Как производят ламинированную фанеру — Как сделать самому? Пленка для ламинирования фанеры
Как ламинировать фанеру
Фанера — это универсальный материал, который можно использовать для решения многих строительных задач. Изготавливают такие продукты из нескольких тонких листов дерева, пропитанные специальными веществами, которые и придают изделию прочность.
Сегодня, чтобы придать красивый внешний вид или защитить фанеру от воздействия влаги, используют ламинирование. Более подробно об этом можно узнать на специализированных сайтах, а также здесь вы сможете приобрести необходимый материал.
Основные понятия
Фанера является слоистым строительным материалом, состоящего из нескольких слоев шпона.
Практически все виды таких продуктов стойкие к воздействию влаги. Это достигается специальными пропитками, которые наносятся на поверхность дерева.
На рынке сегодня можно найти несколько видов пленок, которые подойдут для ламинирования фанеры. Среди них следует выделить:
- Меламиновые изделия. Обладают высокой стойкостью к воздействию влаги и стиранию. Очень часто используются для защиты деревянных покрытий. В состав входят различные виды формальдегидных смол, которые вредны для здоровья человека.
- ПВХ пленки хорошо отталкивают влагу. Рекомендовано использовать только внутри помещений.
- Фенольные продукты не так сопротивляются влаге, как предыдущий вариант, но могут использоваться для защиты изделий из фанеры.
Ламинируем поверхность
Следует сказать, что при нагревании большинство видов пленок выделяют вредные вещества. Поэтому работать с ними нужно в специальном респираторе и в хорошо вентилируемом помещении.
Процесс ламинирования фанеры можно разбить на несколько этапов:
- Для того, чтобы пленка приклеилась к основанию, ее следует предварительно нагреть. Сделать это можно с помощью фена. При этом желательно не перестараться, так как этом может быть причиной появления пузырьков.
- Когда пленка нагрелась, прикладываем ее к листу фанеры и разглаживаем ее постепенно по всей поверхности. Для этого следует использовать ветошь, которой удаляют воздух из-под наносимого материала.Когда внутри покрытия образовался пузырь, его можно проткнуть чем-то острым, а место снова нагреть и разгладить, чтобы получить ровную поверхность.
Процесс ламинирования довольно сложен и требует специальных навыков. Оптимальным вариантом будет приобретение готового изделия, которые будет выполнено качественно и без изъянов.
Смотрите также:
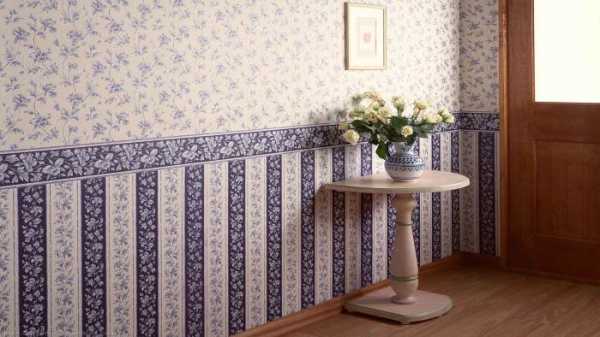
Технические характеристики труб ВГП http://domkrat.org/tehnicheskie-harakteristiki-trub-vgp/.
Интересное по теме: Качественные насосы
Советы в статье "Как выбрать стабилизатор напряжения " здесь.
В этом ролике можно наглядно увидеть, как ламинируется фанера в производственных условиях:
Tweetdomkrat.org
Производство ламинированной фанеры | ООО «Компания Альфа»
Технологии
Технология производства ламинированной фанеры может быть условно разделена на два этапа
- производство ФСФ как таковой;
- ламинирование фанеры.
Производство фанеры ФСФ
Изготовление клееной фанеры - процесс достаточно простой, если не вдаваться в детали, и чрезвычайно сложный, если вдаваться. Мы постараемся описать его в общих чертах.
Фанеру изготавливают из лущеного шпона, который в свою очередь получают из отрезков древесных стволов (чураков). Чураки распаривают в горячей воде до размягчения лигнина и затем помещают в лущильный станок. Лущильный нож срезает с вращающегося чурака тонкую ленту шпона, который затем выпрямляют, раскраивают и высушивают.
Полученный шпон склеивают клеевым составом на основе смол. Для изготовления фанеры ФСФ, которая идет на ламинирование, используют фенолформальдегидные смолы. Такие смолы представляют собой продукт поликонденсации фенола и формальдегида. Фанерные комбинаты обычно не имеют собственного производства смол и закупают их у химических компаний.
Итак, клеевой состав на основе смол наносится на листы шпона, которые укладываются друг на друга и затем помещаются в пресс. В прессе под воздействием высокой температуры и давления листы шпона склеиваются, и получается многослойная древесная плита.
Существенный момент: шпон укладывается в стопку не как попало, а с учетом направления волокон. Обычно фанера состоит из нечетного числа слоев шпона. Центральный лист укладывается вдоль условной оси, две следующих по обе стороны от него - волокнами поперек оси, следующие - опять перпендикулярно соседним. Такое расположение необходимо для достижения максимальной прочности на разрыв во всех направлениях и компенсации внутренних напряжений. И то, и другое чрезвычайно важно для ламинированной фанеры, которая обычно используется в опалубке и принимает на себя большую нагрузку.
Склеенная фанера извлекается из пресса, охлаждается, маркируется и упаковывается.
Ламинирование
Наибольшее распространение получило ламинирование фанеры фенолформальдегидной и меламиновой пленками. Меламиновая пленка имеет меньшую влагостойкость, но при комнатной температуре не выделяет фенол и другие вредные вещества. Фенолформальдегидные смолы постепенно разрушаются, выделяя и фенол, и формальдегидные соединения, но такая пленка имеет очень высокую влагостойкость.
Разница в свойствах определяет разницу в применении: фанера, ламинированная фенолформальдегидной пленкой, используется для опалубки, а фанера с меламиновым покрытием - как материал для отделки и производства мебели (если речь идет о фанере ФК или ФКМ).
Ламинат, наносимый на фанеру, представляет собой лист плотной бумаги, пропитанной соответствующим составом. Поверхность фанерного листа промазывается клеем (те же фенолформальдегидные или меламиноформальдегидные смолы), после чего на нее накладывается пленка. Затем лист помещается в горячий пресс, где ламинат полностью спрессовывается со шпоном, образуя единое целое.
