Кевлар предложили заменить углеродными нанотрубками. Кевларовая пленка
Кевлар предложили заменить углеродными нанотрубками
Пленка из углеродных нанотрубок
Фотография: East China University of Science and Technology
Исследователи из Восточно-Китайского университета науки и технологий разработали способ, который позволяет получать прочные пленки из углеродных нанотрубок. По своей прочности такие пленки несколько превосходят углеволоконные и значительно превосходят кевларовые. Результаты работы китайских ученых опубликованы в журнале Nanoletters, а их краткое изложение приводит издание Chemical & Engineering News. По данным исследователей, новые пленки можно использовать при производстве брони для военных или защиты для спортсменов.
Для изготовления пленки из углеродных нанотрубок ученые использовали метод, аналогичный выдуванию стеклянных изделий. Исследователи горизонтально поместили трубку диаметром 50 миллиметров в горн, в котором поддерживалась температура в 1150-1130 градусов. Через трубку продувался под давлением азот, в поток которого подмешивалась смесь этанола и небольших количеств ферроцена и тиофена. На вдув трубки ученые также подавали углеродные нанотрубки.
Во время продувки через разогретую трубку углеродные нанотрубки становились параллельными друг другу, а на выходе появлялась углеродная трубка. Затем исследователи протягивали ее через серию сдавливающих роликов и наматывали на барабан. При этом ученые выяснили, что чем выше скорость наматывания, тем больше получается прочность пленки. В результате такого способа производства углеродные нанотрубки в пленке располагаются максимально близко друг к другу и параллельно. Это и обеспечивает высокую прочность пленок.
Исследователи провели измерения, по итогам которых выяснилось, что прочность новой пленки составляет 9,6 гигапаскаля. Для сравнения, прочность пленки из углеволокна составляет семь гигапаскалей, а из кевлара — 3,7 гигапаскаля. Кроме того, углеродная пленка получилась в четыре раза более гибкой, чем кевларовая. Она также может растягиваться на восемь процентов от своей изначальной длины по сравнению с двумя процентами у кевлара.
Наконец, получившаяся пленка способна проводить электричество. По мнению ученых, это свойство позволит использовать ее при производстве различных электродов, а также искусственных мышц. В настоящее время для производства пленок используется способ помещения заранее расположенных параллельно друг к другу углеродных нанотрубок в специальные растворы и последующей их опрессовки. По словам китайских исследователей, пленки, изготовленные их методом, получаются гораздо прочнее.
Василий Сычёв
nplus1.ru
кевлар « Домашняя яхт-верфь.
Сайт создан для тех, кто мечтает построить яхту своими руками — яхту своей мечты…
Современное серийное пластиковое судостроение делится на две большие группы: в одной судостроители работают с материалами термопластическими, в другой – с термореактивными. Термопласты (например, такие популярные в судостроении, как АБС и полиэтилен) – это синтетические вещества, отверждаемые при остывании, но легко размягчающиеся и/или плавящиеся при повторном нагревании.
Такие качества позволяют сравнительно легко формовать из них небольшие корпуса при помощи прессов и пуансонов, что делает это производство высокомеханизированным. Термореактивные же синтетические материалы (о которых и пойдет речь в этой статье), чаще всего представляющие собой композицию из связующего и армирующего веществ, после начального отверждения уже не подвержены повторному размягчению или плавлению п
yachtshipyard.wordpress.com
Кевлар предложили заменить углеродными нанотрубками
Для изготовления пленки из углеродных нанотрубок ученые использовали метод, аналогичный выдуванию стеклянных изделий. Исследователи горизонтально поместили трубку диаметром 50 миллиметров в горн, в котором поддерживалась температура в 1150-1130 градусов. Через трубку продувался под давлением азот, в поток которого подмешивалась смесь этанола и небольших количеств ферроцена и тиофена. На вдув трубки ученые также подавали углеродные нанотрубки.
Во время продувки через разогретую трубку углеродные нанотрубки становились параллельными друг другу, а на выходе появлялась углеродная трубка. Затем исследователи протягивали ее через серию сдавливающих роликов и наматывали на барабан. При этом ученые выяснили, что чем выше скорость наматывания, тем больше получается прочность пленки. В результате такого способа производства углеродные нанотрубки в пленке располагаются максимально близко друг к другу и параллельно. Это и обеспечивает высокую прочность пленок.
