Защита бетона в жару. Pvb пленка свойства
Триплекс – технология производства и свойства
Стеклянный пол (перекрытие второго этажа, триплекс 32 мм)
Ламинированное многослойное стекло, называемое триплексом, состоит из двух и более стеклянных листов, соединенных между собой ламинирующей пленкой. Триплекс может быть полностью прозрачным или цветным, распространены также многослойные стекла молочного матового оттенка. Оптические и физические свойства триплексного стекла определяются числом слоев и типом используемой пленки. Выделяют три основных технологии производства триплекса.1. Этиленвинилацетатная пленка (EVA). Изготовленный по этой технологии триплекс не обладает высокой прочностью. Главным достоинством данной технологии является низкая стоимость требуемого оборудования для производства и расходных материалов. Также не требуются значительные производственные площади. Основным инструментом для изготовления триплекса EVA является многофункциональная печь, оснащенная вакуумными мешками из силикона.Низкая стоимость стекол EVA не всегда способна компенсировать их многочисленные недостатки. При многослойном ламинировании пленкой EVA часто возникают опалесцирующие замутнения. Матовый триплекс EVA начинает желтеть уже после года эксплуатации. Прочность на удар и сдвиг очень невысока. При низких температурах окружающей среды возможно расслоение триплекса. Также пленка начинает отслаиваться при повышенной влажности. Со временем на стекле возникают локальные расслоения в виде пузырей.Триплекс EVA пригоден к использованию только в декоративных целях и лишь при хороших эксплуатационных условиях.2. Поливинлбутиральная пленка (PVB). Пленка PVB обладает очень высокими адгезивными способностями к стеклу и почти не приклеивается к пластику. Готовый триплекс PVB обладает очень высокими эксплуатационными характеристиками. Мутность практически отсутствует, стекла очень прочные, толщина равномерна по всей площади, триплекс не боится значительных перепадов температур. Для производства триплекса PVB требуется большое количество специального дорогого оборудования. Необходим автоклав, горячий пресс, стерильное помещение. Минимальная площадь для размещения производственной линии триплекса PVB составляет 500 квадратных метров. Помещение должно быть оснащено автоматизированной климатической системой с контролем влажности. Пленка PVB портиться и не может быть использована в производстве при влажности превышающей 25 процентов.Стекла с пленкой PVB могут использоваться в качестве защитных. Они полностью соответствуют требованиям ГОСТ к защитным, ударостойким и бронированным стеклам.3. Термопластичный полиуретан (TPU). Триплекс с пленкой этого типа обладает высочайшими характеристиками. Он полностью прозрачен, выдерживает сильнейшие механические нагрузки, невосприимчив к агрессивным средам и высокой влажности. Производится триплекс TPU автоклавным способом. И пленка, и необходимое для создания производства оборудование обладают очень высокой стоимостью. Это является причиной того, что триплекс TPU практически не используется в быту. Сфера применения такого триплекса ограничена специальными конструкциями. В частности триплекс TPU используется для остекления в аэрокосмической отрасли.Приобретая триплекс необходимо убедиться, что он соответствует заявленным продавцом характеристикам. В последнее время значительно участились случаи продаж дешевого триплекса с пленкой EVA под видом высококачественного PVB. Определить разницу по внешнему виду практически невозможно. Так как осмотр производственной линии в подавляющем большинстве случаев проблематичен, можно воспользоваться примитивным, но надежным методом. Если разбить небольшой фрагмент триплекса, то с пленки EVA практически все осколки отпадут сразу. Пленка PVB практически не даст осколков, все стекло останется на ней.
mosstek.ru
Оптические свойства полимерных пленок
Полимерные пленки и синтетические ткани также находят применение при уходе за бетоном.
Классификация пленок по химическим признакам позволяет разделить их на три самостоятельных группы: пленки из природных, искусственных и синтетических полимеров.
Технологическая классификация пленок основана на различиях в способах изготовления: из растворов, дисперсных систем или расплавов полимеров.
Самую обширную группу составляют пленки на основе синтетических полимеров. Наибольшее распространение из этой группы получили пленки на основе полиолефинов, поливинилхлорида, полиамида, полиэтилентерефталата.