Слой ламината является надежным барьером, защищающим древесные волокна от влаги, однако она может проникнуть чрез незащищенные торцы. Торцы опалубочной фанеры покрывают фенолформальдегидной смолой, которая не пропускает воду. Мебельная ламинированная фанера впоследствии все равно раскраивается, а потому ее торцы ничем не покрывают.
oooalfa.ru
Как ламинировать фанеру
Фанера — это универсальный материал, который можно использовать для решения многих строительных задач. Изготавливают такие продукты из нескольких тонких листов дерева, пропитанные специальными веществами, которые и придают изделию прочность.
Сегодня, чтобы придать красивый внешний вид или защитить фанеру от воздействия влаги, используют ламинирование. Более подробно об этом можно узнать на специализированных сайтах, а также здесь вы сможете приобрести необходимый материал.
Основные понятия
Фанера является слоистым строительным материалом, состоящего из нескольких слоев шпона.
Практически все виды таких продуктов стойкие к воздействию влаги. Это достигается специальными пропитками, которые наносятся на поверхность дерева.
На рынке сегодня можно найти несколько видов пленок, которые подойдут для ламинирования фанеры. Среди них следует выделить:
- Меламиновые изделия. Обладают высокой стойкостью к воздействию влаги и стиранию. Очень часто используются для защиты деревянных покрытий. В состав входят различные виды формальдегидных смол, которые вредны для здоровья человека.
- ПВХ пленки хорошо отталкивают влагу. Рекомендовано использовать только внутри помещений.
- Фенольные продукты не так сопротивляются влаге, как предыдущий вариант, но могут использоваться для защиты изделий из фанеры.
Ламинируем поверхность
Следует сказать, что при нагревании большинство видов пленок выделяют вредные вещества. Поэтому работать с ними нужно в специальном респираторе и в хорошо вентилируемом помещении.
Процесс ламинирования фанеры можно разбить на несколько этапов:
- Для того, чтобы пленка приклеилась к основанию, ее следует предварительно нагреть. Сделать это можно с помощью фена. При этом желательно не перестараться, так как этом может быть причиной появления пузырьков.
- Когда пленка нагрелась, прикладываем ее к листу фанеры и разглаживаем ее постепенно по всей поверхности. Для этого следует использовать ветошь, которой удаляют воздух из-под наносимого материала.Когда внутри покрытия образовался пузырь, его можно проткнуть чем-то острым, а место снова нагреть и разгладить, чтобы получить ровную поверхность.
Процесс ламинирования довольно сложен и требует специальных навыков. Оптимальным вариантом будет приобретение готового изделия, которые будет выполнено качественно и без изъянов.
Смотрите также:
Технические характеристики труб ВГП /tehnicheskie-harakteristiki-trub-vgp/.
Интересное по теме: Качественные насосы
Советы в статье «Как выбрать стабилизатор напряжения » здесь.
В этом ролике можно наглядно увидеть, как ламинируется фанера в производственных условиях:
Не забудь поделиться с друзьями: Загрузка...u-news.org.ua
Как производят ламинированную фанеру
В связи с развитием монолитного строительства особое значение для качества возводимых конструкций приобретают опалубочные системы. В состав опалубки входят металлический каркас и ламинированная фанера. Качественная ламинированная фанера имеет гладкую, ровную поверхность и хорошо прокрашенные, защищенные от влаги торцы. Именно эти свойства позволяют использовать ее многократно.
Первые станки для переработки древесины в шпон, а далее – в фанеру, были запатентованы еще в XVIII веке. Примечательно, что практически все их изобретатели так или иначе связаны с Россией.
NOTA BENE
Первую модель лущильного станка в конце XVII создал инженер-механик Сэмюэль Бентам, ранее служивший Екатерине II по приглашению князя Потемкина. По окончании 10-летней службы в России Бентам вернулся в Англию и получил патенты сразу на несколько своих изобретений. Впрочем, изобретенный англичанином станок не был замечен производителями тех времен.
Действительно эффективный прототип всех современных лущильных станков создал шведский инженер-изобретатель Эммануэль Нобель, отец Альфреда Нобеля, основателя Нобелевской премии. Созданная им в конце XVIII века модель ротационного (поворотного) токарного станка позволяла снимать с деревянного чурака шпон определенной и постоянной толщины, благодаря чему фанерный «сэндвич» становился однородным по структуре и толщине.
Эммануэль Нобель жил и работал в России с 1838 по 1859 год, созданные им в этот период изобретения предназначались для военной промышленности и высоко ценились императором Николаем I.
В начале XIX века русский промышленник Дитрих Мартин Лютер, владевший мануфактурой по производству карандашей в эстонском Ревеле (современный Таллинн), изобрел свой лущильный станок – более крупную версию станка для производства карандашей. Он получил патент на свое изобретение в 1819 году.
Первая фанера, производство которой основывалось на станке Дитриха Мартина Лютера, была создана эстонским мебельщиком Александром Лютером, его однофамильцем. В конце XIX века он решил использовать склеенные между собой листы шпона в качестве сидений для венских стульев – мебель получилась легкой, прочной и недорогой, благодаря чему на нее возник устойчивый спрос.
Практически одновременно с мебельщиком Лютером фанера была создана русским изобретателем — Огнеславом Степановичем Костовичем, занимавшимся созданием летательных аппаратов и остро нуждавшимся в конструкционном материале для их постройки. В 1881 году он изобрел арборит – материал, состоящий из склеенных между собой поперек волокон листов шпона. Лущильный станок и клей для производства фанеры-арборита Костович также изобрел самостоятельно, причем его фанера обладала высокой устойчивостью к воздействию влаги и была не подвержена гниению.
С момента изобретения сама технология переработки практически не изменилась. Модернизации подверглось управление станками, сейчас оно полностью автоматизировано. Это позволило сократить долю ручного труда в производстве, и, как следствие, повысить качество конечного продукта – фанеры.
Начало: подготовка сырья
Процесс производства ламинированной березовой фанеры требует тщательного отбора и подготовки сырья. В первую очередь подбираются стволы нужного размера. Для производства стандартной для России фанеры (1220х2440 мм) перерабатываются стволы диаметром 20–40 см и длиной 5,2 м (в дальнейшем такие стволы можно распилить на чураки по 1,3 или 2,6 м, необходимые для производства продольного и поперечного шпона требуемого формата).
