 10 Вт·час/кг) и технологичность ее изготовления.
Металлизация волокон бусофита с поверхности пористым слоем титана направлена на снижение внутреннего электрического сопротивления конденсатора для максимальной отдачи электрической энергии в нагрузку.
Пористый слой титана на внутренней поверхности волоконной структуры конденсаторного пакета необходим, чтобы электролит, который пропитывает высокопористый бусофит, обеспечивал электрический контакт между примыкающими слоями титанового покрытия и с каждым волокном бусофита. Титан выбран как металл, который химически не взаимодействует с электролитом.
Толщина титанового покрытия на поверхности углеродных волокон основы определялась опытным путем для достижения максимальных значений показателей назначения, согласно расчетам по математической модели планирования эксперимента, результаты которых получили подтверждение в оптимизированном диапазоне значений толщины адгезионного токопроводящего слоя.
Если использовать слой покрытия волокон бусофита пористым титаном толщиной менее 0,2 мкм, то не удается получить устойчивое минимальное электрическое сопротивление на контакте между двумя сопряженными друг с другом слоями бусофита.
Если слой пористого титана в покрытии будет больше 2 мкм, то сопротивление контакта двух сопряженных слоев бусофита перестает зависеть от толщины слоя пористого титана и дальнейшее увеличение его толщины становится экономически и технически нецелесообразным.
Выбор толщины токоотводов в диапазоне 5-20 мкм определен в соответствии с достигаемой токовой нагрузкой при минимальном времени разряда конденсаторной ячейки.
Токоотводы выбранной толщины обеспечивают прохождение максимального тока через него при температуре эксплуатации 50°C.
Выполнение токоотводов композитными, в форме последовательных высокопористых слоев бусофита, титана и меди/серебра, создает минимальное электрическое сопротивление на контакте бусофит-металл, сравнительно с накладными токоотводами, и обеспечивает увеличение в полтора-два раза удельной емкости электролитической ячейки.
Примыкающий толстый слой пористого титана на поверхности бусофита обеспечивает хороший электрический контакт с углеродным материалом основы.
Предложенная конструкция токосъемника обеспечивает отсутствие паразитных электрических емкостей, которые неизбежно появляются при использовании прижимных токосъемных устройств, снижая тем самым общее сопротивление электролитической ячейки и ее массогабаритные характеристики.
Следовательно, каждый существенный признак необходим, а их совокупность в устойчивой взаимосвязи являются достаточными для достижения новизны качества, неприсущей признакам в разобщенности, то есть поставленная в изобретении техническая задача решена не суммой эффектов, а новым сверхэффектом суммы признаков.
Сущность предложенного технического решения поясняется чертежом, который служит чисто иллюстративным целям и не ограничивает объема притязаний совокупности существенных признаков формулы.
На чертеже изображена структурная схема предложенного конденсатора.
Каждый пакетный электрод 1 включает несколько слоев 2 углеродного волокна - бусофита 40, с поверхности покрытого прослойками 3 высокопористого титана толщиной 0,2-2 мкм.
Электроды 1 изолированы между собой диэлектриком 4, выполненным, например, из конденсаторной бумаги или полимерной мембраны.
На внешней прослойке 3 титана каждого электрода 1 ионно-дуговым осаждением сформирован толстый (суммарно 5-20 мкм) слой 5 меди или серебра, служащий токоотводом 6.
Сравнение предложенного технического решения с выявленными аналогами уровня техники не выявило идентичного совпадения совокупности существенных признаков изобретения.
Существенные отличия пленочного конденсатора не являются очевидными для специалистов по электротехнике, которые прямо не следуют из постановки технической задачи.
Изготовление многослойных пленочных конденсаторов предложенной структуры в устойчивой взаимосвязи составляющих элементов возможно осуществлять на действующем автоматическом производстве серийно для использования в качестве промышленных источников тока.
Из вышесказанного можно сделать вывод о соответствии изобретения условиям патентоспособности.