Исследователи провели измерения, по итогам которых выяснилось, что прочность новой пленки составляет 9,6 гигапаскаля. Для сравнения, прочность пленки из углеволокна составляет семь гигапаскалей, а из кевлара — 3,7 гигапаскаля. Кроме того, углеродная пленка получилась в четыре раза более гибкой, чем кевларовая. Она также может растягиваться на восемь процентов от своей изначальной длины по сравнению с двумя процентами у кевлара.
Наконец, получившаяся пленка способна проводить электричество. По мнению ученых, это свойство позволит использовать ее при производстве различных электродов, а также искусственных мышц. В настоящее время для производства пленок используется способ помещения заранее расположенных параллельно друг к другу углеродных нанотрубок в специальные растворы и последующей их опрессовки. По словам китайских исследователей, пленки, изготовленные их методом, получаются гораздо прочнее.
Кевларовая ткань: свойства, производство, аналоги
На сегодняшний день кевларовая ткань повсеместно используется при пошиве одежды и экипировки людей, которые в процессе работы подвергаются опасности: военных, космонавтов, полиции, спортсменов и т.д.
Кевларовая ткань была разработана специалистами компании DuPont в 1965 году и является зарегистрированным товарным знаком пара-арамидного синтетического волокна.
реклама
Позднее были созданы волокна, по свойствам аналогичные кевлару, но все материалы, относящиеся к этому типу стали именовать кевларом. Массовое использование кевлара началось в 1970 году, когда этот высокопрочный материал стали использовать в гоночных шинах на замену тяжелой стали.В настоящее время кевларовое волокно используется в самых различных сферах: в производстве велосипедных шин, парусов яхт, в бронежилетах, для увеличения прочности частей углепластиковых стоп в протезировании.
Производство кевларовой ткани
Кевлар – чистейший полимер, получаемый с помощью поликонденсации в специальном растворе при низких температурах. В раствор хлористого кальция и метил-пирролидона добавляются реагенты, которые выделяют особое вещество с качествами жидких кристаллов.
Внешне они представляют собой гель или крошку, которую промывают и просушивают. Далее, пропуская получившийся полимер через фильеры, формируются нити или волокна, которые повторно направляются в осадительную ванну, промывают и снова высушиваются.
Производство кевлара – дорогостоящий процесс, т.к. возникают трудности с использованием серной кислоты, необходимой в процессе синтеза и образования волокон кевларовой ткани.
Свойства кевларовой ткани
Кевларовые нити обладают прочной структурой, которая по крепости превышает сталь в 5 раз, по жесткости кевлар может сравниться со стекловолокном.
Кевлар, не смотря на свое химическое происхождение, абсолютно безопасен для здоровья человека, устойчив к перепадам температур и сохраняет свои свойства в самых сложных условиях, не возгорается и не плавится.
Кевларовая ткань не боится воздействия органических растворителей, устойчива к коррозии. Под воздействием низких температур кевларовая ткань не только не портиться, но становится еще прочнее.
реклама
Изделия из кевларовых тканей защищают от ударов и порезов. Не смотря на все достоинства этого материала, есть у него и слабые стороны. А именно — под воздействием солнечных лучей и влаги структура ткани разрушается, волокна становятся менее прочными и теряют свои свойства.
Некоторые производители покрывают изделия из кевлара специальным оберегающим слоем, позволяя свести к минимуму и этот недостаток.
Применение кевлара
Как упоминалось выше, целью разработчиков было создание легкого, но в то же время прочного материала, который смог бы заменить тяжелую сталь при производстве шин.
Позднее, благодаря великолепным свойствам кевлара его начали использовать при пошиве одежды, спецовок, военной формы и т.д.
Броня
Кевлар является известным компонентом для производства средств личной брони и защиты. Боевые шлемы, баллистические маски для защиты лица и бронежилеты выполнены с применением кевлара.
Вооруженные силы различных стран применяют кевлар для создания пуленепробиваемых масок и подшлемников для экипажей бронетанковой техники.