Складирование сырья для производства фанеры.
Основным этапом подготовки является проварка сырья. Она осуществляется в специальном бассейне (открытом или закрытом) в течение 24 часов. Летом температура в бассейне держится на уровне 35–40°С, а зимой – 40–45°С. Для повышения качества шпона, из которого впоследствии будет изготовлена фанера, важно, чтобы на этапе проварки соблюдались термический режим и время обработки древесины.
Проваренный фанерный кряж подается в отделение по окорке и распиловке.
Окорка осуществляется следующим образом: специальные ножи окорочного станка надрезают кору и снимают ее лентами по спирали. Снятая кора используется как для отопления самого комбината, так и соседних зданий или даже целого поселка. Так происходит, например, на Пермском фанерном комбинате (группа «Свеза»). Котельная предприятия обслуживает и комбинат, и поселок Уральский, в котором расположено предприятие.
Проварка сырья в открытом бассейне.
Окоренный кряж (практически без коры) проходит через металлодетектор. Он помогает обнаружить металлические включения в древесине: гвозди, остатки проволоки и т. п., которые могут испортить оборудование. При обнаружении металла на пульт управления станка поступает сигнал, процесс останавливается, и металл удаляется оператором.
После окорки выполняется распиловка. Обработанное сырье пилится на чураки для производства продольного и поперечного шпона.
Производство и обработка шпоная
Следующий этап – лущение шпона на специальных станках, где с подготовленного чурака срезается непрерывная тонкая лента шпона. Чем тоньше шпон, тем больше слоев будет в фанере определенной толщины. Чем больше слоев, тем прочнее фанера. Шпон из российской березы – самый тонкий (1,2–1,5 мм) по сравнению с другими породами древесины (например, толщина шпона из тополя 1,6–2,6 мм, а хвойного шпона – 2–4 мм).
На этапе лущения осуществляется контроль качества шпона: ежедневно отбираются образцы для проверки толщины и еще ряда параметров, а полученные результаты сравниваются с нормативными. С учетом этих данных производится настройка лущильных станков.
Лущильная линия.
После лущения лента шпона подается на автоматические ножницы, где происходит рубка на форматные листы шпона размером 1,3х2,6 м для производства фанеры формата 1220х2440 мм. Продольный и поперечный шпон (для последующего склеивания в одном листе фанеры) производится на отдельных лущильных линиях.
Разрезанный на форматные листы шпон поступает в сушилку.
«Находясь в сушилке, листы шпона обдуваются горячим воздухом. За 8–10 минут из древесины уходит до 90% влаги. На выходе из сушилки листы шпона укладываются на поддон или попадают на транспортер (в зависимости от конструкции сушилки)», – комментирует Наталья Андреева, инженер-технолог производства ламинированной фанеры комбината «Фанплит», входящего в состав группы «Свеза».
После просушки шпон сортируется по целому ряду параметров, в том числе на наличие выпавших сучков, трещин и т. п. На многих комбинатах на этом этапе используется автоматизированное оборудование: параметры сортов заложены в компьютерную программу, управляющую процессом. При сортировке происходит сканирование поверхности и ее автоматическая оценка, после которой сканер сам управляет раскладкой шпона по стопам. Оператор в данном случае лишь наблюдает за процессом. На этом же этапе оценивается влажность листов. Если шпон оказался недосушенным, он откладывается в отдельную стопу и досушивается позже.
Если на этапе сортировки выявляются дефекты, то листы не утилизируются, а отправляются на починку. Починка шпона может осуществляться как на ручных станках, так и на оборудовании с автоматическим управлением. Автоматические станки позволяют повысить качество фанеры, сократив затраты ручного труда в три раза. Сейчас существует оборудование для починки шпона любых форматов: как стандартного – 5х5 футов (1525х1525 мм), так и большого – 5х10 футов (1500/1525х3000/3050 мм). После починки вновь происходит сортировка шпона.
Комплектование фанеры
Для получения готовой фанеры необходимо склеить несколько листов шпона между собой. Волокна в последовательных слоях шпона располагаются перпендикулярно друг другу, что придает прочность готовому продукту. Полученные листы оказываются стойкими к деформации в любых направлениях. Эта особенность определяет применимость фанеры в опалубочных системах для монолитного строительства.
При производстве березовой фанеры склеивается нечетное количество листов шпона в фанеру толщиной от 3 до 40 мм. Между собой листы склеиваются при помощи клея, который изготавливают здесь же, в специальном смесителе. Он состоит из мела, воды, смолы, а также древесной или ржаной муки. Важно строгое соблюдение технологии производства клея, чтобы не произошло расклеивание слоев фанеры. На современных предприятиях установлено оборудование, которое автоматически контролирует пропорции ингредиентов в соответствии с рецептурой.
Склейка листов шпона.
На следующем этапе, вальцовке, лист шпона пропускается между двумя валиками, смазанными клеем. Клей равномерно распределяется по обеим поверхностям листа, после чего эти листы отправляются в наборку.
«В стопе наборного пакета сухой шпон чередуется со шпоном, намазанным клеем. Количество чередующихся листов зависит от толщины фанеры. В конце процесса комплектования одного листа фанеры автомат подает два листа сухого шпона (последний лист предыдущего «сэндвича» и первый следующего), что позволит позже отделить один лист фанеры от другого. Подготовленная таким образом стопа отправляется на подпрессовку», – комментирует Елена Вершинина, начальник службы качества Пермского фанерного комбината, входящего в состав группы «Свеза».
Холодная подпрессовка пакетов собранного шпона производится непосредственно перед горячим прессованием с целью получения цельных пакетов, удобных для транспортирования и загрузки в горячий пресс. Время холодной подпрессовки составляет 5–10 минут при давлении 1–1,5 МПа.
После этого осуществляется загрузка предварительно склеенных листов в этажерку горячего пресса для окончательного приклеивания при температуре 120–130°С и давлении 1,2–1,8 МПа.
После прессования склеенные листы обрезаются с четырех сторон под формат, требуемый заказчиком: к примеру, 1250х2500 мм или 1220х2440 мм с точностью до 3 мм. При производстве ламинированной фанеры станок выполняет предварительную обрезку до размера 1290х2550 мм, чтобы после нанесения пленки лист можно было еще раз подровнять, срезав оставшиеся миллиметры.
