Вакуумная формовка. Оборудование для вакуумной формовки пластиков и пленок. Пленка для вакуумной формовки
Вакуумная формовка. Оборудование для вакуумной формовки пластиков и пленок
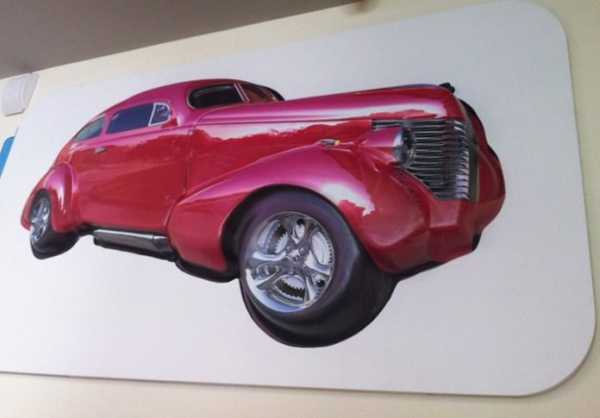
Навигация:
- Вакуумная формовка пластиков
- Вакуумно-пленочная формовка
- Формы для вакуумной формовки
- Метод вакуумной формовки
- Станок для вакуумной формовки пластика
Вакуумная формовка является технологией формирования изделий при помощи горячего вакуума. Такой вид производства осуществляется при помощи пластичных материалов, которые под воздействием горячего вакуума или низкого давления способны менять свою форму. Такой способ изготовления изделий в большинстве случаев применяется в серийном производстве пластиковых изделий крупных размеров, но не исключено применение при единичных изготовлениях пластмассовых форм.
Вариант вакуумной формовки
Основные привилегии использования метода вакуумной формовки:
- Имеется возможность использовать пластик, толщина которого в зависимости от характеристик нужного изделия составляет од 0, 04 до 7 мм, а что касаемо конечных габаритов изделия, то они могут достигать 5 м в диаметре;
- Готовое изделие от матрицы можно отделять вручную;
- Низкая цена заготовки;
- Относительно маленькая цена на обустройство системы вакуумной формовки.
Для формирования готового изделия применяется достаточно обширный ряд материалов: пластик, прозрачный либо цветной акрил, полистирол, ПВХ, поликарбонат и так далее. Негативным фактором при изготовлении таких изделий является то, что осуществить создание заготовки, один из углов которой будет меньше 90 градусов невозможно.
Вакуумная формовка пластиков
На сегодняшний день формы из пластика могут полноценно заменять аналогичные изделия, которые ранее лидировали в индустриальном производстве. Применяется такой вид формовки для серийного производства и для индивидуальных экземпляров изделий. Благодаря современным агрегатам для вакуумной формовки, дизайн изделия может иметь очень креативные формы, что удовлетворяет огромный диапазон сфер производства. К разряду пластика относятся следующие материалы:
- Оргстекло. Этот материал является полиметилметакрилатным пластиком либо акрилом, и в своей стандартной форме он полностью прозрачный, но при необходимости его цвет можно изменить при помощи добавления красителей любых оттенков. Прежде чем использовать такой вид материала, его необходимо тщательно высушить, так как он предрасположен к интенсивному впитыванию влаги из окружающей среды. Из недостатков использования данного сырья, можно отметить, что в процессе формирования необходимого изделия, затрачивается большое количество электричества, но это с лихвой компенсируется долговечностью готового продукта, который применяется в рекламных стендах, в изготовлении объемных цифр и букв, и прочих деталей продукции для рекламных кампаний.
- Пластик ABS. Этот материал свободно поддаётся вакуумной формовке и отличается изумительными качествами выдерживания ударных нагрузок. Благодаря этому, основное предназначение при использовании данного материала является изготовление спортивного инвентаря. В дополнение можно подчеркнуть, что ABS пластик способен выдерживать нагрев до 90 градусов в процессе его формовки.
Вакуумная формовка пластиков
Вакуумно-пленочная формовка
Одним из разновидностей формовочного материала является плёнка ПЭТ, которая очень просто и технологически удобна в процессе вакуумной формовки. Такой материал не требует заблаговременной просушки, обладает низким внутренним напряжением, имеет пониженную теплоемкость, что многократно экономит затраты на использование электроэнергии в процессе формовки деталей из вакуумной пленки. Таким образом, характеристики изготовленных элементов способствуют широкому применению в рекламной и осветительной сфере.
Вакуумно-пленочная формовка
Формы для вакуумной формовки
Существует два типа материала для создания форм, которые используются в процессе вакуумной формовки:
- Формы из МДФ
Наиболее простым, недорогим и быстрым вариантом для изготовления форм, является фрезеровка МДФ плит при помощи ЧПУ. С таких плит набирается нужная толщина и в соответствии с 3D моделью, которая запрограммирована в ЧПУ, выполняется фрезеровка необходимой формы. После окончательной фрезеровки детали, её высушивают и обрабатывают специальным раствором, и в заключение поверхность обрабатывается шлифовочным материалом, после чего, её уже можно использовать для вакуумной формовки. В зависимости от сложности формы матрицы или иными словами болванки, разница количества циклов отличается при использовании. Таким образом, если форма имеет округлые края и невысокие выступы, то количество использования может достигать до 500 раз. Но если конструкция состоит из острых углов и высоких выступов, то её стойкость значительно сокращается, появится необходимость в реставрации болванки. Но реставрация в большинстве случаев является довольно дешевым процессом, за счет низкой цены на материалы для повторного изготовления.
- Формы из стеклопластика
Такой материал можно использовать большее количество раз, нежели МДФ. Технология производства такой матрицы состоит в том, что предварительно необходимо иметь полую заготовку, в которую заливается полимерная смола, армированная стеклотканью. Данная процедура занимает значительный отрезок времени, но с лихвой окупается за счёт многократного использования формы в дальнейшем. В дополнение, если необходимо за один цикл изготовить, к примеру, 10 одинаковых изделий при помощи вакуумной формировки, то использование стеклопластика гораздо удешевляет размножение болванок в отличие от МДФ форм.
Метод вакуумной формовки
Чтобы создать изделия при помощи вакуумной формовки, в первую очередь необходимо приобрести соответствующий вакуум-формовочный станок. Касательно материалов, которые необходимы для создания изделий, то их тип зависит от сферы деятельности предприятия и дальнейшей области применения готовых изделий. Главным требованием, которое предъявляется сырью для производства, это одинаковая толщина всех листов для единой серии деталей.
Процедуру формовки при помощи вакуума можно разделить на 2 ступени:
- Изготовление болванки;
- Вакуумное формирование по матрице из подобранного материала.
Касательно изготовления матрицы нужно отметить, что этот процесс отнимает довольно мало средств, так как основным материалом для изготовления болванок является МДФ или стеклопластик. Существуют и другие типы материалов, такие как дюраль алюминий, всевозможные смолы и так далее, но их применение целесообразно только на производствах, где изготовления формовочных изделий основана на постоянном серийном цикле.