Первостепенное влияние на формирование температурного режима в твердеющем бетоне оказывают оптические свойства полимерных пленок. Например, коэффициент интегрального светопропускания полиэтиленовой пленки составляет: 92% при толщине 0,02-0,1 мм; 90% - 0,1-0,2 мм; 88% - 0,2-0,35 мм; 84% - 0,35-0,5 мм.
Оптические свойства пленок (табл. 2) зависят от химического состава полимера, присутствия в нем стабилизаторов и красителей. Например, введение в состав полиэтилена 0,2-0,5% двуокиси титана на 20% снижает прозрачность в видимой части спектра и до 45% в инфракрасной, а 1-2% газовой сажи делает ее в этих областях непрозрачной.
Определенный интерес представляют полимерные пленки с функциональным защитным покрытием, металлизированные. В частности при одинаковой толщине полиэтилентерефталатной пленки слой алюминия 0,03-0,07 мкм придает ей новые оптические свойства.
Таким образом, полимерные пленки обладают многими положительными свойствами, благодаря которым их можно широко применять для ухода за бетоном при возведении монолитных сооружений.
Таблица 2. Оптические свойства полимерных пленок
Пленки | Спектральная область | |||||
видимая | инфракрасная | |||||
пропускания | отражения, | поглощения | пропускания | отражения | поглощения | |
Полиэтиленовая нестабилизированная неокрашенная | 0,72 | 0,10 | 0,18 | 0,80 | 0,08 | 0,12 |
Полиэтиленовая с титановым наполнителем | 0,80 | 0,13 | 0,07 | 0,55 | 0,20 | 0,25 |
Полиэтиленовая с сажевым наполнителем | 0 | 0,04 | 0,96 | 0 | 0,06 | 0,94 |
Поливинилхлоридная марки В | 0,72 | 0,16 | 0,12 | 0,52 | 0,16 | 0,32 |
Полиэтилентерефталатнал прозрачная | 0,86 | 0,11 | 0,03 | 0,86 | 0,07 | 0,07 |
Полиэтилентерефталатная металлизированная | 0 | 0,85 | 0,15 | 0 | 0,80 | 0,20 |
www.stroimt.ru
Удивительные свойства упаковочной пленки
А.Л. Волынский, член-корреспондент РАН, д.х.н., проф., гл.н.с.
Иногда случается так, что хорошо известные и изученные предметы и явления вдруг открываются новыми и необычными сторонами. Именно это произошло при исследовании упаковочной полимерной пленки на нашей кафедре. Казалось бы, что в ней особенного? Это просто упаковочный материал, без которого быт современного человека совершенно немыслим: металлизированные полимерные пленки (как правило, с тонким алюминиевым слоем) используют, например, для упаковки цветов, продуктов, промышленных товаров, применяют в полиграфии и во многих других областях. Неудивительно, что такие полимерные материалы выпускаются сегодня сотнями тысяч тонн.
Вполне естествен и интерес самых разных специалистов к столь распространенным в быту и промышленности объектам. Уже многие годы издается журнал “Thin Solid FILMs” (“Тонкие твердые пленки”), где освещаются научные и прикладные аспекты проблем, связанных с изучением и использованием систем, которые можно обозначить как “твердое покрытие на податливом основании”.
Удивительно, что при всем том научном интересе, который проявляют исследователи к подобным системам, до недавнего времени никому не пришло в голову просто растянуть упаковочную армированную пленку (она как раз и представляет собой типичную систему “твердое покрытие на податливом основании”) и посмотреть, что из этого получится. А посмотреть, как оказалось, есть на что: в микроскоп (сканирующий электронный) видны ряды светлых полос с регулярным волнистым рельефом, разделенных темными полосами.
Что это за ряды и каким образом они появляются?
Растягивая полимерную пленку, на которую твердое покрытие нанесено тонким слоем, мы растягиваем одновременно и этот слой. В результате покрытие распадается на множество “островов”-фрагментов. Они-то и “выстраиваются” рядами, образуя своеобразный рельеф. Поражает регулярность самопроизвольно возникающего рельефа и его строгая ориентация относительно оси растяжения: его углубления и вершины всегда ориентированы строго параллельно оси. Высока и степень порядка, достигаемая при фрагментации покрытия: образующиеся острова однородны по размерам и располагаются на поверхности податливой подложки весьма регулярным образом. Другими словами, на растянутой полимерной пленке возникают высокоорганизованные периодические структуры. Именно поэтому деформированная упаковочная пленка рассеивает свет, как настоящая дифракционная решетка.