Прочность кевлара настолько велика, что его применяют в качестве брони для авианосцев класса «Нимиц».
В гражданской сфере свойства кевлара используются при создании снаряжения для защиты работников органов экстренного реагирования. Бронежилеты сотрудников полиции, частных охранных предприятий и бойцов спецназа выполнены также из кевлара.
Спортивный инвентарь
Кевлар используется для обкладки велосипедных шип, что повышает их устойчивость к проколам. Также волокна кевлара применяются для увеличения отскока теннисных ракеток и уменьшения их веса.
В мотоспорте кевлар используется для производства безопасной одежды для спортсменов-мотоциклистов, укрепления элементов в области плеч и локтей.
Свойства кевлара с успехом нашли применение в других видах спорта – создания курток, брюк, элементов масок в фехтовании, в японской искусстве стрельбы из лука Кюдо для укрепления тетивы, для повышения производительности в парусах для гоночных лодок и т.д.
Музыкальные инструменты
Кевлар имеет отличные акустические свойства, которые нашли применение при создании диффузоров акустических динамиков для передачи низких и средних частот.
Кевлар используется в качестве основы в струнах для струнных инструментов. Струны из кевлара становятся более прочными, гибкими и стабильными к температурным скачкам.
Другие сферы применения
Благодаря своим физическим свойствам кевлар применяется как армирующее волокно, позволяя делать детали более легкими и прочными. Кевларовое волокно используют для укрепления кабелей, что защищает провода от растяжения и обрыва.
Возможность комбинирования кевлара с другими полимерами путем химической реакции позволяет создать более совершенные материалы, применяемые в специфических областях.
Как пример, карбон-кевлар, который отличается высокой термостойкостью и легкостью и применяется для строительства корпусов высокоскоростных лодок.
Уход за кевларовой тканью
реклама
Ухаживать за изделиями из кевлара не сложно, при этом нужно учитывать недостатки этого полимера, а именно:- не подвергать изделия воздействию высоких температур – при повышении температуры до 150С волокна теряют прочность;
- не стирать изделия слишком часто – на практике их не стирают вообще, так как кевлар боится воды. В некоторых ситуациях, когда изделия применяются в сложных природных условиях необходимо ограничить их соприкосновение с водой;
- не использовать для очистки изделий химические реагенты – реакция между полимером и другими химическими компонентами может быть непредсказуемой;
- не подвергать изделия воздействию солнечных лучей – это основной недостаток арамидных волокон, под воздействием ультрафиолета прочность кевларовых волокон снижается. При длительном воздействии солнечных лучей изделия из кевлара просто «рассыпаются».
Другие виды арамидных тканей
Помимо кевлара современная химическая промышленность разработана другие виды арамидных тканей.
Тварон
По свойствам и характеристикам аналогичен кевлару. Тварон был разработан компанией Тейджин Арамид, заводы которой расположены в Японии и Нидерландах. Ткань отличается высокой прочностью, небольшим весом, химической нейтральностью, термостойкостью, диэлектрическими свойствами и т.д. Но основное преимущество тварона заключается в отсутствии деформации даже в самых сложных условиях эксплуатации.
СВМ
Арамидная ткань, разработанная в 1970 году в СССР. Этот синтетический материал по свойствам схож с кевларом, но превосходит его по составу и некоторым параметрам. Аббревиатура СВМ расшифровывается как синтетический высокопрочный материал. Позднее на основе СВМ были разработаны нити второго поколения – Русар и Армос.
Новые арамидные волокна превосходят кевлар по следующим показателям – удлинение при разрыве, удельная нагрузка нити на разрыв, прочность нити и т.д.
Номекс
Номекс — разработка известной компании DuPont и относится к категории мета-арамидов. Номекс по прочности уступает кевлару, однако, стойкость к изгибу у номекса в 3 раза выше, чем у других арамидных тканей.
Номекс используется в авиации и судостроении, для изоляции кабелей и двигателей, в изделиях, подвергаемых воздействию высоких температур и т.д.
Как купить кевларовую ткань
Купить кевларовую ткань можно практически в любом магазине тканей. Стоимость кевлара варьируется в зависимости от плотности и вида – полотно, лента или нить. Средняя цена 1 м. кв. кевларового полотна составляет 2 500 рублей.