Сама формовка начинается с того, что к матричной рамке станка крепится сырьевой лист, который кстати необходимо тщательно очистить от всякого рода пыли и загрязнений, так как в противном случае эти компоненты станут единым целым с готовым изделием. В середине расположен элемент матрицы либо серия болванок, при множественном изготовлении за один цикл. Для вакуумного формирования над рамкой с материалом находится разогретая панель, которую необходимо опустить на формируемый лист, чтобы установленный материал разогрелся до нужной температуры и принял форму матрицы.
Станок для вакуумной формовки пластика
Предлагаемая к независимому производству установка станка предполагает из себя конструкцию с недвижимой матрицей с прикрепленной модификацией, к которой перемещается рамочка, в которую прижимается сырье с целью формовки, в верхней части конструкции находится нагреватель. Вакуум формируется вакуумнасосом, что и формирует разряжение. В последствии нагрева пластмассы, вводится вакуум и совершается непосредственно само изготовление. Как только лишь сырье получил установленную фигуру, вакуум выключается и допускается доставать лист с отделанной фигурой. За один раз допускается формовать с 1-го вплоть до нескольких 10-ов продуктов – всё зависит от масштабов рабочего стола станка и объемов модификации. Остаётся прибавить, что средний период цикла формовки забирает от 40 вплоть до 120 сек. – всё находится в зависимости от толщины материала и сложности самого продукта.
Станок для вакуумной формовки пластика
pv-system.ru
Вакуумная формовка пластика, особенности технологии
Вакуумной формовкой называется процесс производства серийных или единичных изделий из листовых полимерных материалов путем придания им формы матрицы под воздействием температуры и вакуума. В процессе производства изделия лист пластика нагревается до температуры размягчения и плотно облегает поверхность матрицы за счет создания отрицательного давления.
В серийном промышленном производстве для вакуумного формования изделий применяется современное высокотехнологичное оборудование, осуществляющее процессы разогрева сырья и откачки воздуха в режиме постоянно действующего конвейера.
В качестве сырьевых заготовок могут использоваться практически все полимеры, обладающие свойствами термопластов (полипропилен, полиэтилен, поливинилхлорид, поликарбонат и другие).
Методом вакуумной формовки выпускаются пластиковые изделия для всех направлений и сфер деятельности, в том числе:
- для авиационной, автомобильной и судостроительной отраслей промышленности;
- для производства упаковочной тары и емкостей всех видов;
- для нужд пищевого производства, химической промышленности, медицины;
- для производства бытовой техники, приборов и оборудования;
- для нужд строительства и дизайна.
Технология производства
Особенностью метода вакуумной формовки является возможность протекания производственного процесса с невысоким отрицательным давлением. Такие процессы не требуют наличия мощного оборудования, высокопрочных матричных форм и значительных расходов энергоносителей. Вследствие этого производство считается экономным, а готовые изделия имеют низкую себестоимость.
Широкие возможности для применения автоматизированных производственных процессов позволяют наладить непрерывный цикл изготовления продукции самого различного назначения. Немаловажную роль играет и то, что для формовки используются готовые листовые материалы, не требующие глубокой переработки сырья.
Стандартный метод вакуумной формовки состоит из нескольких этапов, включающих в себя:
- фиксацию заготовки на матрице;
- нагрев полимерного листа;
- предварительное растяжение листа;
- откачку воздуха из матрицы и вдавливание заготовки;
- охлаждение материала;
- извлечение изделия из матрицы;
- окончательную доработку изделия.
Для того чтобы понять, что представляет собой вакуумная формовка пластика, необходимо подробно рассмотреть все стадии производственного процесса.
Фиксация заготовки
Листы полимера крепятся к матрице при помощи зажимной рамы. Фиксирующие элементы должны обеспечивать прижимное усилие, достаточное для удержания листов толщиною до 6 мм. При автоматизированной подаче заготовок на формовку работа подвижных элементов прижимной рамы должна исключать возможность повреждения готового изделия.
Нагрев заготовки
Главной особенностью этого этапа работ является обеспечение равномерного прогрева всего объема заготовки, так как в противном случае плотного прилегания материала к форме матрицы добиться не удастся. В технологии вакуумной формовки для нагрева заготовок применяются, как правило, инфракрасные излучатели и кварцевые лампы.
Общая площадь поверхности заготовки делится на несколько зон, каждая из которых нагревается отдельным элементом, а температура нагрева контролируется при помощи специальных пирометров. Данные о температуре обрабатываются компьютерной системой для своевременной корректировки разницы нагрева различных участков заготовки.
Предварительное растяжение листа
В некоторых случаях в процесс производства включают предварительное растяжение материала, называемое также раздувом. Растяжение выполняется после достижения пластиком рабочей температуры формовки и служит для выравнивания толщины заготовки. Процесс раздува необходим при формовании заготовок на глубоких матрицах со сложной геометрией поверхности.
Откачка воздуха и вдавливание заготовки
После предварительного нагрева и растяжения закрепленной заготовки из аппарата для формовки производится откачка воздуха вакуумным насосом. При снижении давления внутри аппарата полимерный материал, достигший состояния пластичности, начинает облегать форму матрицы.
В зависимости от требований, предъявляемых к конечному продукту, технология вакуумной формовки, может совмещаться с технологией штампования при помощи пуансона. В этом случае помимо откачки воздуха на заготовку сверху воздействует специальная конструкция, профиль которой повторяет поверхность матрицы.
Комбинацией этих методов можно добиться максимальной точности заданных форм деталей, а также обеспечить равномерное распределение полимерного материала по поверхности матрицы, полностью исключив образование складок и участков с различной толщиной.
Охлаждение изделия и извлечение из матрицы
Во избежание повреждения детали при извлечении из матрицы необходимо дождаться полного остывания материала. Если применяемое для процесса вакуумная формовка пластика оборудование оснащено системами воздушного охлаждения, время остывания изделий может быть сокращено на 20-30%.
Для изготовления наиболее ответственных деталей вакуумные матрицы оснащаются системами управления температурными процессами.
Наличие таких систем позволяет добиваться равномерного охлаждения изделия, что способствует повышению его эксплуатационных качеств. Извлечение остывшей детали из матрицы происходит под воздействием создаваемого внутри давления.
Окончательная обработка
Изделие, извлеченное из матрицы необходимо отделить по контуру от излишков полимерного материала. Сформованная деталь может являться полуфабрикатом для дальнейшего сборочного производства. Для этого изделие может разрезаться, в нем могут высверливаться отверстия для крепежных элементов и делаться пропилы для вставок.