Пленочный конденсатор, содержащий разделенные диэлектриком пакетные электроды, полимерное основание которых выполнено из высокопористого рифленого материала, покрытого токопроводящим слоем, оснащенным токоотводом, отличающийся тем, что полимерная основа выполнена из углеродных волокон бусофита, металлизированных с поверхности пористым слоем титана толщиной 0,2-2 мкм, а токоотводы толщиной 5-20 мкм выполнены композитными: бусофит и титановый слой с покрытием из высокопроводного металла, преимущественно меди, серебра.
www.findpatent.ru
Пленочные конденсаторы, изготовленные металлизацией диэлектрика
Из-за технологических трудностей, связанных с одновременным сворачиванием в цилиндр нескольких слоев, образованных металлической фольгой и диэлектрической пленкой, большая часть конденсаторов изготавливается методом напыления алюминиевого слоя толщиной до 12 мкм на одну из сторон диэлектрической пленки для образования обкладки конденсатора. Следует отметить, что этот прием не только облегчает технологию производства конденсаторов, по также позволяет получить более высокие значения удельной, относительно занимаемого объема, емкости, так как пленка со слоем металлизации значительно тоньше фольги, однако, такие конденсаторы характеризуются более высоким значением последовательного эквивалентного сопротивления, ESR. Так как последовательное эквивалентное сопротивление для пленочных металлизированных конденсаторов становится значительным только на высоких частотах, когда оно становится сравнимым с емкостным (реактивным) сопротивлением конденсатора, этот фактор не вызывает серьезных осложнений. Однако фольговые конденсаторы часто рекомендуются их производителями, как более подходящие для использования в высокочастотных импульсных цепях, именно по этой причине.
Уже упоминалось, что из-за гранулированной структуры напыляемой металлической пленки, которая применяется при изготовлении пленочных резисторов и вызвана наличием небольшого количества посторонних примесей, в них возникают избыточные шумы, в силу чего пленочные резисторы характеризуются всегда несколько более высоким уровнем шумов по сравнению с проволочными. Так как обкладки в металлизированных пленочных конденсаторах также получают методами вакуумного напыления, то не будет очень самонадеянным предположить, что конденсаторы будут страдать от точно такой же проблемы, связанной с качеством металлической пленки, с тем лишь только отличием, что конденсаторы не подвергались планомерной проверке относительно уровня генерируемых шумов. Хотя чисто субъективные ощущения позволяют сделать вывод, что при использовании фольговых конденсаторов качество звучания радиоаппаратуры было лучше и, возможно, что причина этого явления заключается в технологических проблемах изготовления конденсаторов.
Металлизированные бумажные конденсаторы
Металлизированная бумага являлась традиционным диэлектриком в конденсаторах, которые использовались в классических ламповых усилителях, и в зависимости от бумаги и ее способности к пропитке качество изделий менялось от весьма посредственных до хороших. К сожалению, если герметизация металлизированных бумажных конденсаторов оказывается несколько худшей, чем идеальная, атмосферная влага проникает внутрь конденсатора, приводя к высоким токам утечки. Автору как-то довелось приобрести стереофонический усилитель мощности Leak Stereo 20, в котором использовались бумажные конденсаторы связи, и все они, как было потом установлено, оказались с большими токами утечки.
Использование для пропитки бумаги (минерального) масла или эпоксидных смол значительно улучшает положение, до такой степени, что изготовленный конденсатор имеет почти такие же хорошие характеристики, что и полипропиленовый конденсатор. Так как бумажные конденсаторы обладают свойством «самозалечивания», они широко используются в энергетике. При возникновении пиков перенапряжения бумажная изоляция пробивается в самом слабом месте, а напыленная металлическая пленка при этом испаряется, предотвращая, таким образом, возникновение короткого замыкания и вызванных им серьезных последствий.
Слюдяные посеребренные конденсаторы
Слюдяные посеребренные конденсаторы, имеющие небольшие значения емкости, традиционно использовались в ВЧ цепях, а также фильтрах звукового частотного диапазона, где необходима особенно высокая стабильность характеристик. Слюда представляет кристаллический материал, который легко расщепляется на отдельные чрезвычайно тонкие слои, на которые потом наносятся пленка из серебра. Сборка таких листов в пакеты обеспечивает очень низкое значение индуктивности конденсатора.
Так как слюда является природным материалом, она подвержена все капризам, свойственным неоднородным материалам. Существует несколько различных по свойствам типов слюды, но слюда мусковит обеспечивает изготовление конденсаторов с наименьшими потерями. Хотя мусковитная слюда и полистирол характеризуются сравнимыми по значению потерями (0,001 < tgδ < 0,0002), диэлектрические потери в слюде примерно в 80 раз выше по сравнению с полистиролом, поэтому использование полистирола в качестве диэлектрика является, как правило, предпочтительнее.
