Применение плёнки ПВХ на поверхности МДФ. Технология нанесения пленки пвх на дверь температура плавления
Пленка пвх на мдф поверхностях
Производство фасадных частей корпусной мебели предусматривает использование натурального дерева и МДФ. Именно эти материалы хорошо поддаются разным видам обработки, включая механическую. С помощью фрезерования изготавливаются детали разных форм и конфигураций, в том числе криволинейных. Долговечность мебельным атрибутам обеспечивает декоративное плёночное покрытие. Применяется для облицовки деталей из МДФ пленка ПВХ, которая прекрасно зарекомендовала себя эстетическими показателями и эксплуатационными характеристиками.
Особенности монтажа
В производственном процессе задействуется мембранно-вакуумная технология. На пресс укладываются элементы фасада из МДФ, пленка ПВХ натягивается. Для облицовки заготовок корпусной мебели применяется пленочный материал толщиной 0,2-0,55 мм. На основании этого параметра подбирается температурный режим, который не приводит к перегреву поливинилхлоридной основы. В ином случае образуются оплавленные отверстия, появляются глянцевые пятна, нарушается герметичность. При низкой температуре нагрева пленочное покрытие не приобретает необходимых показателей эластичности, присутствует недостаточная реакция клея, в результате чего снижается качество соединения покрытия и основы.
В процессе изготовления фасадов из МДФ пленка ПВХ применяется разных цветов, что также оказывает непосредственное влияние на выбор температурного режима:
- Для термоусадочных покрытий темного цвета технологические процессы наступают при температуре от 45 до 60 °С.
- Для светлых аналогов, включая глянцевые пленочные покрытия, температура нагрева составляет 120-135 °С.
Под тепловым воздействием начинается движение пленки и именно в этот момент необходимо следить, чтобы не образовались складки. Признаком готовности пленочного покрытия к натягиванию и включению вакуумного насоса являются состояние поверхности «в струнку» и наличие небольшой задымленности над ней. Это указывает на то, что достигнутая температура имеет максимальный предел, при котором должен происходить процесс обтягивания заготовок из МДФ.
Процедура проходит при слегка открытом кране вакуума и отключенном нагреве, по истечении 2-3 секунд температура снова повышается. В местах соприкосновения с МДФ пленка ПВХ остывает и огибает боковины деталей. В этом момент должен быть включен вакуум и не останавливается тепловой процесс, который длится до тех пор, пока не будет обтянут фасад и его боковые части.
Особенности использования МДФ покрытого плёнкой
Пленка из поливинилхлорида или ПВХ является уникальным декоративным материалом, который нашел широкое применение в мебел
vibor.su
Технологии применения декоративных ПВХ пленок. Статьи компании «ТОО «Phlox Group»»
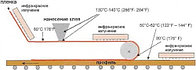
Мембранно-вакуумное прессованиеМембранное или вакуумное прессование — это процесс, при котором давление равномерно прижимает разогретую пленку к поверхностям, уложенным на столе заготовок, а температура, накопленная пленкой, активирует клеевой слой. Технология мембранно-вакуумного прессования позволяет облицовывать ПВХ пленками наиболее сложные глубокие профили фасадных деталей и погонажных изделий. С помощью такой технологии можно создавать непрерывные линии профиля и придавать изделиям округлые формы. Как результат поверхности обладают повышенной износоустойчивостью, увеличивающей срок эксплуатации изделий. Процесс 3D ламинирования фасадов возможен, благодаря особенности ПВХ пленки после нагревания становиться пластичной, а после охлаждения сохранять принятую форму. На этом принципе построено оборудование для ламинирования фасадов — вакуумных и вакуумно-пневматических прессов. Мембранно-вакуумный пресс — пресс для покрытия деталей различными финишными и декоративными покрытиями. Пресса бывают двух разных типов – более простые и дешевые вакуумные, использующие атмосферное давление и пресса с дополнительным давлением 1-8 кг/см 2, которые значительно сложнее и дороже вакуумных. Оба вида прессов могут оснащаться мембранами для прессования пористых материалов или шпоном и работать без мембраны с пленками ПВХ. Пресса с дополнительным давлением прессуют детали при давлении 0,6-8,5 кг/см2, вакуумные пресса могут дать максимальное давление на деталь не более 0,95 кг/см2, впрочем как показывает практика его вполне хватает для большинства случаев прессования различных изделий, за исключением случаев покрытия шпоном деталей со сложным профилем. При работе со шпоном желательно применение прессов с дополнительным давлением в 5-8 кг/см2. Остановимся подробнее на работе вакуумного пресса. Конструктивно пресс состоит из стола, на котором размещаются заготовки; нагревателя, используемого для разогрева пленки; а также вакуумной системы, обеспечивающей создание равномерного давления на пленку за счет атмосферного давления или нагнетания избыточного давления. Обычно процесс ламинирования в вакуумном прессе выглядит так: 1. Заготовки с предварительно нанесенным и просушенным клеевым слоем равномерно размещаются на плоскости стола на специальных подкладках, соразмерных с заготовкой, для обеспечения возможности растяжения пленки и более полного облегания ею заготовки. С той же целью между заготовками сохраняются специальные технологические зазоры. 