Для окончательной обработки материала могут использоваться:
- механический обрезной пресс;
- ленточная пила вертикального или горизонтального типа;
- станок строгально-шлифовальный;
- фрезерный станок;
- сверлильный станок;
- ручной механический и электроинструмент.
polimerinfo.com
Вакуумная формовка. Сферы и особенности применения
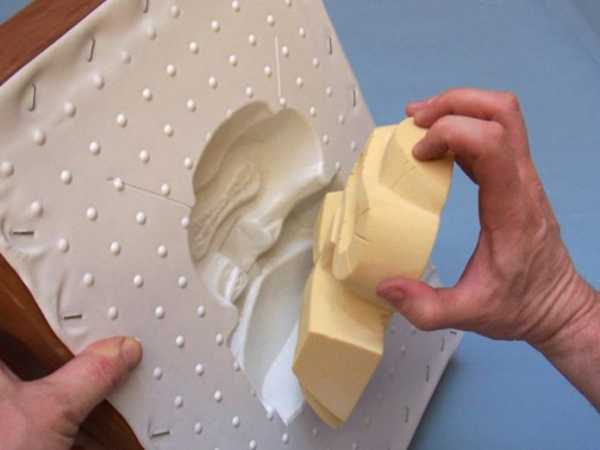
Навигация:
- Метод вакуумной формовки и особенности применения
- Вакуумная формовка пластиков. Области применения
- Вакуумно-пленочная формовка. Особенности применения
Вакуумной формовкой изготавливают изделия из пластиков, которые можно встретить повсюду. Вакуумно-пленочной формовкой изготавливают литейные формы, и она известна только специалистам литейного производства. Вакуумной формовкой получают:
- Торговое оборудование и оснастку для магазинов
- Продукцию рекламного характера и различные сувениры
- Объемные буквы и другие средства наружной рекламы магазинов и заведений
- Формы и оснастку для изготовления строительных элементов, дорожного ограждения и дорожных знаков
- Объемные контейнеры и блоки для упаковки пищевых продуктов
- Элементы украшения в сфере автомобильного тюнинга
- Емкости для упаковки различных товаров
- Емкости для оснащения зооуголков для растений и животных
- Контейнеры для вакуумной упаковки товаров
- Детские игрушки, товары для детей
Метод вакуумной формовки и особенности применения
В вакуумной формовке используют атмосферное давление воздуха для получения изделия необходимой формы. Главная особенность метода — создание равномерного газостатического давления величиной в 1 атмосферу на всей поверхности заготовки. Отметим универсальность метода. Вакуум является рабочим инструментом, деформирующим изделие при вакуумной формовке. В технологии вакуумно-пленочного формования вакуума формирует поверхность литейной формы из песка для последующей заливки расплавленного металла. В этом случае вакуум выполняет вспомогательную функцию.
Вакуумная формовка пластиков. Области применения
Вакуумным формованием получают детали пространственной формы из листовых термопластов. Разогретая листовая заготовка копирует форму полости в твердой матрице. При этом не требуется пуансон, что упрощает процесс изготовления формы и снижает издержки при производстве изделий. Эту технологию преимущественно применяют для масштабного производства объемных изделий. Иногда экономически целесообразно изготовление единичных изделий сложной формы или больших размеров.
Технологический процесс изготовления изделий из пластика методом вакуумной формовки включает несколько этапов. На первом этапе листовую заготовку нагревают в специальной камере и доводят до вязко-пластичного состояния. Затем разогретый материал помещают на матрицу и прижимают по контуру специальным прижимом. На следующем этапе воздух откачивают из под заготовки и создают вакуум. Атмосферное давление плотно прижимает заготовку к поверхности матрицы до полного затвердевания. Для получения высокого качества изделия полость матрицы должна быть полированной и иметь плавные сопряжения различных поверхностей. На следующем этапе готовое изделие выталкивают из полости матрицы, создавая давление воздуха. Следует отметить, что вместо отсоса воздуха иногда создают избыточное давление для заполнения пластиком полости матрицы. Такой технологический процесс называют пневматическим формованием.
Станок для вакуумной формовки пластика. Описание конструкции и технических характеристик некоторых моделей
Станки для вакуумной формовки просты по конструкции. Их разрабатывают и производят как специализированные фирмы, например, «ATSNGroup» «Flexplast», «Фолипласт», так и различные частные предприятия. В сети интернет-магазинов можно приобрести готовое оборудование и оснастку, а также заказать станок по спецзаказу.
Станок для формовки пластиков представляет собой бак определенных размеров. В комплекс входят рабочие органы и агрегат для создания вакуума, органы управления и энергообеспечения.
Размеры станков определяются габаритами получаемого изделия из листового термопласта. Компания «ATSNGroup» выпускает линейку станков с возможностью изготовления изделий в диапазоне от 400 х 400 до 5000 х 5000. Базовые модели ориентированы на размеры 600 х 600, 1000 х 100 и 2400 х 1400 мм с возможностью быстрой переналадки в сторону уменьшения размеров при необходимости выпуска соответствующей продукции. Станки оборудованы кварцевыми нагревателями мощностью 8; 19,5; 55 кВт и насосами производительностью 200, 750, 1000 литров/мин., соответственно типоразмерам моделей. Эти устройства обеспечивают быстрый нагрев заготовки и создание вакуума. Предусмотрена возможность локального разогрева. Станок с размерами стола 2400 х 1400 мм оборудован системой для предварительного выдува листа заготовки с последующим формованием готового изделия с требуемой точностью. Это позволяет существенно повысить производительность работы оборудования при изготовлении изделий больших размеров. Установки позволяют получать изделия из ПВХ, полистирола, полипропилена, полиэтилена и т.п.
Формы для вакуумной формовки. Материалы и особенности изготовления
Формы изготавливают из алюминия, эпоксидной смолы, МДФ, стеклопластика. На выбор материала влияют: масштабность производства, размеры изделия, температурный режим подготовки заготовки к процессу формования.
Формы из алюминиевых сплавов изготавливают литьем, а затем добиваются требуемой точности и качества с помощью фрезерования, шлифования и полирования. Формы из эпоксидной смолы получают путем заливки компаунда в мастер-форму, изготовленную по методу обратного копирования. Формы из МДФ и стеклопластика изготавливают горячим или теплым прессованием. В связи с различием физико-механических и химических свойств материалов, формы имеют различные эксплуатационные показатели. Главные из них: жесткость, химическая стойкость, долговечность и ремонтопригодность.
Вакуумно-пленочная формовка. Особенности применения
Технология вакуумно-пленочной формовки или V – процесс, относится к сфере литейного производства и имеет мало общего с вакуумной формовкой, применяемой в производстве изделий из листового пластика. Объединяет эти два направления только использование вакуума для создания атмосферного давления. При вакуумной формовке, вакуум является рабочим инструментом, обеспечивающим основной технологический процесс изготовления детали, т.е. воздействует непосредственно на поверхность изделия. В технологии вакуумно-пленочного формования вакуум воздействует на поверхность песка, подготавливая литейную форму к заливке расплавленным металлом. В этом случае вакуум исполняет вспомогательную роль в производстве отливки, т.е. непосредственно на поверхность изделия – отливки не действует.