Далее выполняется шлифование на станке для придания фанере гладкой поверхности и выравнивания ее по толщине. Фанера последовательно проходит через шлифовальные ленты с разной зернистостью. После этого фанеру снова классифицируют по внешнему виду: качество листов оценивает оператор.
Завершение: ламинирование поверхности
На заключительном этапе на лист фанеры с двух сторон наносится пленка. Затем фанера загружается в многопролетный пресс, в котором одновременно могут находиться 15–18 листов продукции. Прессование, в процессе которого пленка схватывается с поверхностью плиты, осуществляется в течение 4,5–10 минут при температуре 130–136оС. Время прессования зависит от плотности пленки, толщины фанеры и вида покрытия (гладкая или сетчатая). За счет пленки фанера приобретает дополнительную защиту от воды, механических повреждений, агрессивных сред. Так, из обычной «белой» фанеры получается фанера с покрытием, или ламинированная.
Помимо глянцевой пленки, на ламинированную фанеру может наноситься сетчатое покрытие, обладающее антискользящим эффектом. Такая фанера востребована в транспортном машиностроении: она применяется в полах трейлеров и легких коммерческих автомобилей. А также в качестве настилов в строительных лесах на стройплощадках.
Линия ламинирования.
Далее ламинированная фанера попадает на линию обрезки, где обрезается по формату.
После этого готовую продукцию сортируют по внешнему виду и геометрическим параметрам и укладывают в пачки. По завершении сортировки пачки фанеры подаются в покрасочную камеру. Здесь на торцы плиты наносится специальная водоэмульсионная краска на акриловой основе. Такое покрытие защищает фанеру от попадания влаги и разбухания.
Чем лучше прокрашены торцы, тем лучше влагозащитные свойства плиты, а значит, больше циклов заливки бетона фанера сможет выдержать. Особенно это важно для опалубки перекрытий, где фанера подвергается сильным механическим нагрузкам и воздействию агрессивной среды – бетонной смеси.
Если ламинированная фанера хорошо склеена внутри, имеет ровную поверхность, которая покрыта износостойкой пленкой, и защищенные от влаги торцы, она будет дольше сохранять свою форму. А это значит, что даже при многократном применении одного и того же листа фанеры (не менее 15–20 циклов) качество монолитных перекрытий будет неизменным.
«Ламинированная фанера особенно востребована в монолитном строительстве. Ее популярность объясняется механическими свойствами: только березовая фанера, благодаря высокой прочности и упругости, способна выдерживать нагрузки, воздействующие на опалубку в процессе бетонирования», – комментирует Наталья Андреева (группа «Свеза»).
Как мы увидели, процесс производства ламинированной фанеры довольно сложен. И качество конечного продукта зависит от четкого соблюдения технологии на каждом этапе его производства.
Если использовать фанеру ненадлежащего качества, то поверхность стен и перекрытий здания будет неудовлетворительной. Это приведет к росту трудозатрат на отделочные работы. Поэтому качество фанеры – это не только красота и надежность зданий, в которых мы живем и работаем, но и экономика рационального строительства.
library.stroit.ru
Как производят ламинированную фанеру — Как сделать самому?
В связи с развитием монолитного строительства особое значение для качества возводимых конструкций приобретают опалубочные системы. В состав опалубки входят металлический каркас и ламинированная фанера. Качественная ламинированная фанера имеет гладкую, ровную поверхность и хорошо прокрашенные, защищенные от влаги торцы. Именно эти свойства позволяют использовать ее многократно.
Производство ламинированной фанеры — сложный многоступенчатый процесс, на каждом этапе которого важна точность соблюдения производственных методик. Рассмотрим процесс производства ламинированной фанеры на примере комбинатов группы «СВЕЗА», мирового лидера в производстве берёзовой фанеры.
Первые станки для переработки древесины в шпон, а далее — в фанеру, были запатентованы ещё в XVIII веке. Примечательно, что практически все их изобретатели так или иначе связаны с Россиейi. С момента изобретения сама технология переработки практически не изменилась. Модернизации подверглось управление станками, сейчас оно полностью автоматизировано. Это позволило сократить долю ручного труда в производстве, и, как следствие, повысить качество конечного продукта — фанеры.
Начало: подготовка сырья
Процесс производства ламинированной берёзовой фанеры требует тщательного отбора и подготовки сырья. В первую очередь подбираются стволы нужного размера. Для производства стандартной для России фанеры (1220х2440 мм) перерабатываются стволы диаметром 20-40 см и длиной 5,2 м (в дальнейшем такие стволы можно распилить на чураки по 1,3 или 2,6 м, необходимые для производства продольного и поперечного шпона требуемого формата).
Складирование сырьяПроварка сырья в открытом бассейне
Основным этапом подготовки является проварка сырья. Она осуществляется в специальном бассейне (открытом или закрытом) в течение 24 часов. Летом температура в бассейне держится на уровне 35-40оС, а зимой — 40-45оС. Для повышения качества шпона, из которого впоследствии будет изготовлена фанера, важно, чтобы на этапе проварки соблюдались термический режим и время обработки древесины.
Проваренный фанерный кряж подаётся в отделение по окорке и распиловке.
Окорка осуществляется следующим образом: специальные ножи окорочного станка надрезают кору и снимают её лентами по спирали. Снятая кора используется как для отопления самого комбината, так и соседних зданий или даже целого посёлка. Так происходит, например, на Пермском фанерном комбинате (группа «СВЕЗА»). Котельная предприятия обслуживает и комбинат, и посёлок Уральский, в котором расположено предприятие.
Окорённый кряж (практически без коры) проходит через металлодетектор. Он помогает обнаружить металлические включения в древесине: гвозди, остатки проволоки и т. п., которые могут испортить оборудование. При обнаружении металла на пульт управления станка поступает сигнал, процесс останавливается, и металл удаляется оператором.
После окорки выполняется распиловка. Обработанное сырьё пилится на чураки для производства продольного и поперечного шпона.
Производство и обработка шпона
Лущильная линияСледующий этап — лущение шпона на специальных станках, где с подготовленного чурака срезается непрерывная тонкая лента шпона. Чем тоньше шпон, тем больше слоёв будет в фанере определённой толщины. Чем больше слоёв, тем прочнее фанера. Шпон из российской берёзы — самый тонкий (1,2-1,5 мм) по сравнению с другими породами древесины (например, толщина шпона из тополя 1,6-2,6 мм, а хвойного шпона — 2-4 мм).