Купить изделия из кевлара можно в многочисленных интернет-магазинах, где представлены верхняя одежда из кевлара, брюки, ветровки, толстовки, перчатки и другая одежда.
Кевларовая ткань поражает своими физическими и химическими свойствами. Это современный высокопрочный материал, характеристики которого были по достоинству оценены и применены в самых различных областях от производства одежды до укрепления деталей авиационных двигателей.
Компании-разработчики арамидных тканей не останавливаются на одном кевларе, совершенствуя это волокно и создавая аналоги по свойствам превосходящие кевлар.
wearpro.ru
обзор свойств и сферы применения
Кевлар — название торговой марки высокопрочного полимерного материала (KEVLAR), разработанного учёными американской химической компании DuPont (Дюпон). По прочностным характеристикам превосходит сталь, но намного легче по весу.
Первый в группе
Кевлар был изобретён в 1964 году американской учёной-химиком Стефани Луизой Кволек во время её работы в Дюпон.
К 1971 году группе учёных компании удалось доработать материал, и началось его массовое производство.
Практически одновременно в России и Европе были созданы аналогичные волокна (СВМ и тварон), но так как кевлар был первым, все материалы, относящиеся к этой группе, стали называть именно так.
Производство
Кевлар выпускают в виде:
- технических нитей;
- пряжи;
- ровинга;
- тканей.
Свойства
Обычный диаметр волокон 1 мкм, непрозрачные.
- Основной характеристикой материала является его высокая механическая прочность. Плотность и, соответственно, масса достаточно низкие.
- Кевлар обладает устойчивостью к растяжению.
- Не горит и не плавится, обладает способностью к самотушению. Начинает разлагаться при температурах от 430 °C. При воздействии высоких температур начинает терять прочность только с течением времени, не сразу.
- Имеет устойчивость к органическим растворителям.
- Обладает высоким модулем упругости.
- Устойчив к коррозии.
- Под воздействием очень низких температур (криогенных) не только не портится, но и становится ещё прочнее.
- Обладает низкой удельной электропроводностью.
- Устойчив к порезам.
Применение
Изначально целью разработчиков было создать лёгкое, но очень прочное волокно, которое можно было бы использовать при производстве шин.
Кевларовые ткани
Выпускаются обычно в виде полотна в рулонах под названием Кевлар-49. Также бывают другие виды:
- штапель-кевлар — коротко нарезанные волокна длиной чуть более шести мм. Прочностные свойства теряются из-за нарезки, но сохраняются барьерные. Используется для производства пряжи, войлока и нетканых изделий с высокими теплоизоляционными и виброизоляционными свойствами;
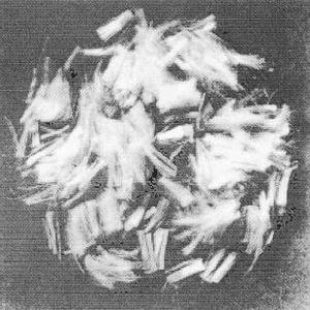
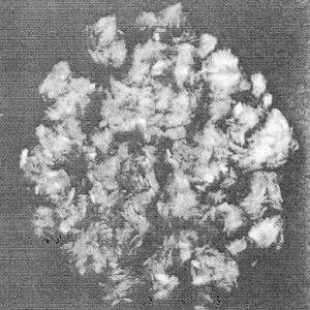
- флок-кевлар — измельчённое волокно (до 1 мм), применяют для армирования различных смол.
- теряют прочность при истирании;
- разрушаются под действием ультрафиолета. Требуют специального покрытия смолой.
Защитная одежда
Армирующие свойства кевлара используют, включая его в состав тканей, из которых изготавливают элементы защитной одежды: перчатки, отдельные вставки в костюм, наколенники, антипрокольные стельки, одежду спортивной группы — для сноубординга, мотоспорта и т. д. Подобная ткань становится устойчивой к порезам и прокалыванию.