В технологии вакуумно-пленочной формовки (ВПФ) используется тонкая синтетическая пленка и тонкодисперсный кварцевый песок без примеси глины. Поверхность литейной формы накрывают пленкой, разогревают и откачивают воздух через микроскопические отверстия в подмодельной плите. Затем заполняют опоку кварцевым песком и накрывают следующим слоем пленки. Откачивая воздух из промежутка между слоями пленки, создают твердый песчаный каркас, повторяющий форму модели. Откачка воздуха и поддержание вакуума продолжается в процессе заливки металла в форму вплоть до затвердевания готового изделия. В процессе заливки металла пленка газифицируется и газ проникает в песок, выполняя роль связующего.
Технология ВПФ создана в Японии и уже более 50 лет применяется в СССР и в странах постсоветского пространства, в том числе, в России для получения сложных отливок для различных сфер применения. Благодаря этой технологии удается значительно повысить точность и качество отливок и отказаться в ряде случаев от механической обработки. V — процесс пока не получил широкого распространения в нашей стране.
Преимущества технологии вакуумной формовки:
- Снижение издержек производства благодаря упрощению технологии изготовления литейных форм
- Увеличение ресурса работы всех элементов технологической оснастки
- Повышение точности и качества отливок
- Устранение операции обрубки и очистки поверхности отливок
- Повышение уровня экологической безопасности при проведении литейных операций
- Недостатки технологии:
- Необходимость поддержания вакуума в течение всего процесса изготовления отливки
- Усложнение оснастки и технологии ее изготовления
- Необходимость точного поддержания температуры пленки во избежание ее разрыва и образования брака литья
vakuumtest.ru
Особенности технологии вакуумно-пленочной формовки для литейного производства
Валеев Ильнар Эдуардович,Студент кафедры «Конструирование и технологии машиностроительных производств» ФГОУ ВПО Набережночелнинский филиал Казанского Национального Исследовательского Технического Университета им. А.Н. Туполева КАИ, г. Набережные Челны[email protected]Шапарев Александр Васильевич,Кандидат технических наук, доцент кафедры«Конструирование и технологии машиностроительных производств» ФГОУ ВПО Набережночелнинский филиал Казанского Национального Исследовательского Технического Университета им. А.Н. Туполева
КАИ, г. Набережные Челны
[email protected], [email protected]
Глухов Петр Васильевич,Студент кафедры «Конструирование и технологии машиностроительных производств» ФГОУ ВПО Набережночелнинский филиал Казанского Национального Исследовательского Технического Университета им. А.Н. ТуполеваКАИ, г. Набережные Челны[email protected]
Особенности технологии вакуумнопленочной формовки
для литейного производства
Аннотация.В наше время в литейном деле, при формовке сталкиваются с проблемами такими как: не высокая размерная точность отливок, износ используемых моделей, сложность изготовления тонкостенных отливок, большие припуски на механическую обработку, образование раковин в отливках и т.д. Целью моей работы является исследование технологии вакуумнопленочной формовки и предотвращение вышеуказанных проблем, тем самым улучшить качество отливок для последующей механической обработки.Ключевые слова:формовка, литьё, модель,вакуум.
Технология вакуумноплёночной формовки (ВПФ) медленно завоёвывает своё место среди других литейных технологий. В наше время в литейном деле, при формовке сталкиваются с проблемами такими как: не высокая размерная точность отливок, износ используемых моделей, сложность изготовления тонкостенных отливок, образование раковин в отливках и т.д. Целью данного исследования является изучение технологии вакуумнопленочной формовки и предотвращение вышеуказанных проблем, тем самым улучшить качествоотливок для последующей механической обработки.Данную технологию также называют как Vпроцесс. Важнейшей характеристикой данной технологии является использование сухого кварцевого песка без связующего, а также тонкой пластичной пленки при давлении вакуума от 0,3 до 0,6 бар. Отливки, полученные по Vпроцессу, характеризуются, прежде всего, высоким качеством поверхности и превосходной размерной точностью. При определенных условиях возможен также отказ от обычно необходимого уклона на модели. В отдельных, частных случаях это может устранить необходимость трудоемкой обработки.Описание вакуумнопленочной формовки.Рис.1 Технология ВПФ.
На закрытую камеру, из которой впоследствии удаляется воздух (пустотелый корпус формовочного стола), устанавливается плитас моделями отливки и элементами литниковой системы. Над натянутой на раму термопластичной пленкой (модельной пленкой) находится нагревательное устройство. Подогретая и поэтому пластичная пленка опускается на модель. В формовочном столе, устанавливается вакуум в 0,50,6 бар; пленка натягивается на модель, в точности повторяя ее контуры. После этого сверху на пленку пульверизатором наносится циркониевая противопригарная краска на спиртовой основе.Двустенная, оснащенная вакуумными трубами и всасывающими окнами (с внутренней стороны) опока опускается на модельную оснастку.Опока наполняется обычным сухим песком без связующего пластификата. Контрлад полуформы покрывается полиэтиленовой пленкой. Затем песок уплотняется между двумя слоями пленки посредством вакуума.После отключения вакуума в формовочном столе часть формы, с обеих сторон «закрытая» пленкой и далее удерживаемая вакуумом, снимается с модельной оснастки. Нижняя полуформа изготовляется и поворачивается аналогичным образом. Проставляются необходимые стержни; обе части формы собираются в готовую форму.Для получения отливки полой цилиндрической формы, отдельно в стержневых ящиках, изготавливают стержни. Внутрь засыпают смесь песка и смолы и продувают амином. Такой процесс называют «CoolBoxпроцессом».Пониженное давление поддерживается в процессе заливки и на начальном этапе затвердевания жидкого металла. При заливке пленка испаряется, либо сгорает под влиянием заливаемого металла. Под воздействием вакуума остатки пленки проникают в краску формы и вместе с частицами песка образуют тонкую оболочку, которая упрочняет поверхностный слой формы. Далее этот процесс поддерживается наносимым слоем краски.Для выбивки опоки вакуум отключается, песок «самотёком» высыпается, отливка освобождается для дальнейшей транспортировки.Преимущества вакуумнопленочной формовки:1.Отсутствие износа моделей.2.Возможность изготовления тонкостенных отливок.3.Использование оборотного формовочного песка без связующих.4.Уменьшение припусков на механическую обработку.5.Высокая размерная точность отливок.6.Низкие затраты на зачистку.7.Экологически чистая технология.Недостатки вакуумнопленочной формовки:1.Сложный процесс изготовления литейной формы.2.От начала и до конца технологического процесса используется вакуум.3.Отливки из стали имеют пригар (пенитрация).4.Процесс требует строгого соблюдения всех параметров технологического процесса.5.При механической обработке выявляются газовые раковины (обычно внизу отливки).К великому сожалению, царящий хаос знаний в области вакуумноплёночной формовки, отсутствие не всегда достоверной информации по результатам эксплуатации такого оборудования, отсутствие центров обучения специалистов и необходимого технологического сопровождения предприятий поставщиками оборудования либо специализированными организациями, шаг за шагом разрушает и до того ещё не окрепшее мнение литейщиков о целесообразности внедрения этой, действительно перспективной технологии, имеющей неоспоримые преимущества перед целым рядом других современных литейных технологий.Использование технологии вакуумноплёночной формовки впередовых предприятиях России и других странах уже на сегодняшний деньпозволило организовать выпуск сложных, ответственных отливок высокого качества, таких как отливки запорной арматуры и отливки для РЖД, разработатьуникальные, высокоэффективные литейные технологии на целый ряд отливок пользующихся спросом у потребителей, значительно снизить себестоимость выпускаемого литья и дальнейшей его механической обработки, уйти от использования дорогостоящих стержней, повысить культуру производства, в разы снизить уровень загрязнения производственных помещений и окружающей среды.Тщательная проработка технологий получение отливок, профессионализм при подборе необходимого литейного оборудованиявот залог получения качественного литья. Нельзя одну и ту же, ранее для когото разработанную технологию, слепо использовать в другом месте для получения своих отливок без их детальной технологической проработки, даже если она гдето хорошо работает.Самый распространённый дефект на отливках при литье ВПФ –это газовые раковины внизу отливки, которые вскрываются при механической обработке. Без специальной технологии, брак достигал свыше 50%.Рассмотрим данный дефект на примере отливки «Корпус буксы», отливка изготавливается по ВПФ.