2. Над всей плоскостью стола закрепляется и фиксируется прижимной планкой ПВХ пленка. Декоративная пленка обжимается по рельефу с помощью эластичной мембраны (в мембранных прессах) или с помощью создания вакуума под пленкой (в вакуумных прессах). 3. Далее происходит нагрев пленки. Разные конструкции прессов предполагают разный принцип совмещения стола и нагревателя. В одних прессах подвижным является стол, в других — нагреватель. По принципу нагревания различают контактный, когда пленка непосредственно соприкасается с нагревателем, и бесконтактный, или инфракрасный, способ прогрева. Конечный результат должен обеспечить равномерный прогрев пленки до определенной температуры, рекомендованной производителем декоративной ПВХ пленки. Температура нагрева в мембранном прессе достигает – максимум — 160С, минимум — 140С. 4. После нагрева пленки начинается этап вакуумирования (т. е. непосредственно прессования). Под этим подразумевается удаление воздуха из полости между поверхностью стола и натянутой над заготовками пленкой. В результате атмосферное давление с усилием (например, 950 кг/м2) равномерно прижимает разогретую пленку к поверхностям уложенных на столе заготовок, а температура, накопленная пленкой, активирует клеевой слой. По окончании периода выдержки под давлением (1,5-3 мин. ) процесс приклеивания пленки заканчивается, хотя прочность клеевого шва достигает максимального значения только спустя несколько суток. 5. После завершения этапа прессования и остывания пленки, заготовки обрезаются по контуру детали от излишков пленки.Основные сферы применения декоративных ПВХ пленок для мембранно-вакуумного прессованияСтолешницы: Фасады МДФ: Дверные и декоративные накладки: Декоративные элементы оформления: Таким образом, основное назначение ПВХ пленок при технологии мембранно-вакуумного прессования (3-D — ламинирование) – это облицовывание рельефной мебельной поверхности. Ниже приведены примеры использования декоративных мебельных пленок ПВХ по технологии мембранно-вакуумного прессования.Каширование мебельных поверхностейТермин «каширование» происходит от французского cacher, что означает в переводе «прятать», «закрывать», «скрывать». В общем случае каширование — это процесс укрытия поверхности основного материала облицовочными пленками с целью улучшения его внешнего вида. В мебельной промышленности под кашированием понимают процесс облицовывания пластей рулонными пленочными материалами с использованием вальцовых прессов и последующим отверждением клеевого слоя различными способами. В общем случае каширование предусматривает следующие операции: • очистка кромок и пластей детали от пыли; • нанесение клея на пласти детали; • удаление влаги из клеевого слоя; • размотка пленки из рулона и ее накатывание на пласти деталей; • разделение (разрубание) непрерывного полотна пленки в разрывах между деталями; • повторное прикатывание пленки; • отверждение клеевого слоя.В зависимости от степени температурного воздействия на клеевой слой технологические процессы каширования условно разделяются на холодное, теплое и горячее каширование. При холодном кашировании удаление излишней влаги из клеевого слоя проводится при температуре цеха, а отверждение клея после накатывания пленки — в стопе, в специальном холодном прессе или без пресса, с нагружением сверху для прижатия пленки на верхних деталях стопы. Время отверждения клея — от нескольких часов до суток. Как правило, именно этот способ применяется для облицовки гладких мебельных поверхностей ПВХ пленками. Теплое каширование предусматривает промежуточный нагрев клеевого слоя для удаления из него влаги с целью снижения времени последующего отверждения клея и снижения разбухания верхнего слоя плиты из-за впитывания. Окончательное приклеивание также производится в стопах, но время выдержки при этом снижается до нескольких часов. Горячее каширование включает практически те же операции, что и теплое, но накатывание и прикатывание рулонного облицовочного материала производится горячими валами, нагреваемыми до температуры 120-160 С. В некоторых моделях оборудования дополнительно используются нагреваемые до 160-180 гр. C валы, устанавливаемые перед станком для нанесения клея, что позволяет вдавить в плиту