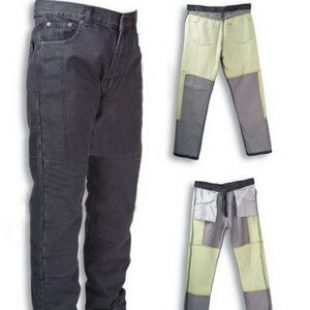
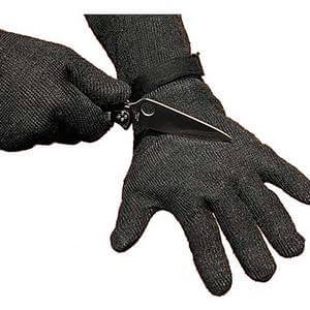
С 1970 года велась разработка, а затем началось производство лёгких пуленепробиваемых бронежилетов из нескольких слоёв кевлара. Для того чтобы качества материала не ухудшались под воздействием воды и ультрафиолета, кевларовый бронежилет имеет покрытие из водостойкой ткани.
Также производят другие элементы защиты от огнестрельных и осколочных поражений, например, в бронеавтомобилях.
Спортивное снаряжение
Лыжи, доски для сноуборда, шлемы, лодки и вёсла из кевлара обладают очень высокой прочностью и лёгкостью.
Судостроение
Кевлар начали применять в судостроении относительно недавно — последние два десятилетия. Процесс его производства высокотехнологичный и достаточно дорогой, поэтому его применяют выборочно — для отделки корпуса по швам, в килевой части.Применяется для строительства яхт. Из этого материала они получаются очень лёгкими, расходуют меньше топлива и способны развивать более высокую скорость.
Другие сферы
- Кевлар используется в качестве армирующего волокна, чтобы придать материалу прочность и лёгкость. Им укрепляют кабели, продевая нить из кевлара по всей длине, защищая его от растяжения и обрыва.
- Также его применяют для изготовления ортопедических протезов.
- Кевларовые канаты характеризуются высокой прочностью, малым весом, устойчивостью к коррозии, неэлектропроводностью, благодаря чему широко используются в судостроении и горной промышленности, где заменяют стальные тросы.
- Прочностные свойства волокон кевлара объединяют с термостойкостью карбона и получают гибридный материал — карбон-кевлар. Его используют для строительства корпусов лодок, способных развивать высокую скорость.
© 2018 textiletrend.ru
textiletrend.ru
Изготовление карбона. Карбон на авто
Карбон или углепластик – сокращенное название от английского Carbon Fiber (углеродное волокно), под маркой которого, объединилось большое количество различных композитных материалов (также, как например, сотни органических материалов с определенными физическими свойствами, называют пластмассами). Карбон получают из углеродного волокна и используют, как армирующий наполнитель для производства различных высокопрочных композитных материалов. Самое удивительное, что карбон или углепластик, делают из жидкости. Точнее, из жидкого полимера – полиакрилонитрила. Для этого, из полиакрилонитрила, сначала получают полиакрилонитрильное волокно, которое получают, путем продавливания исходного полимера – полиакрилонитрила, через специальную фильеру с сотнями тончайших отверстий, диаметром около 50 микрон. Под давлением, в горячей воде, через крохотные отверстия фильеры, непрерывным потоком, "выходят" тонкие белые ниточки,
которые и являются исходным сырьем для дальнейшего изготовления карбона. После прохождения через несколько ванн со специальными растворами, полученные полиакрилонитриловые волокна становятся в несколько раз тоньше, а их молекулы выстраиваются таким образом, что волокна становится еще прочнее. После этого, полиакрилонитрильное волокно проходит многоэтапный процесс обработки, который изменяет внутреннюю структуру вещества на молекулярном уровне. Данный процесс включает в себя высокотемпературную обработку, окисление и "карбонизацию" (насыщение углеродом) в инертной среде, в результате чего получается конечный продукт – материал карбон или углеродное волокно.