Из-за более высокой стоимости и большего разброса в параметрах посеребренные слюдяные конденсаторы сегодня практически повсеместно заменены на полистироловые, которые, в свою очередь, постепенно заменяются на полипропиленовые.
Керамические конденсаторы
Керамические конденсаторы предназначаются в первую очередь для радиочастотных узлов радиоприемников и радиопередатчиков. В аналоговых цепях звуковых трактов они обычно не используются!
До настоящего времени рассматриваемые диэлектрики характеризовались значением относительной диэлектрической проницаемости εr < 10, однако для конденсаторов с керамическим диэлектриком значение εr, может достигать 200 000! Как правило, для изготовления керамических конденсаторов используется титанат бария, или титанат стронция, которые являются пьезоэлектрическими материалами. Это означает, что они способны генерировать электрическое напряжение при приложении к ним механических воздействий (в частности, эти материалы являлись основой для керамических картриджей, которые использовались для воспроизведения пластинок в «музыкальных центрах» весьма посредственного качества).
Керамические конденсаторы могут использования в качестве высокочастотных блокировочных конденсаторов в цифровых цепях или цепях подогревателей, в которых их нестабильность величины емкости и низкое значение tgδ не вызывает возникновение существенных проблем.
next-sound.ru
Пленочный конденсатор
Изобретение относится к электронной технике и может быть использовано при производстве тонкопленочных гибридных и монолитных интегральных схем при изготовлении тонкопленочных конденсаторов. Техническим результатом изобретения является повышение выхода годных конденсаторов за счет снижения влияния дефектов диэлектрической пленки. Согласно изобретению пленочный конденсатор содержит первую и вторую обкладки, выполненные в виде металлических пленок, расположенный между обкладками диэлектрик, токовыводы, выполненные в виде части металлических пленок, выступающих над торцевыми сторонами диэлектрика, введены второй слой диэлектрика и расположенная между слоями диэлектрика промежуточная металлическая обкладка, состоящая из изолированных фрагментов. 2 ил.
Изобретение относится к электронной технике и может быть использовано при производстве тонкопленочных гибридных и монолитных интегральных схем при изготовлении тонкопленочных конденсаторов.
Известен конденсатор с пленочным диэлектриком (патент №1452383, H01G 4/22, опубл. 1995.02.20), содержащий обкладки и расположенный между ними пропитанный пленочный диэлектрик, выполненный из слоев полимерной пленки с шероховатой и гладкой поверхностями, при этом слой полимерной пленки с гладкой поверхностью расположен между двумя слоями пленки, имеющими с обеих сторон шероховатую поверхность.
Наиболее близким техническим решением является пленочный конденсатор (патент №2046429, H01G 4/06, опубл. 1995.10.20), содержащий первую и вторую обкладки, выполненные в виде металлических пленок, включающих слои Cr-Cu, расположенный между обкладками диэлектрик в виде полиимидной пленки и размещенные на противоположных сторонах диэлектрика токовыводы, при этом соотношение толщин металлических пленок и пленки полиимида выбрано в диапазоне от 1,1 до 1,2, а токовыводы выполнены в виде части металлических пленок, выступающих над торцевыми противоположными сторонами полиимидной пленки соответственно.
Недостатком известных технических решений является невысокий процент выхода годных изделий из-за пробоя конденсатора в случае наличия дефектов в тонких пленках диэлектрика. Вероятность появления дефекта увеличивается в случае создания конденсаторов большой емкости вследствие увеличения площади конденсатора.
Задачей изобретения является повышение выхода годных конденсаторов за счет снижения влияния дефектов диэлектрической пленки.
Для решения поставленной задачи в пленочный конденсатор, содержащий первую и вторую обкладки, выполненные в виде металлических пленок, расположенный между обкладками диэлектрик, токовыводы, выполненные в виде части металлических пленок, выступающих над торцевыми сторонами диэлектрика, введены второй слой диэлектрика и расположенная между слоями диэлектрика промежуточная металлическая обкладка, состоящая из изолированных фрагментов.