воткнувшиеся мелкие частицы, не удаленные щеточным станком, «припаять» частично отслоившиеся стружки ДСП за счет расплавления лигнина, выровнять температуру на поверхности и нагреть пласти для ускорения выпаривания влаги. После первичного нанесения клеевого слоя и его частичного высушивания сверху может наноситься слой отвердителя. Тогда после накатывания и прикатывания пленки горячими валами сразу же достигается ее приклеивание. Такая технология позволяет использовать клеи на основе карбамидных смол и обеспечивает практически мгновенное склеивание, исключающее промежуточную выдержку деталей перед последующей обработкой. Quickstep Одной из разновидностей горячего каширование является способ Quickstep. Способ был предложен в начале 70-х годов фирмой Bison для облицовывания плит пленками с заранее нанесенным слоем клея-расплава. Технологическая линия для облицовывания этим способом состоит из комбинации обычной линии холодного каширования, разгонного ленточного транспортера и короткотактного однопролетного пресса, обеспечивающего необходимые давление и температуру при облицовывании. В настоящее время способ Quickstep применяется для облицовывания с использованием любых клеев: на основе ПВА-дисперсий и карбамидных, ускоренного отверждения. Линии холодного каширования применяются в производствах с относительно небольшой производительностью, при облицовывании достаточно толстыми пленками (до 130 г/кв. м), с использованием относительно дорогих клеев на основе ПВА-дисперсий. Возможность разбухания крупной стружки на поверхности ДСП из-за отсутствия удаления влаги из клеевого слоя делает более предпочтительным облицовывание на таких линиях материалов с анизотропной структурой — типа ДВП или МДФ. Линии теплого каширования за счет наличия зоны выпаривания влаги из клеевого слоя позволяют облицовывать и древесностружечные плиты, обеспечивая более высокое качество поверхности. Линии типа Quickstep дают наиболее высокое качество облицовывания за счет использования плоского пресса, обеспечивающего выравнивание прессуемой поверхности и более равномерный нагрев. Однако производительность таких линий ниже и ограничивается скоростью подачи проходного участка (каширование) 7-10 м/мин. Но такие линии могут обеспечивать применение облицовочных пленок практически любой массы (60-140 г/кв. м), любых клеев (ПВА-дисперсий и карбамидных) и практически полностью исключают появление дефектов поверхности от разбухания стружки. Кроме того, при оснащении плит пресса специальными матрицами возможно тиснение структуры поверхности на облицованной пласти, что практически невозможно при использовании только вальцовых прессов. Линии горячего каширования на базе вальцовых или ленточных прессов обладают наибольшей производительностью (до 50 м/мин. ), но требуют весьма тщательного соблюдения технологических режимов: расхода клея и отвердителя, температуры нанесения и отверждения клея и др., но главное — плотности и разной толщины облицовываемых плит. Во всех случаях клей наносят преимущественно на плиту кистью (или валиком) при ручном методе, или клеенаносящими вальцами на линиях каширования, где пленка непрерывно разматывается с рулона и прижимается к поверхности плиты. Клей на линиях каширования непрерывно подается на вальцы либо самотеком, либо с помощью насоса. При кашировании толщина пленки обычно составляет 150 – 200 микрон, при этом используется линия каширования.Облицовка профиля Принцип облицовки профильных погонажных изделий в каком-то смысле аналогичен кашированию мебельных поверхностей. Вместе с тем, оборудование для каширования плит (линии каширования) и для профильных погонажных изделий (установки для облицовки погонажа) заметно отличаются по конструкции. Основной особенностью последних является наличие прижимных валков для более точной облицовки изгибов профиля. Кроме того, говоря об облицовки профильных изделий (особенно это касается ПВХ профиля), часто упоминают термин «ламинирование». Однако главный признак ламинирования — отсутствие в процессе облицовывания такого этапа, как нанесение клея, что недопустимо в нашем случае, т. к. речь идет о ПВХ пленках без клеевого слоя. Таким образом, называть процесс окутывания профиля пленкой «ламинированием» – не может быть верным. Тем не менее, далее в тексте этот термин встречается в отношении облицовки оконного ПВХ профиля и пластиковых подоконников, поскольку он общепринят и распространен среди участников рынка. Процесс облицовки (ламинирования) включает несколько стадий:• обработка пленки клеем • прохождение пленки через сушильный канал • подогрев профиля • приклеивание пленки при помощи прижимных валков Таким же способом декорируются поверхности профильно-погонажных изделий из ДВП, ДСП, применяемые преимущественно для отделки внутренних помещений.