На этапе лущения осуществляется контроль качества шпона: ежедневно отбираются образцы для проверки толщины и ещё ряда параметров, а полученные результаты сравниваются с нормативными. С учётом этих данных производится настройка лущильных станков.
После лущения лента шпона подаётся на автоматические ножницы, где происходит рубка на форматные листы шпона размером 1,3х2,6 м для производства фанеры формата 1220х2440 мм. Продольный и поперечный шпон (для последующего склеивания в одном листе фанеры) производится на отдельных лущильных линиях.
Разрезанный на форматные листы шпон поступает в сушилку.
«Находясь в сушилке, листы шпона обдуваются горячим воздухом. За 8-10 минут из древесины уходит до 90% влаги. На выходе из сушилки листы шпона укладываются на поддон или попадают на транспортёр (в зависимости от конструкции сушилки)», — комментирует Наталья Андреева, инженер-технолог производства ламинированной фанеры комбината «Фанплит», входящего в состав группы «СВЕЗА».
После просушки шпон сортируется по целому ряду параметров, в том числе на наличие выпавших сучков, трещин и т. п. На многих комбинатах на этом этапе используется автоматизированное оборудование: параметры сортов заложены в компьютерную программу, управляющую процессом. При сортировке происходит сканирование поверхности и её автоматическая оценка, после которой сканер сам управляет раскладкой шпона по стопам. Оператор в данном случае лишь наблюдает за процессом. На этом же этапе оценивается влажность листов. Если шпон оказался недосушенным, он откладывается в отдельную стопу и досушивается позже.
Если на этапе сортировки выявляются дефекты, то листы не утилизируются, а отправляются на починку. Починка шпона может осуществляться как на ручных станках, так и на оборудовании с автоматическим управлением. Автоматические станки позволяют повысить качество фанеры, сократив затраты ручного труда в 3 раза. Сейчас существует оборудование для починки шпона любых форматов: как стандартного — 5х5 футов (1525х1525 мм), так и большого — 5х10 футов (1500/1525х3000/3050 мм). После починки вновь происходит сортировка шпона.
Комплектование фанеры
Для получения готовой фанеры необходимо склеить несколько листов шпона между собой. Волокна в последовательных слоях шпона располагаются перпендикулярно друг другу, что придаёт прочность готовому продукту. Полученные листы оказываются стойкими к деформации в любых направлениях. Эта особенность определяет применимость фанеры в опалубочных системах для монолитного строительства.
Склейка листов шпонаПри производстве берёзовой фанеры склеивается нечётное количество листов шпона в фанеру толщиной от 3 до 40 мм. Между собой листы склеиваются при помощи клея, который изготавливают здесь же, в специальном смесителе. Он состоит из мела, воды, смолы, а также древесной или ржаной муки. Важно строгое соблюдение технологии производства клея, чтобы не произошло расклеивание слоёв фанеры. На современных предприятиях установлено оборудование, которое автоматически контролирует пропорции ингредиентов в соответствии с рецептурой.
На следующем этапе, вальцовке, лист шпона пропускается между двумя валиками, смазанными клеем. Клей равномерно распределяется по обеим поверхностям листа, после чего эти листы отправляются в наборку.«В стопе наборного пакета сухой шпон чередуется со шпоном, намазанным клеем. Количество чередующихся листов зависит от толщины фанеры. В конце процесса комплектования одного листа фанеры автомат подаёт 2 листа сухого шпона (последний лист предыдущего «сэндвича» и первый следующего), что позволит позже отделить один лист фанеры от другого. Подготовленная таким образом стопа отправляется на подпрессовку», — комментирует Елена Вершинина, начальник службы качества Пермского фанерного комбината, входящего в состав группы «СВЕЗА».
Холодная подпрессовка пакетов собранного шпона производится непосредственно перед горячим прессованием с целью получения цельных пакетов, удобных для транспортирования и загрузки в горячий пресс. Время холодной подпрессовки составляет 5-10 минут при давлении 1-1,5 МПа.
После этого осуществляется загрузка предварительно склеенных листов в этажерку горячего пресса для окончательного приклеивания при температуре 120-130оС и давлении 1,2-1,8 МПа.
После прессования склеенные листы обрезаются с четырёх сторон под формат, требуемый заказчиком: к примеру, 1250х2500 мм или 1220х2440 мм с точностью до 3 мм. При производстве ламинированной фанеры станок выполняет предварительную обрезку до размера 1290х2550 мм, чтобы после нанесения плёнки лист можно было ещё раз подровнять, срезав оставшиеся миллиметры.
Далее выполняется шлифование на станке для придания фанере гладкой поверхности и выравнивания её по толщине. Фанера последовательно проходит через шлифовальные ленты с разной зернистостью. После этого фанеру снова классифицируют по внешнему виду: качество листов оценивает оператор.
Завершение: ламинирование поверхности
На заключительном этапе на лист фанеры с двух сторон наносится плёнка. Затем фанера загружается в многопролётный пресс, в котором одновременно могут находиться 15-18 листов продукции. Прессование, в процессе которого пленка схватывается с поверхностью плиты, осуществляется в течение 4,5-10 минут при температуре 130-136оС. Время прессования зависит от плотности плёнки, толщины фанеры и вида покрытия (гладкая или сетчатая). За счёт пленки фанера приобретает дополнительную защиту от воды, механических повреждений, агрессивных сред. Так, из обычной «белой» фанеры получается фанера с покрытием, или ламинированная.
Линия ламинированияПомимо глянцевой плёнки, на ламинированную фанеру может наноситься сетчатое покрытие, обладающее антискользящим эффектом. Такая фанера востребована в транспортном машиностроении: она применяется в полах трейлеров и лёгких коммерческих автомобилей. А также в качестве настилов в строительных лесах на стройплощадках.
Далее ламинированная фанера попадает на линию обрезки, где обрезается по формату.
После этого готовую продукцию сортируют по внешнему виду и геометрическим параметрам и укладывают в пачки. По завершении сортировки пачки фанеры подаются в покрасочную камеру. Здесь на торцы плиты наносится специальная водоэмульсионная краска на акриловой основе. Такое покрытие защищает фанеру от попадания влаги и разбухания.
Чем лучше прокрашены торцы, тем лучше влагозащитные свойства плиты, а значит, больше циклов заливки бетона фанера сможет выдержать. Особенно это важно для опалубки перекрытий, где фанера подвергается сильным механическим нагрузкам и воздействию агрессивной среды — бетонной смеси.