Рис.2 Корпус буксы.
Характер дефекта следующий:
газовая пористость вскрывается после механической обработки;
расположение дефектатолько в нижней части отливки;
газовая пористость чистая, не имеет неметаллических включений;
раковины округлой формы, но разные по диаметру (от 2мм до 8мм).Основные предполагаемые причины возникновения газовой пористости:
высокая дозировка смолы в стержневой смеси;
не раскислённый металл;
переход заливки форм с чайникого на стопорный ковш, увеличение скорости заливки.Методом проб и ошибок пришли к следующему выводу:
газовая пористость никаким образом не связана со стержнями, с качеством металла, с влажностью формовочного песка или краски. Причина была в литниковой системе, в турбулентном течении металла в системе.
Рис.3 Литниковая система (1 вариант с фильтрами)
Рис.4 Литниковая система (1 вариант без фильтров)
Первый поток металла, проходящий через всю литниковую систему, протекает в турбулентном режиме. В некоторых местах он перетекает в ламинарное течение за счёт шлаковика и их тупиков. Но сам гидравлический удар, в момент попадания его в полость формы, ничем заглушить не возможно. В этот момент происходит разбрызгивание жидкой стали, начинает сгорать плёнка и в этовремя поступает огромный поток атмосферного воздуха. В эти первые секунды происходит окисление брызг жидкой стали атмосферным воздухом. В тех местах, где произошло окисление, там и выявляются газовые раковины.После заполнения жидким металлом определеннойчасти отливки, поток металла постепенно превращается в ламинарное течение. По этой причине в верхней части отливки дефектов не наблюдаются.
Рис.5 Литниковая система (2 вариант с фильтрами)
Решение проблемы установить внизу отливки промывник (резервуара для принятия первой порции холодного, окислённого металла и успокоения турбулентного потока). На основе этих выводов литниковая система для отливки «Корпус буксы» была изменена. Процент брака по газовой пористости резко сократился:1.За счёт конструкции литниковой системы, создание оптимальных условий по ламинарному заполнению полости формы (установление промывника).2.За счёт установления оптимального времени и температуры заливки форм жидким металлом. Температура заливки форм не ниже 1580 С.
Ссылки на источники1.MULTIBEST CORPORATION LTD [Электронный ресурс]. —Режим доступа: http://multibest.ru/page103, свободный. Загл. сэкрана. 2. Yam, K. L.,"Encyclopedia of Packaging Technology", John Wiley & Sons, 2009.3. Савин И.А., Акст Е.Р., Савина А.И. Радиационноиндуцированные процессы в чугунах, облучённых потоками ионов азота // Современные научные исследования и инновации,2014.№11[Электронныйресурс].URL:http://web.snauka.ru/issues/2014/11/39532 (дата обращения: 13.11.2014).4. Савин И.А., Методика теоретического расчета поверхностного натяжения металлических расплавов на основе физической модели энергетического состояния жидкости/ Савин И.А., Марков В.В. Нищенков А.В. Плохов С.В. //"Справочник. Инженерный журнал" (с приложением) Издательский дом «Спектр» г.Москва ISSN 0203347X № 5. 2014г. с.4852
e-koncept.ru
Vacuum-film forming
Vacuum-film forming.
Vacuum-film forming (V-процесс) – технология изготовления форм для литья с помощью термопластичной пленки. Получаемые отливки имеют улучшенные свойства: высокую размерную точность, чистую поверхность, меньшие механические напряжения за счет особых условий кристаллизации и охлаждения отливки, более плотную структуру, минимальное количество посторонних включений, высокое качество поверхности.
Description
Преимущества вакуумно-пленочной формовки и литья
Description:
Vacuum-film forming (V-процесс) – технология изготовления форм для литья с помощью термопластичной пленки. Данное название – “вакуумно-пленочная формовка” – распространилось и на процесс получения отливок в формы, созданные по данной технологии.
Литье в вакуум-пленочную форму имеет ряд преимуществ перед литьем в песчано-глинистые формы.
Процесс вакуумно-пленочной формовки происходит в несколько этапов.
На закрытую камеру, из которой впоследствии удаляется воздух (пустотелый корпус формовочного стола), устанавливается плита с моделями отливки и элементами литниковой системы. Над натянутой на раму термопластичной film (модельной пленкой) находится нагревательное device. Подогретая и поэтому пластичная пленка опускается на модель.
В формовочном столе, устанавливается vacuum at 0,5-0,6 have; пленка натягивается на модель, в точности повторяя ее контуры. После этого сверху на пленку пульверизатором наносится циркониевая противопригарная краска на спиртовой основе.
Двустенная, оснащенная вакуумными трубами и всасывающими окнами (с внутренней стороны) опока опускается на модельную оснастку. Опока наполняется обычным сухим песком без связующего пластификата. Контрлад полуформы покрывается полиэтиленовой пленкой. Затем песок уплотняется между двумя слоями пленки посредством вакуума.
После отключения vacuum в формовочном столе часть формы, с обеих сторон «закрытая» пленкой и далее удерживаемая вакуумом, снимается с модельной оснастки.