Техническим результатом изобретения является создание пленочного конденсатора, электрическая схема которого представляет собой n параллельно соединенных между собой пар последовательно включенных конденсаторов малой емкости. Параллельное соединение последовательно соединенных пар конденсаторов обеспечивается наличием в структуре пленочного конденсатора общих для всех пар нижней и верхней обкладок конденсатора. Каждая пара последовательно соединенных конденсаторов малой емкости образована верхней обкладкой и одним из фрагментов промежуточной обкладки и этим же фрагментом и нижней обкладкой конденсатора.
Дефект в пленке диэлектрика приводит к пробою одного из конденсаторов малой емкости, в пределах которого он локализован. Промежуточная обкладка не позволяет пробою развиться дальше, таким образом, работоспособность конденсатора в целом сохраняется.
Таким образом, повышается процент выхода годных конденсаторов, поскольку в заявленном устройстве диэлектрик получается двухслойным, дефекты в слоях распределены случайным образом и вероятность пробоя одновременно двух последовательно включенных конденсаторов невелика, а в случае пробоя одного из конденсаторов малой емкости выходит не весь конденсатор, а только его составная часть.
Заявляемое устройство пленочного конденсатора отвечает всем критериям патентоспособности изобретения.
Оно ново, т.к. аналогичные известные из уровня техники решения не обладают тождественной совокупностью признаков.
Заявляемое устройство соответствует критерию «изобретательский уровень», т.к. сущность этого решения для специалиста явным образом не следует из уровня техники и не выявлена совокупность признаков, совпадающих с отличительными признаками заявляемого изобретения.
Заявляемое изобретение является промышленно применимым, поскольку оно может быть использовано в производстве гибридных и монолитных интегральных микросхем в условиях промышленного предприятия.
На фиг.1 представлена конструкция предлагаемого пленочного конденсатора, на фиг.2 приведена электрическая схема конденсатора без пробоя и в случае пробоя конденсатора малой емкости.
Пленочный конденсатор содержит обкладки 1 и 2 пленочной металлизации, первый слой 3 диэлектрика, промежуточную металлическую обкладку, состоящую из изолированных друг от друга фрагментов 4, второй слой 5 диэлектрика и токовыводы 6 и 7, являющиеся продолжением обкладок 1 и 2 конденсатора, выступающие над торцевыми сторонами диэлектрика. Число фрагментов 4 должно быть, по меньшей мере, равно 2.
Формирование структуры начинается с очистки подложки и напыления на ее поверхность металла (V-Mo) толщиной 0,1 мкм - нижняя обкладка 1 и токовывод 6. Затем на всю поверхность нижней обкладки 1 осаждается первый слой диэлектрика (SiO2) 3 толщиной 0,2 мкм.
Промежуточная обкладка 4 формируется напылением металла (V-Mo) толщиной 0,1 мкм на первый слой диэлектрика 3, с помощью фотолитографии и травления формируется промежуточная обкладка конденсатора 4. Промежуточная обкладка конденсатора представляет собой несколько металлических фрагментов, изолированных друг от друга, имеющих произвольную конфигурацию, а их количество зависит от площади изготавливаемого конденсатора.
Второй слой диэлектрика 5 создается путем осаждения на полученную структуру пленки SiО2 толщиной 0,2 мкм. Верхняя обкладка конденсатора 2 создается напылением металла (V-Mo) толщиной 0,1 мкм на второй слой диэлектрика 5. С помощью фотолитографии и травления формируется верхняя обкладка конденсатора 2 и токовывод 7.
Конечным этапом изготовления конденсатора является формирование контакта к токовыводу нижней обкладки конденсатора. Для этого выполняется фотолитография и травление диэлектрика до металла токовывода 6.
Заявляемое решение позволяет повысить выход годных конденсаторов, поскольку использование его существенно понижает требования к дефектности диэлектрической пленки.
Пленочный конденсатор, содержащий первую и вторую обкладки, выполненные в виде металлических пленок, расположенный между обкладками диэлектрик, токовыводы, выполненные в виде части металлических пленок, выступающих над торцевыми сторонами диэлектрика, отличающийся тем, что введены второй слой диэлектрика и расположенная между слоями диэлектрика промежуточная металлическая обкладка, состоящая из изолированных фрагментов.
www.findpatent.ru