Если ламинированная фанера хорошо склеена внутри, имеет ровную поверхность, которая покрыта износостойкой плёнкой, и защищённые от влаги торцы, она будет дольше сохранять свою форму. А это значит, что даже при многократном применении одного и того же листа фанеры (не менее 15-20 циклов) качество монолитных перекрытий будет неизменным.
«Ламинированная фанера особенно востребована в монолитном строительстве. Её популярность объясняется механическими свойствами: только берёзовая фанера, благодаря высокой прочности и упругости, способна выдерживать нагрузки, воздействующие на опалубку в процессе бетонирования», — комментирует Наталья Андреева (группа «СВЕЗА»).
Как мы увидели, процесс производства ламинированной фанеры довольно сложен. И качество конечного продукта зависит от чёткого соблюдения технологии на каждом этапе его производства.
Если использовать фанеру ненадлежащего качества, то поверхность стен и перекрытий здания будет неудовлетворительной. Это приведёт к росту трудозатрат на отделочные работы. Поэтому качество фанеры — это не только красота и надёжность зданий, в которых мы живём и работаем, но и экономика рационального строительства.
remont-doma24.ru
инструкция по применению, цвета и технические характеристики, фото
Среди разнообразия строительных материалов традиционной популярностью пользуется обычная фанера, которая отличается великолепными эксплуатационными свойствами, что позволяет использовать ее в различных сферах человеческой жизнедеятельности. В данной статье мы расскажем о таком материале, как ламинированная фанера для пола, а также о том, какие еще разновидности данного материала встречаются.
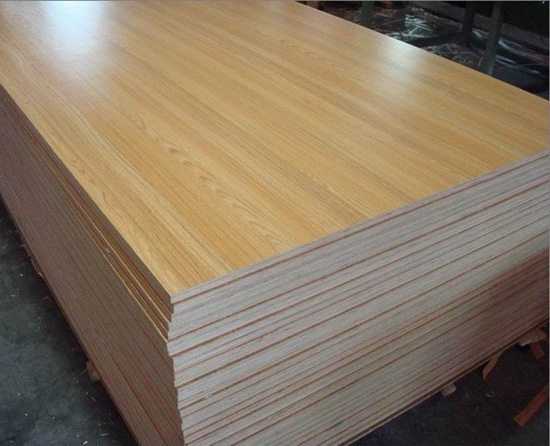
Фанера ламинированного типа
Особенности производства
Для производства описываемого материала используются те же породы дерева, что и для производства обычной фанеры.
В частности, речь идет о таких видах, как:
- береза;
- тополь;
- хвойные деревья;
- осина и другие.
Повышенные эксплуатационные свойства достигаются благодаря ламинированию, в результате которого фанера приобретает следующие характеристики:
- высокую плотность;
- повышенную прочность;
- устойчивость к механическим повреждениям;
- повышенный уровень влагостойкости.
Как выполняется ламинирование
Для того чтобы выполнить ламинирование, производители используют определенные составы.
Среди них:
- меламин;
- фенол;
- поливинилхлорид.
Меламин представляет собой специальный, уникальный материал, в состав которого входят особые смолы меламиноформальдегидного типа. Использование меламина позволяет создать фанеру, характеризующуюся повышенной влагоустойчивостью, а также высоким уровнем износостойкости.
Фенол являет собой удивительное соединение химического типа, которое присутствует практически во всех смолах органического типа. Если применять для обработки поверхности только феноловую смолу, то это не позволит повысить уровень влагостойкости.
Обратите внимание!Производители чаще берут фенол в качестве основы фенолформальдегидного состава, который позволяет создать материал высочайшего уровне влагостойкости, благодаря чему такая фанера используется при обустройстве опалубки.
Последний вид составов, которым является поливинилхлорид – это наиболее распространенный вариант обработки фанеры при ее ламинировании.
Главные характеристики данного состава:
- низкая химическая активность;
- высокий уровень экологичности.
Потому фанеру, обработанную таким видом покрытия, применяют при внутренней отделки помещения, а также при создании мебели.
Стандарты качества
Существует даже специальный ГОСТ на ламинированную фанера — 53920-2010 «Фанера облицованная. Технические условия». Если говорить о дате появления данного ГОСТа, то, в сравнении с прочими техническими условиями, он появился относительно недавно, а потому многие специалисты в области строительства и выполнения ремонтных работ даже не подозревают о его существовании.
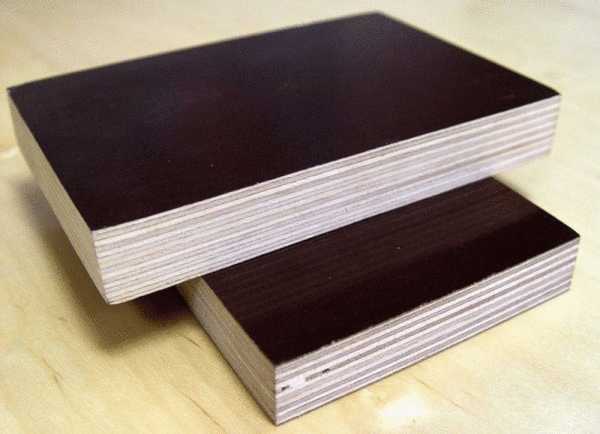
Фото фанеры темного цвета
Поэтому рассмотрим данный документ более подробно.
В частности, его применяют к продукции:
- повышенной влагостойкости;
- облицованной полимерной пленкой или особыми смолами полимерного типа.
Данный документ предусматривает наличие нескольких марок ламинированной фанеры:
- FF – подразумевается материал, который с обеих сторон проходит облицовку специальной пленкой;
- FW – речь идет о материале, который с одной стороны покрывается гладкой пленкой, а с другой – сеткой;
- SP/SP – материал, используемый под покраску, а потому покрыт особой разновидностью пленки;
- F/SP – материал, который с одно стороны облицовывается пленкой, пригодной под покраску, а с другой обычной гладкой пленкой;
- F/U – материал, который только с одной стороны покрыт гладкой пленкой.
В соответствии с ГОСТом, данная продукция должна обязательно проходить строгую маркировку, которая будет отображать следующую информацию:
- марку фанеры;
- наименование материала;
- габаритные размеры изделия;
- марку пленки, которая применяется при ламинировании;
- класс;
- а также иметь обозначение стандарта, по которому и была изготовлена фанера.