Наиболее важное свойство карбона или углеволокна – это уникальное соотношение низкого веса и исключительной прочности. Модуль упругости отдельных "сортов" карбона может превышать 60 ГПа, а разрывная нагрузка может достигать 5 гПа, при этом карбон в полтора раза легче стали и на четверть легче алюминия. Для придания большей прочности, карбоновые волокна переплетают между собой особым образом, с разным углом направления плетения и затем, шьют из них специальные высокопрочные карбоновые ткани, способные выдерживать колоссальные механические нагрузки. Композитные армирующие материалы на основе карбона стали использовать для создания монококов спортивных и гоночных автомобилей, корпусов скоростных катеров, мачт океанских яхт, винтов вертолетов, корабельных тросов, для изготовления специальной экипировки и многого другого. Благодаря выдающихся технико-эксплуатационных характеристик и декоративных свойств, карбон стал широко использоваться и в автотюнинге, для отделки кузовных элементов автомобилей. И если раньше, натуральный карбон можно было увидеть только на дорогих спортивных или представительских автомобилях, то уже сейчас продаются автомобили, в которых покрытие карбоном входит в базовую комплектацию, при этом, при покупке у дилера нового автомобиля, можно выбрать нужный цвет карбона или заказать понравившийся вид карбона, например, матовый карбон или карбон под лаком. Помимо этого, сейчас уже почти в каждом тюнинговом ателье вам могут полностью обтянуть карбоном машину, обклеить салон карбоном или обклеить машину карбоновой пленкой, или даже, предложат купить карбоновую пленку, для оклейки карбоном своими руками.
Материал – кевлар: кевларовая ткань
Кевларовая ткань представляет собой паpа-аpамидное синтетическое волокно, которое производят из синтетического полимера - полипарафинилин терафталамида. Кевларовые волокна обладают исключительной прочностью (разрывная прочность может доходить 600 кг/мм2), и высоким сопротивлением к ударам и динамическим нагрузкам. Кевларовые волокна обладают высокой термической стойкостью (разлагается при температуре, более 4500 С) и сохраняют прочность, и эластичность (и даже становятся чуть прочнее) при крайне низких, криогенных температурах, до - 2000 С. Из кевларовых волокон плетут армирующие нити, из которых, также, как и из карбона, делают специальные высокопрочные кевларовые ткани, используемые затем, для производства различных армирующих материалов. В отличие от карбона, кевларовый материал может легко деформироваться и имеет наилучшее показатели по скорости поглощения энергии, и длительности взаимодействия с ударником, обеспечивая высокую противопульную и противоосколочную стойкость, благодаря чему, кевларовая ткань является основным армирующим компонентом при производстве бронежилетов и различных средств безопасности. В качестве армирующего материала, кевларовая ткань широко используется при производстве самолетных шин, пуленепробиваемых покрышек, корабельных канатов, специальной защитной одежды и многого другого. Перчатки, сшитые из кевлара защищают руки от ожогов, порезов, в них можно смело хвататься за лезвие ножа без риска порезаться. Для получения эластичного армирующего материала на основе кевлара, несколько слоев кевларовой ткани сшивают вместе и затем спекают с резиновой основой. Тем не менее, у кевлара, как и у любого другого композитного материала, есть свои недостатки. Кевлар разрушается от ультрафиолетового излучения, а в смоле, в виде формованного материала, при длительном воздействии уф-лучей, кевларовая ткань также значительно ухудшает свои свойства. Помимо этого, кевлар сохраняет высокое сопротивление на разрыв и стойкость к порезам только в "сухом" виде. С конца прошлого века началось производство комбинированных армирующих материалов или гибридных тканей, сотканных из равного количества кевларовых и карбоновых нитей, обладающих лучшими эксплуатационными показателями, чем материалы, сделанные из натурального карбона или кевлара. Из карбон-кевларовых нитей плетут тонкие и прочные корабельные канаты, изготавливают корды в автомобильных шинах, делают автомобильные ремни безопасности, приводные ремни и мн. др.
Виниловые "карбоновые" пленки. Иммерсионные пленки под карбон.
Среди недостатков карбоновых, кевларовых или гибридных армирующих материалов можно отнести высокую стоимость исходного сырья и длительное время изготовления конечного продукта. Но, если в исключительных физических свойствах карбона или кевлара нет необходимости, можно использовать внешнюю отделку: покрытие карбоном или перетяжка карбоном. Для отделки карбоном идеально подходят два типа покрытий: самоклеющиеся виниловые карбоновые пленки "3D carbon" и "4D carbon", и иммерсионные пленки под карбон, наносимые методом аквапечати или аквапринта.