А всегда ли проявляются подобные результаты растяжения? Может быть, они зависят от природы подложки (полимера) и покрытия? Мы это выяснили, взяв для экспериментов один и тот же полимер, но с разным покрытием, и наоборот - одно покрытие на разных полимерах.
Микрофотографии трех видов растянутых пленок, армированных разными металлами.
Ось растяжения показана стрелкой. Увел. (слева направо): в 350 раз, 1100 и 1750.
Никакой зависимости мы не обнаружили, всякий раз возникали уже знакомые нам структуры. Правда, необходимо было соблюдать два условия:
- толщина покрытия должна быть пренебрежимо малой по сравнению с толщиной подложки;
- модуль упругости покрытия должен на несколько порядков превышать этот показатель для материала подложки. Именно таким требованиям соответствует упаковочная пленка [1, 2].
Теперь вполне правомочен вопрос: каким образом при простом растяжении возникает столь регулярная структура? Попробуем разобраться в механизме наблюдаемого явления. Примем во внимание, что полимерная пленка, подвергаемая одноосному растяжению, испытывает одновременно два вида деформации - удлинение и сжатие в перпендикулярных друг другу направлениях. (В этом легко может убедиться каждый, растягивая кусок резиновой ленты.) Следовательно, твердое покрытие на поверхности пленки тоже растягивается и сжимается одновременно. Именно сжатием покрытия, как выясняется, обусловлено возникновение регулярного микрорельефа. Какова же физическая суть этого процесса?
Покрытие, представляющее собой анизодиаметричное твердое тело (т.е. с очень разными размерами в перпендикулярных направлениях), испытывает деформацию одноосного сжатия на поверхности растягиваемой полимерной пленки. Надо сказать, что впервые явления, сопровождающие одноосное сжатие анизодиаметричных твердых тел, были рассмотрены Л.Эйлером более 200 лет назад. Он показал, что тело при достижении критической нагрузки теряет устойчивость и приобретает форму полуволны (так называемая эйлеровская классическая потеря устойчивости). Подобное легко наблюдать, сжимая, например, тонкую металлическую линейку или лист бумаги. Если же анизодиаметричное твердое тело (в нашем случае это тонкое жесткое покрытие) прочно связать с податливой подложкой (основанием), то картина потери им устойчивости решающим образом изменяется. При достижении критической сжимающей нагрузки тело не сможет принять форму полуволны, так как при отклонении от прямолинейной формы на него будет действовать со стороны подложки возвращающая сила, пропорциональная величине отклонения. В результате такого взаимодействия противоборствующих сил покрытие неизбежно сложится, подобно складному метру, и примет синусоидальную форму с периодом волны, равным l.
Схема потери устойчивости анизодиаметричного тела в свободном состоянии (а, б) и на податливом основании (в, г).
Величина периода волны (рельефа) определяется следующим. Работа деформации при сжатии анизодиаметричного твердого тела - покрытия - растет с увеличением числа совершенных изгибов (с уменьшением периода рельефа). Не случайно, что без подложки такое тело принимает форму полуволны, т.е. период рельефа максимален. Однако податливая, но весьма протяженная подложка вносит поправки в этот процесс. Очевидно, что чем больше период рельефа, тем, при прочих равных условиях, больше его амплитуда. Полимерная подложка не остается безучастной к ее увеличению - она “течет”, деформируется. Энергетические затраты всей системы при этом стремятся к минимизации. Период рельефа можно найти из условия минимума общего баланса напряжений в покрытии и подложке.
Такого рода минимизация энергии системы в случае упругой каучуковой подложки дает величину периода рельефа
l = 4.15h·(E1/E)1/3, (1)
где h - толщина покрытия, E1 и Е - модули упругости покрытия и подложки соответственно.
Если же подложка пластична, период рельефа равен
l = 2hsy /s, (2)
где sy - предел текучести покрытия, s - предел текучести подложки при растяжении. Расчеты для того и другого случая экспериментально подтверждены. Хорошее соответствие теории и эксперимента свидетельствует о разумности предположений, сделанных относительно механизма возникновения регулярного рельефа на поверхности упаковочной пленки.