Основные сферы применения
Применение ламинированной фанеры достаточно разнообразно. Это обусловлено тем, что технические характеристики ламинированной фанеры достаточно высоки. Особенно это касается такого вида изделия, как фоф, что говорит о высоком уровне влагостойкости.
Итак, основные сферы применения ламинированной фанеры:
- строительство;
- ремонтные работы, в частности, по отделки помещений;
- производство мебели;
- автомобилестроение и создание различных транспортных средств;
- изготовление торгового и складского оборудования.
Особенности использования в строительстве
Если говорить о строительстве, то в первую очередь стоит отметить создание опалубки.
Обустройство опалубки
Это обусловлено тем, что пленка, которой обработана фанера, позволяет защитить материал от следующих негативных воздействий:
- механических повреждений;
- истирания;
- негативного воздействия влаги;
- негативного воздействия химических составов.
Все это дает возможность применять опалубку, созданную из фанеры, многократно.
Помимо обустройства фундаментов данный тип строительного материала используется в следующих случаях:
- при создании перекрытий и перегородок;
- при возведении колонн;
- при создании ограждений;
- при возведении складских помещений;
- при строительстве мостов и т.д.
Отдельного внимания заслуживает фанера с сеткой WISA-WIRE, цена на которую может слегка отличаться от обычного материала описываемого типа. Суть такой фанеры состоит в том, что она с обеих сторон облицована специальной рифленой поверхностью, препятствующей скольжению.
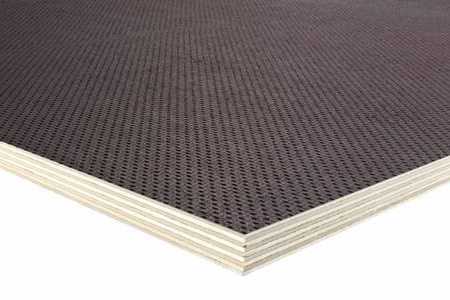
Фанера с сеткой
Есть и другие положительные характеристики у фанеры такого типа, среди которых выделяются следующие:
- дополнительный запас прочности;
- устойчивость к механическому истиранию и повреждениям;
- устойчивость к воздействию влаги;
- устойчивость к химическому воздействию различного типа;
- устойчивость к образованию и распространению плесени, грибка.
Фанера, в которой используется сетка WISA-WIRE, помимо строительства с успехом используется в различных отраслях человеческой жизнедеятельности, например, при создании полов в транспортных средствах любого типа.
Особенности применения при отделочных работах
В данном случае ламинированная продукция используется при создании межкомнатных перегородок, панелей декоративного типа, а также:
- передвижных перегородок;
- подоконников;
- потолков.
Учитывая разнообразие цветовых решений, в помещении можно создать уникальное оформление.
Поэтому фанера с успехом применяется не только в жилых домах, но и в следующих типах зданий:
- офисах;
- общественных зданиях различного типа;
- спортивных и культурных центрах;
- кинозалах и т.д.
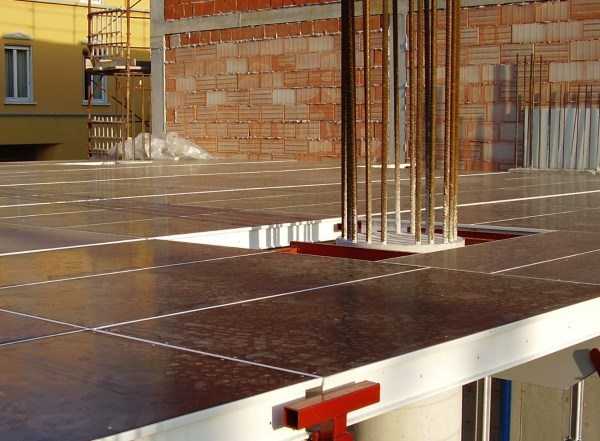
Пол из ламинированной фанеры
Прочие сферы применения
Учитывая повышенные эстетические и декоративные свойства, которые характерны ламинированной фанере, ее принято использовать при производстве мебели.
В частности, из нее делают:
- полки всех типов;
- кухонные гарнитуры;
- шкафы всех типов;
- ящики и многое другое.
А уже повышенные эксплуатационные свойства позволяют применять данный материал в строении различных транспортных средств:
- автомобилей;
- прицепов;
- троллейбусов;
- автобусов;
- судов, в том числе яхт;
- вагонов и т.д.
Обратите внимание!Востребована фанера, в частности цветная, и при создании складского и торгового оборудования, которое подлежит частому мытью.
Например, из нее делают:
- прилавки;
- примерочные кабины;
- рекламные стенды и многое другое.
Эстетические свойства и характеристики
В данном разделе хотелось бы остановиться на различных цветовых решениях данного материала. Даже на фото он выглядит неподражаемо.
Чаще всего покрытие представлено в следующих цветовых решениях:
- коричневом;
- темно-коричневом прозрачного типа;
- темно-коричневый непрозрачного типа;
- каштановый.
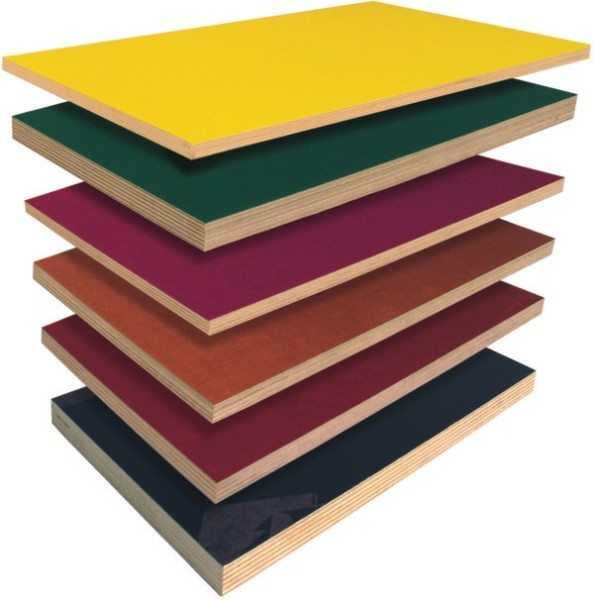
Разноцветный материал
Однако это далеко не все цвета ламинированной фанеры. Их истинное количество великое множество. Конечно же, к примеру, белая отличается своей аристократичностью и может быть использована в любых целях.