Наличие в карбоновых пленках воздушных "каналов", значительно упрощает процесс обтяжки карбоном кузовных элементов и позволяет наклеивать карбоновые пленки на различные сложно профилированные поверхности. Карбоновые пленки стоят дешевле карбоновой ткани и не требуют какой-то специальной подготовки поверхности. После оклейки изделия карбоновой пленкой, покрытие ничем не отличается от формованного покрытия из натурального карбона. Обтяжка карбоном (виниловыми пленками "3D carbon" и "4D carbon"), это простой и экономичный способ имитации карбонового покрытия, не требующий использования для этого, дорогостоящих натуральных карбоновых тканей или материалов.
Другой вид отделки карбоном – использование wtp-пленок под карбон, наносимые методом иммерсионной (аква) печати. Wtp-пленки под карбон позволяют имитировать плетения различных карбоновых или кевларовых тканей и после проведения процесса аква-печати и нанесения на поверхность карбоновой пленки, изделие ничем не отличается от изделия, сделанного от натурального карбона или покрытого натуральной карбоновой тканью. К дополнительным преимуществам использования wtp-пленок, можно отнести большой выбор вариантов "плетений", под карбон или кевлар. При этом, благодаря большому выбору пленок "под карбон", можно выбрать не только понравившийся "рисунок" плетения карбоновых нитей, но и цвет карбонового покрытия, и текстуру карбона.
impgold.ru
что это такое? Материал кевлар. Производство кевлара
У каждого поколения, живущего в ту или иную временную эпоху, свои правила и устои, требования к мобильности и качеству жизни. Соответственно, за ускорением научно-технического прогресса во всех отраслях следует и повышение общего темпа, а новое время диктует свои правила. Так что своеобразная мода на вещи с включением кевларовых нитей коснулась не только специализированных подразделений, в том числе и военных, но и обычных обывателей, которые ценят свою безопасность и любят комфорт.
Кевлар: что это такое?
Прочные кевларовые волокна давно вплелись в структуру разработок в автомобильной, строительной, военной отраслях промышленности, частично вытеснив менее прочную и практичную сталь. «Сотканный» из органических нитей материал стал просто незаменимым благодаря своим уникальным характеристикам. Итак, теперь подробно рассмотрим вопрос о том, кевлар - что это, и узнаем историю его появления.
Вкратце о возникновении
Новый полимер в каком-то смысле стал «ребенком» его величества Случая, родившись в лабораториях компании Dupont, которая уже на тот момент имела в своем активе изобретение такого материала, как нейлон. Тогда, в 1964-м, исследовательская группа искала решение, как заменить стальной корд в автомобильных шинах на значительно более легкие полимерные нити, например полиарамидные. Соответственно, занятие было не из простых, поскольку полиарамиды предварительно необходимо растворить (что само по себе нелегкое дело), а уже затем из получившейся массы «прясть» нити. Положительного результата удалось достичь Стефани Кволек. Она сумела получить волокна исключительной прочности, которые после тестирования показали ошеломляющие результаты - новая нить оказалась прочнее стали.
Но это было лишь начало блестящей истории этого материала. Ткань кевлар появилась на рынке в 1975 году, и с того времени на недостаток спроса жаловаться не приходится. А он рождает производство, так что Dupont не останавливается на достигнутом. Компания осуществляет заметные финансовые вливания, направленные на то, чтобы модернизировать запатентованный материал кевлар и наделить его улучшенными характеристиками.
Состояние на сегодня
Теперь перейдем к нашему времени. Современный кевлар - что это? А это на удивление легкий и мягкий материал, который в огне не горит и даже почти не тлеет, влагу прекрасно впитывает, позволяя кожным покровам «дышать», а при этом по своей прочности превосходит сталь в разы, выдерживая нагрузку на разрыв в пределах 2500 Н. Да и обработка ткани достаточно легка и не требует узкопрофильного оборудования.