Регулярность фрагментации жесткой оболочки связана, кроме того, с особенностями передачи механического напряжения от податливого основания твердому покрытию через границу раздела. Здесь необходимо отметить, что характер самой фрагментации зависит, в частности, от того, однородно или неоднородно деформируется подложка. Полимерные пленки могут деформироваться обоими путями. Хотя деформация подложки достигается разными способами, регулярность фрагментации твердого покрытия оказывается неизбежной.
В случае однородной деформации полимера-подложки вначале, при малых ее удлинениях, решающий вклад в разрушение покрытия вносят поверхностные микродефекты (характерные для любого твердого тела), которые и инициируют процесс в местах своей локализации. Такого рода дефекты располагаются в покрытии хаотически, что и вызывает нерегулярность его разрушения: образуются фрагменты разных размеров. При дальнейшем растяжении подложки фрагменты остаются под нагрузкой, но напряжение в разных частях каждого из них распределяются крайне неравномерно: от близкого к нулевому на концах фрагмента до максимального точно в его центре. Именно здесь в первую очередь напряжение достигает предела прочности, и фрагмент делится на две равные части. Этот процесс можно наблюдать в сканирующем электронном микроскопе. Такое деление продолжается до тех пор, пока слабая податливая подложка способна передавать фрагментам напряжение, превышающее прочность покрытия. Когда их размеры становятся слишком малы для передачи подложкой разрушающего напряжения, деление заканчивается. На поверхности полимерной пленки возникает система из весьма выровненных по размерам фрагментов покрытия.
При неоднородной деформации полимерной пленки непрерывно сосуществуют ее исходный участок и деформированный фрагмент, уже перешедший в ориентированное состояние (так называемая шейка).
Это означает, что одновременно существуют также и две части покрытия: распавшаяся на фрагменты на шейке полимера и целая, не разрушенная часть, покрывающая его исходный участок. События, связанные с фрагментацией покрытия, разыгрываются в узкой перемещающейся зоне, расположенной между ориентированной и неориентированной частями растягиваемого полимера. В этой зоне всегда присутствует край разрушенного покрытия, напряжение в котором, очевидно, близко нулю. По мере удаления от края напряжение растет и быстро достигает предела прочности покрытия. Тогда-то и отрывается его очередная полоса, причем ширина всех полосчатых фрагментов оказывается почти одинаковой.
При таком виде деформации подложки из покрытия фактически образуется система почти не отличимых по размерам тончайших параллельных лент, которые тянутся от одного края растягиваемого образца до другого. Возникновение столь уникальной структуры, как видим, обусловлено особенностью неоднородной деформации полимерной пленки в системе “твердое покрытие на податливом основании”.
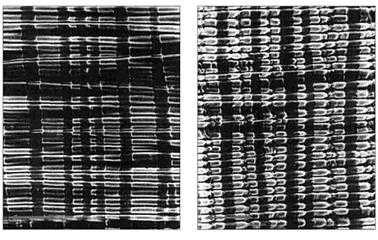
mirznanii.com
7.4. Нанесение покрытий на полимерные пленки. Типы и свойства покрытий
7.4. Нанесение покрытий на полимерные пленки.
Типы и свойства покрытий
7.4.1. Основы нанесения покрытий
Нанесение покрытий на поверхность полимерных пленок применяется для улучшения их способности к термосвариванию и барьерных свойств, а также в целях улучшения барьерных свойств жестких пластмасс. Традиционно наиболее распространенным методом нанесения покрытий на пленки было использование гравировального (травленого) валика, поскольку он обеспечивает непрерывное и точное нанесение с удельным расходом материала покрытия до 6 г/м2. Нанесение таких покрытий проводится изготовителями пленок в промышленных масштабах. Если же требуется более толстое покрытие, то его наносят уже на упаковочных предприятиях.