http://www.newchemistry.ru/letter.php?n_id=836
goldy-kc.kazprom.net
Процесс производства плёнки ПВХ
Современные мебельные атрибуты представлены на рынке в большом разнообразии не только цветовых и дизайнерских решений, а также удивляет огромным выбором текстуры. Достигается такое изобилие благодаря тому, что производители применяют специальное пленочное покрытие, которое создает прочную и эстетичную верхнюю основу. Существует определенный процесс производства плёнки ПВХ для мебели. Каждый вариант декоративного материала следует рассмотреть в отдельности.
Виды плёночного покрытия и способы нанесения
В зависимости от типа рабочей поверхности подбирается декоративный материал. Процесс производства плёнки ПВХ основан на трёх основных способах нанесения:
- Ламинирование. Этот процесс производства плёнки ПВХ проходит на специальной линии ламинации, обеспечивающей заготовкам из МДФ и ДСП надежное покрытие. Обёртывание длинномерных деталей декоративным материалом толщиной 0,3-0,5 мм. В результате создается прочное скрепление с основой, благодаря чему повышается влагостойкость. На протяжении длительного периода эксплуатации покрытие не вздувается.
- Мембранно-вакуумное прессование применяется для создания декоративной отделки поверхностей фасадов корпусной мебели. Обработке подлежат полки, дверки, столешницы. Технологией предусмотрено применение специального оборудования — вакуумного пресса, с помощью которого бумажно-смоляной материал толщиной 0,25-0,5 мм подвергается высокому давлению и температуре. В результате получается прочное равномерное покрытие с высокими показателями влагостойкости и эстетичности. Дизайнерская линия включает в себя однотонные покрытия, имитацию фактур природных материалов, различные рисунки и узоры.
- Кэширование гладких поверхностей. Данный процесс производства плёнки ПВХ основан на нанесении клеевого слоя на заготовку из МДФ и ДВП. Под воздействием высокой температуры и давления декоративный материал толщиной 0,2-0,3 мм плотно приклеивается к элементам мебельного фасада. Для кэширования заготовок из ДСП не все виды плёночного покрытия подходят, поэтому материал подбирается с учётом структуры плит.
Технологический процесс производства плёнки ПВХ позволяет максимально разнообразить мебельную продукцию, придать ей соответствующих декоративных и эксплуатационных свойств. Потребителям предлагается огромный выбор мебели, которая способна удовлетворить все запросы покупателей и прекрасно вписывается в интерьер любого помещения.
vibor.su
Виды декоров "Эко-Шпон"
Декоративная облицовочная пленка - это полимерная пленка (не самоклеющаяся), предназначенная для облагораживания различных поверхностей. Часто используют другое обозначение – «мебельная» пленка. Данная пленка в России практически не производится, между тем объем ее потребления на российском рынке в 2006 году составил около 28 млн.кв.м, что в тоннажном выражении равняется примерно 14-15 тыс.тонн.