Но есть и другие популярные оттенки и цвета:
- черный;
- желтый;
- бордовый;
- лиловый;
- серый и многие другие.
Декоративная фанера распределяется на два основных типа и в своей маркировке может иметь следующие индексы:
- F — гладкая;
- W – тисненая.
Возможно ли выполнить ламинирование самостоятельно
Многих интересует, возможно ли выполнить ламинирование фанеры своими руками. В принципе, сделать это реально.
Вам понадобится:
- пленка для ламинирования фанеры;
- фен;
- определенные навыки работы.
Разложив пленку, ее необходимо прогреть феном, чтобы она плотно приклеилась к поверхности фанеры.
Совет. Чтобы правильно уложить пленку, избежать появления пузырей и прочих дефектов, работать нужно вдвоем.В таком случае вам понадобятся не только навыки и знания, но и слаженность в действиях.
Также отметим, что выполнить данную процедуру своими руками не только сложно, но и потребует временных и финансовых затрат. Специалисты отмечают, что приобрести уже готовый материал намного дешевле.
В завершение
Как видим, ламинированное изделие – великолепный строительный и облицовочный материал с широким спектром применения. Он может быть использован фактически в любой сфере человеческой жизнедеятельности, так или иначе связанной со строительством или производством.
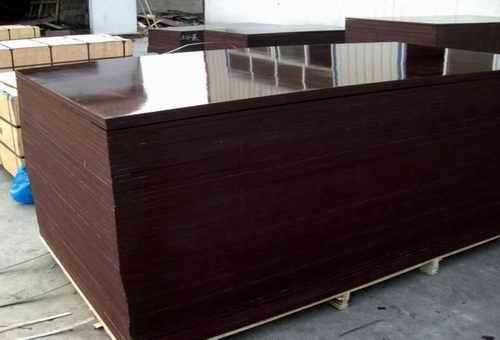
Красивая и качественная фанера
В представленном видео в этой статье вы найдете дополнительную информацию по данной теме.
fanera-info.ru
О фанере в целом и ламинированной фанере в частности
Прежде чем начать рассказ о ламинированной фанере, необходимо рассмотреть, как вообще производится фанера, и когда и где она вообще появилась. Есть сведения, что своим появлением фанера обязана тем странам, где по природно-климатическим условиям были большие проблемы с лесными массивами.
Содержание статьи
Интересно о фанере
В этой связи очень часто вспоминают Египет, где в гробнице Тутанхамона были обнаружены изделия, изготовленные из материалов, отдаленно напоминающих фанеру. В России проблем с лесами не было никогда, и строительству домов из цельных брёвен удивлялись только иностранцы из Западной Европы, где свои леса они вырубили под корень ещё в незапамятные времена, и у которых древесина, особенно хорошая, ценилась буквально на вес золота.
Итак, для строительства нужно было дерево, но использовать цельный брус было нерационально и очень дорого. В результате в XIX веке в Западной Европе (кто бы сомневался!) были проведены первые опыты с получением фанеры ручными и механическими способами. Опыт удался, и с тех пор фанера стала традиционным материалом в строительстве как промышленного, так и жилого назначения.
Технология создания фанеры
В основе процесса изготовления фанеры лежит древесный шпон – обычно берёзовый, хотя, в принципе, годится любая порода дерева. Бревно обрабатывают на строгальных станках, где с него снимают слои толщиной от 0,1 мм и больше. Эти слои собираются в кипы, обрезаются под общий трафарет практически любого размера.
Затем происходит отбраковка тех слоёв, где есть сучки, сколы и т.п. Недостающие части листа вырезаются на стороне и вкладываются в шпон (словно паззлы). После этого слои шпона укладывают так, чтобы направление древесного рисунка чередовалось перпендикулярно от слоя к слою. И уже окончательный процесс – проклейка слоёв клеем и смолами, опрессовка под давлением и сушка.
В итоге получаются листы фанеры, которые по размерам превосходят размеры цельного деревянного массива. При этом листы за счёт воздушной прослойки становятся легче, структура фанеры – прочнее, плюс налицо значительная экономия дерева.
Ламинирование фанеры
С технологиями производства фанеры эксперименты продолжаются постоянно. Несмотря на высокую экологичность материала, он подвержен физическим изменениям при попадании влаги (коробление, расщепление слоёв и так далее и тому подобное).
Мысль заламинировать полученные листы просто лежала на поверхности, и это изобретение сразу же прижилось. Ламинировать фанеру, ясное дело, стали не обычной сварной плёнкой, а смоляной, изготовленной из формальдегидной смолы. Эта плёнка покрывает поверхность фанерного листа с обеих сторон.
Очень часто для ламинирования фанеры применяют специально просмоленную бумагу, но опять-таки смолы для пропитки – на основе формальдегида.
В результате ламинированная фанера стала очень устойчивой не только к изменению влажности, но и вообще к внешним воздействиям. Такой материал очень удобно стало применять при производстве опалубки для заливки бетона, строительства щитовых сооружений, в автомобильной промышленности (для кузовов фургонов), для изготовления полов, стен и много другого. Лёгкость конструкций тоже была оценена по достоинству – стало легко производить монтажные работы, распиловку листов для требований дизайна.
Кстати, о цвете поверхности и фактурах (тиснениях) материала тоже позаботились, так что серые невзрачные листы фанеры – давно уже в прошлом. Цена ламинированной фанеры значительно не увеличилась – фанера была и остаётся одним из самых дешёвых видов строительных материалов, доступных каждому потребителю.
Эксплуатация ламинированной фанеры
Для того, чтобы ламинированная фанера не портилась при эксплуатации, необходимо соблюдать ряд правил.
Самым главным источником проникновения влаги в массив ламинированной фанеры являются незащищенные торцы, которые образуются после распила фанерных листов. Эти торцы перед применением фанеры необходимо обрабатывать краской, желательно акриловой, которая надежно заизолирует все незащищенные части фанерного листа.
Если же фанера имеет конструкционные отверстия, то лучшая их защита – какие-либо силиконовые составы. Если фанера используется в качестве съемной опалубки, то после каждого применения ее следует хорошо очищать и просушивать в естественных условиях. Обработка нагревательными приборами исключается.
Загрузка...
instroymatrem.ru