С учетом важности экологических проблем были разработаны системы покрытий на водной основе. В настоящее время очень редко можно встретить системы покрытий на основе растворителей, но там, где они используются, получают их в основном на основе спиртов, причем растворителем с наиболее высокой температурой кипения является бутанол. Применяется покрытие праймером (грунтовка). Если покрытие должно наноситься с обеих сторон пленки, то праймер наносят одновременно с двух сторон с помощью гравировальных валиков, вращающихся в противоположных направлениях. Здесь очень важна адгезия покрытия к пленке-основе, так что обычно применяют покрытие адгезионного типа с антистатическими свойствами массой 1 г/м2.
Некоторое время была популярна металлизация алюминием, которую проводят путем перевода алюминия в парообразное состояние в вакуумной камере с последующим его осаждением на поверхность полимерной пленки, бумаги или картона. Позднее стали использовать SiOv — смесь оксидов кремния, которую осаждали тонким слоем на различные полимерные пленки. Вполне вероятно, что в дальнейшем свое применение к упаковке (и для бутылок, и для пленок) найдут и другие покрытия, в частности, DLC, алмазоподобное покрытие на основе углерода, которое изначально было разработано для отделки внутренней поверхности ПЭТ-бутылок.
Одним из способов нанесения покрытий на полимерные материалы является экструзионное нанесение; этим термином обычно называют нанесение полимеров на другие материалы — алюминиевую фольгу, бумагу и картон. Нанесение покрытий как способ улучшения свойств полимерных пленок и пластиковых контейнеров представляет собой область активных инноваций.
7.4.2. Акриловые покрытия
Акриловые покрытия наносят на полимерные пленки, особенно на ОПП-пленки. Такое покрытие является совершенно прозрачным, термосвариваемым и обеспечивающим высокий глянец. Температура начала термосваривания составляет около 100°С, а температура плавления четко определена. Это означает, что такое покрытие легко скользит по нагретой поверхности без прилипания к ней. Обычно приемлемым нижним пределом прочности сварного шва является 250 г ■ м~2/25 мм ширины шва. При температуре усаживания пленки в 150 °С это расширяет температурный диапазон сварки на 50 °С. Для улучшения эксплуатационных показателей упаковочной машины в состав покрытия должны быть включены некоторые скользящие и антиблокирующие добавки. Расход покрытия обычно составляет около 1,0 г/м2 и при его удельной массе около 1, что дает толщину покрытия в 1 мкм.
7.4.3. Покрытия на основе ПВдХ
Покрытия из ПВДХ используются для получения полимера или с хорошей способностью к термосвариванию, или с высокими барьерными свойствами. Между требуемой способностью к термосварке и барьерными свойствами можно найти компромисс. Модификация полимера для расширения температурного интервала сварки снижает нижнюю границу температуры термосварки до 110 "С за счет барьерных свойств по отношению к газам. Покрытия из ПВДХ наносят на полимерные пленки и бумагу.
Большинство применяемых покрытий общего назначения характеризуются способностью к термосварке, начиная с температур 120 "С, а барьерные свойства по отношению к кислороду составляют около 25 мл/м2 • сут. Для ПЭТФ-пленок покрытия из ПВдХ обычно применяют для улучшения барьерных свойств по отношению к кислороду (10 мл/м2/сут), но такие пленки могут плохо термосвариваться.
Композиция покрытия должна включать кремний и воск (в качестве скользящих и антиблокирующих добавок для предотвращения прилипания покрытий к горячим сваривающим поверхностям). Обычно производители пленок наносят покрытия с расходом 3 г/м2, то есть толщиной в 2 мкм. Удельная масса ПВдХ — 1,3. Такие покрытия могут наноситься на жесткие емкости типа ПЭТ-бутылок для пива.
7.4.4. Покрытия на основе PVOH
С экологической точки зрения при сжигании хлорсодержащих соединений могут выделяться токсичные диоксины, и поэтому долгое время для замены ПВДХ искали альтернативный материал с повышенными барьерными свойствами по отношению к газам без необходимости модифицировать технологические параметры нанесения покрытия. Этому требованию отвечают эмульсии PVOH, но они чувствительны к влаге и теряют свои барьерные свойства при повышении относительной влажности более чем на 65%. Пленки с покрытием из PVOH, следовательно, можно использовать как часть ламината, у которого внутри расположен слой PVOH, а снаружи — слои БОПП с PVOH (при условии, что наружная сторона покрыта защитным лаком). Кроме того, PVOH не имеет способности к термосвариванию, но он отлично впитывает типографские краски с низкой абсорбцией или удержанием растворителей. Удельный расход при нанесений PVOH-покрытия аналогичен ПВдХ, его удельная масса около 1,0, а выход пленки несколько выше.