Как производят
Волокнообразующие полимеры производятся при низкой температуре путем поликонденсации в растворе. К последнему добавляют реагенты и интенсивно перемешивают. Из этого раствора выделяется полимер в виде крошки или геля. Далее его промывают и высушивают. Затем полимер растворяют в сильных кислотах (например, в серной). Из получившегося раствора методом экструзии формируются нити и волокна. Они промываются и просушиваются.
Кевларовые волокна – кристаллизующий полимер. Их структура отличается высокой степенью жесткости. Это обусловлено наличием бензольных колец. По структуре кевлар относится к сетчатым полимерам. Производится он в виде технических нитей, имеющих различную линейную плотность и структуру. Количество волокон в нитях может быть разным: от 130 до 1000 при производстве кевларовой ткани и от 500 до 10 тыс. при изготовлении корда и канатов. Этот материал выпускается в виде ровинга, ткани и пряжи. Волокна непрозрачны, их средний диаметр – 11 мкм.
Сферы применения
Свое применение кевлар находит в тех отраслях, где крайне важны стойкость к износу и термическая стабильность, низкая структурная жесткость и максимальная легкость, а также отличная прочность при низком весе. Поэтому неудивительно, что этот материал пришелся «ко двору» при изготовлении средств индивидуальной защиты, в частности бронежилетов, шлемов.
Кевлар: защищаемся с комфортом
На сегодняшний день изготавливается различная одежда из кевлара, предназначенная не только для военнослужащих и различных спецподразделений, но и для тех, кто выбирает ультраактивный образ жизни и помешан на той же охоте или страйкболе. Конечно, страйкболисту ни к чему кевларовая броня с высоким уровнем защиты и дополнительными бронепластинами, а вот футболка со специальными кевларовыми вставками будет весьма уместной. К тому же, такие элементы легко скрыть под верхней одеждой, да и подходящие по дизайну модели разработаны.
Пожалуй, наиболее популярными изделиями из кевлара можно считать бронешлемы, тактические перчатки и, конечно же, бронежилеты. Кстати, именно из этой ткани и изготавливают средства пассивной защиты, принятые на вооружение в НАТО.
Защита на руки
Тактические перчатки с кевларом в виде защитных вставок на ладонях и костяшках позволяют не только защитить руку от повреждений при столкновении, например, с зубами противника, но и значительно усилить удар, сделав его сокрушающим. Такой своеобразный современный аналог кастета. Если учитывать прочность, теплоту и устойчивость к влаге и повреждениям, такие аксессуары в последнее время популярны не только у сотрудников специализированных подразделений, но и у экстремалов, уличных бойцов, любителей активного образа жизни. Также они пользуются спросом у тех, у кого темные улицы родного населенного пункта вызывают вполне обоснованные опасения.
И пулю, и штык... остановит ли кевлар?
Бронежилет из кевлара по праву считается одним из наиболее надежных средств индивидуальной пассивной защиты. Благодаря своей уникальной легкости, прочности и относительной долговечности такая «броня» способна защитить владельца от скользящих ударов холодного оружия и смягчить последствия попадания пуль, препятствуя проникновению и распространению осколков.
Выбирая бронежилет, в основе которого используется данный полимер, следует учесть некоторые нюансы, которыми он наделен. Кевлар - что это? Мягкая броня, которая не спасет от выстрела в упор или проникающего удара ножом или шилом, поэтому разработаны модели со специальными жесткими панелями, призванными дополнительно амортизировать удар.
У всех свои минусы
К недостаткам кевлара можно отнести светочувствительность - при длительном пребывании под солнечными лучами чудо-материал начинает разрушаться, хоть и очень-очень медленно. Оптимальным средством предохранения стало вшивание элементов с кевларовыми нитями в более плотную ткань.
Цена на изделия с параамидными нитями достаточно высока, и именно это препятствует всеобщей «кевларизации». Оснащать армию тактическими изделиями из данного материала могут себе позволить только развитые в экономическом плане страны.
В завершение
На сегодняшний день крайне сложно представить пассивную защиту без кевларовых волокон, а выполненные из такой ткани бронежилеты и шлемы, каски спасли множество жизней. Поэтому создателям есть чем гордиться. А изготовителям нужно расширять производство кевлара и постоянно улучшать характеристики его качества.
fb.ru