Нижняя полуформа изготовляется и поворачивается аналогичным образом. Проставляются необходимые стержни; обе части формы собираются в готовую форму.
Пониженное давление поддерживается в процессе заливки и на начальном этапе затвердевания жидкого metal. При заливке пленка испаряется, либо сгорает под влиянием заливаемого металла. Под воздействием вакуума остатки пленки проникают в краску формы и вместе с частицами песка образуют тонкую оболочку, которая упрочняет поверхностный слой формы. Далее этот процесс поддерживается наносимым слоем краски.
Для выбивки опоки вакуум отключается, песок «самотёком» высыпается, отливка освобождается.
Преимущества вакуумно-пленочной формовки и литья:
– получаемые отливки имеют улучшенные свойства: меньшие механические напряжения за счет особых условий кристаллизации и охлаждения отливки, более плотную структуру, минимальное количество посторонних включений, чистую поверхность, высокое качество поверхности,
– отсутствие износа моделей,
– снижение затрат за счет малого объема механической обработки отливки,
– возможность изготовления тонкостенных отливок,
– использование оборотного формовочного песка без связующих,
– уменьшение припусков на механическую обработку,
– высокая размерная точность отливок,
– низкие затраты на зачистку отливки,
– environmental friendliness,
– уменьшение трудозатрат.
RECOMMENDATIONS FOR THE USE OF TECHNOLOGY
CALL: +7-908-918-03-57
or use the search analogue technologies:
The unique technology SEARCH
or write to us here...card site
To come in check in
Victor PotekhinI received a question concerning cooperation, namely: identify areas of enterprise development and preparation of future development plans. Negotiations are currently underway. Baseline information will be analyzed, together we choose the innovative directions and plan.
2018-05-18 10:34:05Victor PotekhinI received a question regarding electrochemical machines. answered.
2018-05-18 10:35:57Victor PotekhinI received a question regarding pyrolysis plants for MSW incineration. answered. In particular, explained, that there are different pyrolysis installation: for combustion 1-4 hazard class and the rest. Accordingly, different technologies and prices.
2018-05-18 11:06:55Victor PotekhinWe receive a lot of requests for purchase of various goods. We do not sell or produce. But we maintain relationships with manufacturers and can recommend, give advice.
2018-05-18 11:08:11Victor PotekhinArrived in question hydroponnomu green feed. answered: we do not sell it. Asked to leave the application in the comments to, to its producers have fulfilled this request.
2018-05-18 17:44:35Victor PotekhinWe receive a lot of questions about technology. Please ask these questions below in the comments to records.
2018-05-23 07:24:36Andrey-245Not quite clear. This battery can not be charged at all or something? How many volts it produces? Where to buy? And is it possible to connect such series-parallel, collecting a normal battery, eg, for electric vehicle?
2018-08-23 10:09:48SergeyShefgood afternoon! Interesting the above installation. How can it be ordered ? What are the terms of cooperation from the author?
2018-08-27 17:07:42Victor PotekhinSergei, throw a link here to install. Or e-mail me [email protected]
2018-08-27 18:52:14SergeyShefI have asked you, how and where it can be bought?
2018-08-27 21:07:41SergeyShefWho made the sample, that you in the photo and whether to make to order?
2018-08-27 21:10:05Victor Potekhincan not understand, that during installation. throw off the link here
2018-08-27 23:15:16Victor PotekhinWe do not possess such information
2018-08-28 21:45:17NPC-soundgood afternoon! SergeyShef product similar to, It is represented title, and in principle, any article of the LTCC technology can be made at our factory JSC "NPC "SpetsElektronSistemy". We are in g. Moscow. You can write me an email [email protected]
2018-08-29 18:41:34NPC-soundIn our production there are probably the most complete set of equipment in Russia, which allows 3D micro, including LTCC technology, in a closed loop, from incoming inspection of materials, all intermediate production processes ...
2018-08-29 18:47:20JahanCryogels for plant growth and development under adverse conditions. who produce, how to find, to buy?
2018-08-30 23:48:23Victor Potekhinyou can buy from the manufacturer
2018-09-01 20:58:09Andrey-245Hello, Victor. I asked the question (2018-08-23) I meant about carbon battery, which serves as a 100 years old.
2018-09-18 12:15:33Victor Potekhinall information, that is, on the battery, It is written in the corresponding article.
2018-09-18 20:47:11Victor PotekhinTo get information about site technology manufacturers, write the bottom of the page - in FaceBook comments
2018-09-29 20:58:40DenssikAll the good days! I'm head of the center which developed the robot, on all matters concerning cooperation can write to the post office [email protected]
2018-10-03 17:19:46Victor PotekhinDenssik, Write pzhl about any work in question?
2018-10-03 19:10:33DS-SurferIf anyone there interested in "COMPLEX WATER BY hydrowave", I beg to contact me: [email protected] Sergei.The settings are made and implemented.
2018-11-07 12:23:40To post messages in the chat you need to login
вакуумно пленочная формовка технология видео клавиш в литейном производстве оборудование для вакуумно пленочной формовки купить
factor demand 144
comments powered by HyperCommentsxn--80aaafltebbc3auk2aepkhr3ewjpa.xn--p1ai
Состав противопригарного покрытия для пленок вакуумной формовки
Изобретение относится к области литейного производства, в частности к составам покрытия для пленок вакуумной формовки при производстве чугунных отливок. Цель изобретения - улучшение качества поверхности отливок за счет устранения пригара. Состав содержит мас.%: аморфный графит 25 - 30; кристаллический графит 5 - 15;инден-кумароновая или стирольно-инденовая смола 50 - 70. Покрытие приготовляют путем механического перемешивания размолотых и просеянных через сито термопластичной смолы и порошков графита. После нанесения состава на пленку последнюю нагревают , что приводит к образованию покрытия , прочно сцепленного с пленкой. При заливке формы расплавленным чугуном происходит термодеструкдия ингредиентов покрытия с образованием блестящего углерода и коксового остатка, откладывающегося на зернах песка и в пространстве между его зернами, что обеспечивает противопригарный эффект покрытия., повьшая тем самым качество поверхности отливок. Отсутствие пригара на отливках сокращает расходы на очистку литья и повышает производительность труда. 1 табл. а S (Л со 00
СО)ОЭ СОВЕТСКИХ
СОЦИАЛИСТИЧЕСКИХ
PEOlYEiflHH (19) (11) А1 (51) 4 В 22 С 3/00,9/02
ОПИСАНИЕ ИЗОБРЕТЕНИЯ
Н ABTOPCHOMY СВИДЕТЕЛЬСТВУ
ГОСУДАРСТВЕННЫЙ НОМИТЕТ СССР
ПО ДЕЛАМ ИЗОБРЕТЕНИЙ И ОТКРЫТИЙ (21) 3947309/22-02 (22) 15.08.85 (46) 15.05.87. Бюл. ))- 18 (72) И.М.Исаева, М.И.Аманацкая, М.Г.Шувалов и Ю.П.Чистухин (53) 621.744.079(088.8) (56) Авторское свидетельство СССР
У 1102653, кл. В 22 С 3/00, 1982.