7.4.5. Низкотемпературные свариваемые покрытия
Низкотемпературные свариваемые покрытия (LTSC) для ОПП, которые можно сваривать при более низких температурах и которые характеризуются более широким диапазоном температур термосваривания, позволяют повысить скорость работы упаковочных машин. Эти покрытия основываются на иономерных смолах и наносятся в виде эмульсий, так что могут служить альтернативой акриловым и ПВдХ- покрытиям. Поскольку диоксид кремния и воски способны увеличить температурный порог сварки любых покрытий, стремятся снизить их содержание до минимума так, чтобы трение с 1Г5С-покрытием было выше, чем с обычными покрытиями. Низкотемпературные свариваемые покрытия не прилипают к ПВдХ- или акриловым покрытиям и не блокируют их, так что можно получать пленки с разными вариантами покрытий. Поверхность этого иономера хорошо впитывает типографские краски и не удерживает их растворители.
7.4.6. Металлизация алюминием
Рис. 7.13. Процесс металлизации (с разрешения Institute of Packaging) |
Прямая вакуумная металлизация полимерных пленок алюминием существенно повышает их барьерные свойства. Это становится возможным благодаря гладкости пленок, так что покрытие на них имеет равномерную толщину. Металлизируют главным образом ПЭТ-, ПА- и ОПП-пленки. Себестоимость такой пленки во многом обусловлена временем, необходимым на создание вакуума после смены рулона. Предпочитают использовать ПЭТ-пленку толщиной 12 мкм, поскольку при этой толщине больше общая площадь пленки в рулоне. Металлизация ПЭТ-пленки позволяет использовать ее для последующей металлизации бумаги и картона путем перевода покрытия с пленки на подложку с помощью нагретых прижимных валков, после чего ПЭТ-пленку можно использовать повторно (рис. 7.13).
7.4.7. SiO-покрытия
В качестве покрытия оксиды кремния стали использоваться сравнительно недавно. Этот материал характеризуется отменными барьерными свойствами и наносится методом осаждения в вакууме. ПЭТ-пленка с SiO -покрытием производится в промышленных масштабах и используется в Японии для изготовления стерилизуемых ламинированных пакетов. Такой материал прозрачен, может стерилизоваться в автоклаве, может вторично перерабатываться и имеет отличные барьерные свойства. Другой способ нанесения покрытия разработан в Швейцарии Лоусоном Мардоном (.Lawson Mardon) — в нем используется предварительная плазменная обработка с последующим напылением диоксида кремния электронным пучком [8].
SiO -покрытие наносят также на пластиковые бутылки, что обеспечивает им 20-кратное улучшение барьерных свойств по отношению к кислороду [9]. По технологии Glaskin фирмы Tetrapak используется вакуумное нанесение покрытия изнутри ПЭТ-бутылок для пива. Бутылки с таким покрытием используют несколько ведущих европейских пивоваренных предприятий [2,3]. Отмечается, что при минимальном сроке годности 6 мес. происходит гораздо меньше потерь вкуса и аромата.
Вопросы применение в Европе термических способов нанесения оксида кремния, химического осаждения его в газовой фазе с помощью электронного пучка, а также реактивное напыление алюминия рассмотрены в работе [10].
7.4.8. DLC-покрытие
Относительно новое «алмазоподобное» покрытие обозначают DLC (DiamondLike Coating). Состоит оно из очень тонкого слоя углерода. ПЭТ-бутылки для пива не обеспечивают такого же долгого срока годности напитка, как стеклянные, и DLC-покрытие внутренней стороны ПЭТ-бутылок широко использовалось в Японии со значительным улучшением барьерных свойств [1,4].
7.4.9. Экструзионное ПЭ-покрытие
На термостойкие ПЭТ- и П А-пленки можно наносить термосвариваемое ПЭ-покрытие (рис. 7.14).
Рис. 7.14. Нанесение экструзионного покрытия на полимерную пленку |
www.chinkopack.ru