Патент Японии У 52-2684, кл. В 22 С 9/02, 1977. (54) СОСТАВ ПРОТИВОПРИГАРНОГО ПОКРЫТИЯ ДЛЯ ПЛЕНОК ВАКУУМНОЙ ФОРМОВКИ (57) Изобретение относится к области литейного производства, в частности к составам покрытия для пленок вакуумной формовки при производстве чугунных отливок. Цель изобретения— улучшение качества поверхности отливок за счет устранения пригара.
Состав содержит мас.7: аморфный графит 25 — 30; кристаллический графит
5 — 15; инден-кумароновая или стирольно-инденовая смола 50 — 70. Покрытие приготовляют путем механического перемешивания размолотых и просеянных через сито термопластичной смолы и порошков графита. После нанесения состава на пленку последнюю нагревают, что приводит к образованию покрытия, прочно сцепленного с пленкой.
При заливке формы расплавленным чугуном происходит термодеструкция ингредиентов покрытия с образованием "блестящего углерода" и коксового остатка, откладывающегося на зернах песка и в пространстве между его зернами, что обеспечивает противопригарный эффект покрытия,, повышая тем самым качество поверхности отливок.
Отсутствие пригара на отливках сок- ращает расходы на очистку литья и повышает производительность труда.
1 табл.
1310093
Стирольно-инденовая или инденкумароновая
50 60 70 смола
55
Изобретение относится к литейному производству и может быть испольэовано в качестве протинопригарного покрытия при производстве отливок из чугуна методом вакуумно-пленочной формовки.
Цель изобретения — улучшение качества поверхности отливок за счет ус раггения пригара.
В качестве огнеупорного углеродсодержащего наполнителя используется аморфный и кристаллический графит с модулем мелкости 250 и 100 соответственно.
Кристаллический графит повышает термостойкость противопригарного покрытия, а аморфный графит является источником образования блестящего углерода".
Оптимальное соотношение аморфного и кристаллического графита в покрытии 3: 1.
Б качестве связующего используются синтетические смолы инден-кумароновая или стирольно-инденовая.
Инден-кумароновая и стирольноинденовая смолы представляют собой гранулы или пластинки темно-коричневого цвета. Эти смолы выделяют при термодеструкции большое количество
"блестящего углерода" (45-557), благодаря чему обладают высокими противопригарными свойствами.
Температура размягчения смол равна 80 — 140 С и близка к температуре пластификации полимерной пленки,применяемой при вакуумной формовке.
Составы противопригарных покрытий приведены в таблице.
Ингредиенты Содержание ингредиентов, мас.X в составах
Аморфный графит 35 30 25
Кристаллический графит 15 10 5
Прртивопригарное покрытие готовят путем механического смешивания
45 размолотой в бегунах и просеянной через сито термопластичной смолы и порошков графитов.
Приг.отовленная указанным способом смесь насеивается слоем толщиной в среднем 1,0 мм на полимерную пленку, закрепленную на рамке. После этого пленку с покрытием нагревают.
Так как смолы имеют температуру pasмягчения, равную температуре пластификации полимерной пленки, то одновременно с нагревом пленки и ее прилипанием смола плавится и обволакивает порошковый графит. При вакуумировании внутренней полости подмодельной плиты рамку с размягченной пленкой и покрытием опускают «а металлический модельный комплект, который плотно обтягивают пленкой.При этом происходит фиксация пленки на модели и одновременно затвердевание противопригарного покрытия, которое прочно сцепляется с поли" мерной пленкой, облегающей модель и подмодельную плиту.
При заливке формы расплавленным чугуном происходит выделение "блестящего углерода из смолы и аморфного графита, который откладывается на зернах песка и в пространстве между зернами, что обеспечивает несмачиваемость формы расплавом.Одновременно между зернами песка формы осаждается коксовый остаток,образующийся за счет термодеструкции кристаллического и аморфного графитов который оказывает механическое сопротивление проникновению жидкого расплава в поры песка.
Образующийся эа счет выделения блестящего углерода и эакупоривания пор песка коксовым остатком противопригарный эффект способствует устранению пригара на чугунных отливках, повышая тем самым их качество.
Отсутствие пригара на отливках при использовании покрытий предлагаемого состава сокращает расходы на очистку литья и повышает производительность труда.
Формула изобретения
Состав противопригарного покрытия для пленок вакуумной формовки при производстве чугунных отливок, включающий углеродсодержащий наполнитель и синтетическую смолу, о т л и ч а1310093
50 — 70
Составитель В.Решетов
Редактор Н.Киштулинец Техред А.Кравчук Корректор А.Тяско
Заказ 1824/9 Тираж 741 Подписное
ВНИИПИ Государственного комитета СССР по делам изобретений и открытий
113035, Москва, Ж-35, Раушская наб., д. 4/5
Производственно-полиграфическое предприятие, r. Ужгород, ул. Проектная, 4 ю шийся тем, что, с целью улучшения качества поверхности отливок за счет устранения пригара, он в качестве углеродсодержащего наполнителя содержит кристаллический и аморфный графит, а в качестве синтетической смолы — инден-кумароновую или стирольно-инденовую смолу при следующем соотношении ингредиентов, мас.7:
Аморфный графит 25 — 35
Кристаллический графит 5 — 15
Инден-кумароновая или стирольно-инденовая смола
www.findpatent.ru
Вакуумно-пленочная формовка.
Технологический процесс, основные принципы и особенности:
1. В процессе производства используется специальная вакуумная форма с вытяжной камерой и с отверстиями для откачки воздуха.
2. Нагретую до размягченного пластичного состояния пленку из полимерного материала помещают на заранее подготовленную форму. Затем вакуумный насос выкачивает воздух. Это приводит к тому, что под действием приложенной силы вакуумного насоса полимерная пленка плотно прижимается к форме и оформляется в готовое изделие.
3. Затем на уже прижатую к форме пленку из полимерного материала накладывается опока, оборудованная трубой для откачки воздуха со специальным фильтром.
4. Внутренняя часть опоки заполняется специальным сухим формовочным песком, не имеющим спаивающих (вяжущих) веществ и других дополнительных примесей. Мелкими встряхиваниями вибростола достигается уплотнение заполнителя опоки, удаляются излишки засыпного материала, а сверху опока накрывается полимерной пленкой, необходимой для уплотнения заполнителя. После этого открывается клапан трубы для откачки воздуха, что приводит к возникновению вакуума в формовочном песке. В результате этого возникает разница внешнего и внутреннего давления на форме (приблизительно 300~400 миллиметров ртутного столба). Благодаря указанной разнице давлений получается форма для литья, обладающая достаточно высокой жесткостью. Значение жесткости формы по шкале твердости может достигать плюс-минус 95.
5. После полного окончания приложения усилия вакуума внутри формы, указанную форму необходимо извлечь, чтобы получилась полость. Усилие должно прилагаться к форме до тех пор, пока форму можно будет извлечь без особых усилий и без ущерба для полученной полости для заливки. Нижнюю часть опоки изготавливают точно также, как и описано выше для верхней части опоки.
6. В форму устанавливаются различные литейные стержни, затем после формовки изделия они убираются, нижняя и верхняя части опоки совмещаются и происходит залитие формы.
7. Усилие вакуумного насоса должно прилагаться вплоть до полного затвердевания изделия. После полного затвердевания изделия, прекращается откачка воздуха из формы. И когда давление внутри формы начнет приближаться к атмосферному, нижняя и верхняя части формы автоматически распадутся.
Важные моменты:
(1) разница внешнего и внутреннего давления на форме обеспечивает необходимую жесткость и прочность изделия, а также точное соответствие изделия выпуклостям и полостям формы.
(2) при подсоединение вакуумного насоса, труба для откачки воздуха, оборудованная специальным фильтром, должна устанавливаться в соответствующее место верхней и нижней опоки еще до начала заполнения их песком, но после помещения туда модели и литейных стержней, а также после накладки на опоки пленок для уплотнения заполнителя.
Преимущества V-формовки:
• Повышается качество формовки изделий: поверхность формованного изделия гладкая и чистая, изделие обладает четкими краями и очертаниями, кроме того, размеры готового изделия строго соответствуют заданным. Готовое изделие обладает высокой степенью твердости, твердость изделия равномерна. Легкость извлечения модели будущего изделия из литейной формы.
• Простота используемого оборудования, низкие капиталовложения, невысокие расходы на техническое обслуживание и профилактический ремонт, связанные с функционированием и эксплуатацией указанного оборудования. Это все указано без учета соответствующего оборудования, используемого в процессе производства и служащего для отбора материалов с низким количеством посторонних примесей, отбора материалов, обладающих низкими вяжущими свойствами, и предназначенного для смешивания материалов. Коэффициент использования отработанной формовочной смеси составляет приблизительно 95% и выше. Капиталовложения в оборудование уменьшается на 30%. Энергетические затраты при использовании данного оборудования составляют 60% от оборудования, применяемого при литье «влажного» типа. Затраты людских ресурсов уменьшаются на 35%.
• Долговечность эксплуатации литейной формы и опоки.
• Высокий коэффициент использования металла. При использовании формовки V типа, металл обладает сравнительно хорошей активностью, хорошей способностью к заполнению формы. Можно производить тонкостенные детали с толщиной стенки всего 3мм. Готовые изделия обладают высокой степенью жесткости, медленно охлаждаются. При использовании дополнительных скрепляющих приспособлений значительно уменьшается выпор отливки. Повышается производительность, уменьшается припуск на обработку изделий
.
Недостатки:
• Сложный процесс изготовления литейной формы, трудно увеличить производительность изделий малой формы.
• От начала и до конца технологического процесса используется вакуум, тяжело механизировать труд.
• Из-за того, что на заготовки из полимерных материалов накладывают ограничения по тягучести и пластичности материала, то это ограничивает сферу применения указанной технологии.
• Проблема пыли и охлаждения формовочной смеси.
Основное технологическое оборудование:
1. Водокольцевой вакуум-насос модели SK-12. Следует уделить внимание удалению пыли с модели!
2. Вибростол:
переменного типа: модель DZ-300W, частота колебаний(Гц) тип вибратора 3000 об/мин. Двойная амплитуда 1.5мм.
3. Нагревательные элементы для размягчения и пластификации пленки из полимерных материалов: пластина с нагревательными элементами, принцип действия которых основан на использовании тепловой энергии лучей дальней (коротковолновой) ИК-области спектра излучения. Для размягчения и пластификации также можно использовать нагревательные элементы, отдающие тепловую энергию при помощи открытого огня, либо принцип действия которых основан на излучении тепла при прохождении через них электрического тока.
Чтобы тепло распространялось равномерно, нагревательные элементы, находящиеся на пластине нагревателя, располагают в три группы А, В, С. В процессе функционирования установки электрическая схема управления нагревом использует каждую группу нагревательных элементов в отдельности, и тем самым регулирует температуру каждой из групп нагревательных элементов, распределяя его равномерно.
4. Формы и отъемные части формы.
Диаметр отверстия для откачки воздуха составляет 2~3мм.
Необходимо обеспечить плотное прилегание пленки из полимерных материалов к форме. В местах неплотного прилегания пленки к форме следует дополнительно просверлить еще одно маленькое отверстие.
5. Опока с трубой для откачки воздуха со специальным фильтром и отъемные части формы.
Способ откачки воздуха:
- по трубопроводам для откачки воздуха,
- из боковой вытяжной камеры,
- комбинированный способ.
При использовании трубопроводов для откачки воздуха (для изготовления трубопроводов для откачки воздуха можно использовать металлизированные гофрированные шланги от электрических проводов) на них должны быть установлены специальные просеивающие фильтры, размер ячейки которых должен быть меньше среднего размера песчинок формовочного песка.
1). Выбор формовочного песка:
Формовочный песок должен обладать достаточной степенью проницаемости, при этом, чем меньше размер песчинок, тем проницаемость будет ниже.
Наличие в песке различных примесей, а также смешивание формовочных песков различных марок может привести к возникновению песчаных раковин.
2). При использовании метода вакуумной формовки легко получить дефект формы.
(1). Наличие литейного пригара:
Способ предотвращения образования пригара: необходимо использовать достаточно мелкий формовочный песок, температура заливаемого материала должна быть достаточно низкой, повышение плотности формы. Степень вакуума должна быть достаточно низкой. Верхний слой полимерной пленки должен быстро высыхать.
(2). Провалы: нарушена герметичность.
Способ предотвращения возникновения провалов:
① плавная заливка, постоянное наполненные литниковой системы;
②плотное прилегание полимерной пленки;
③использование литниковой системы открытого типа.
(3). Появление трещин и утолщений.
Способ предотвращения :сжатие материала, припуски для формы.
Поліпшення умов праці - один з найважливіших напрямів економічної і соціальної політики нашої держави, закріплений Конституцією України і регламентований спеціальними правилами і нормами. Особливо актуальним з цієї точки зору є рішення проблеми збереження і зміцнення здоров'я металургів, праця яких пов'язана з виробництвом, яке характерізується високими темпами, великими об'ємами і навантаженнями, наявністю великої кількості небезпечних і шкідливих факторів.
infopedia.su