Основным видом полимерных пленок, используемых для облицовки, являются пленки на основе поливинилхлорида (ПВХ), толщиной, как правило, 0,2-0,55 мм. Реже встречаются отделочные материалы на основе полистирола, акриловых полимеров и пр. Они могут быть прозрачными или пигментированными (например, с рисунком древесной текстуры), глянцевыми, матовыми или полуматовыми, жёсткими или эластичными. ПВХ пленки, благодаря огромному разнообразию цветов, текстур и тиснений, позволяют имитировать на поверхности облицовочного материала натуральное дерево, мрамор, камень и т. п., причем не только на вид, но и на ощупь. Это не только красиво, но и практично, долговечно и недорого.
ПВХ пленка обладает следующими преимуществами:
- не подвергается старению
- устойчива к механическим и химическим повреждениям
- устойчива к атмосферным воздействиям и низким температурам
- устойчива к УФ-лучам (высокая светостойкость)
- обладает высокой прочностью
- невосприимчивость к образованию пятен
- возможность очистки
В зависимости от применения декоративные (облицовочные) ПВХ пленки можно условно разделить на несколько категорий:
1. Пленка для мембранно-вакуумного прессования
Пленки для мембранно-вакуумного прессования предназначены для облицовки рельефных (филенчатых) поверхностей таких как: объемные мебельные фасады (из МДФ), дверные полотна, закругленные столешницы, а также различные декоративные элементы мебели при помощи специального оборудования – вакуумного пресса (с мембраной или без нее). Как правило, для этих целей используются более толстые пленки, толщиной 0,3-0,5 мм (300-500 микрон), реже 0,25 мм (250 микрон), как однотонные, так и с печатным рисунком с текстурой «под дерево».
2. Пленка для каширования (ламинации) профильных погонажных изделий
Данная категория пленок используется для окутывания профильных погонажных изделий из любых материалов, будь то дерево, пластик (ПВХ) или металл (алюминий). Облицовывание профиля осуществляется с помощью облицовочной установки (станок для окутывания профильного погонажа). Следует отметить, что для ламинирования оконного/дверного профиля используются двухслойные ПВХ пленки с верхним акриловым слоем для защиты от УФ-излучения.
3. Пленка, используемая для каширования гладких поверхностей
Этот вид пленки подходит как для облицовки ровных поверхностей таких как: панели (ПВХ и МДФ), древесностружечные плиты (МДФ И ДСП), стенки корпусной мебели, подоконники с помощью установок каширования. Сразу стоит оговорить, что использование полимерных пленок для облицовки ДСП весьма ограниченно из-за невысоких физико-механических характеристик получаемого покрытия и низкой теплостойкости. Для этой цели используются более тонкие пленки, чаще до 0,25-0,3 мм (250-300 мм).
Выше описанную классификацию можно кратко представить в виде следующей таблицы:
Облицовка объемных филенчатых деталей (технология 3D) | МДФ, ДСП | мебельные фасады | мембранно-вакуумный пресс |
столешницы | |||
дверные накладки | |||
декоративные элементы мебели | |||
Облицовка погонажных профильных изделий | ПВХ, АL, МДФ, дерево | оконный профиль | установка для окутывания погонажных изделий (облицовочный станок) |
дверной профиль | |||
плинтуса | |||
отделочный профиль | |||
Каширование гладких поверхностей | ДСП, МДФ, ПВХ | подоконники | Кашировальные установки |
панели | |||
внутренние стенки мебели | |||
плоские поверхности мебели |
Технологии применения декоративных ПВХ пленок
Для получения декоративного покрытия термопластичная ПВХ пленка прессуется или кашируется (ламинируется) на ДСП, МДФ или ПВХ с предварительно нанесенным клеевым покрытием. При этом используются следующие технологические линии:
1. вакуумные или мембранные пресса
2. установки каширования
3. установки для окутывания погонажных изделий
Мембранно-вакуумное прессование
Мембранное или вакуумное прессование - это процесс, при котором давление равномерно прижимает разогретую пленку к поверхностям, уложенным на столе заготовок, а температура, накопленная пленкой, активирует клеевой слой.
Технология мембранно-вакуумного прессования позволяет облицовывать ПВХ пленками наиболее сложные глубокие профили фасадных деталей и погонажных изделий. С помощью такой технологии можно создавать непрерывные линии профиля и придавать изделиям округлые формы. Как результат поверхности обладают повышенной износоустойчивостью, увеличивающей срок эксплуатации изделий. Процесс 3D ламинирования фасадов возможен, благодаря особенности ПВХ пленки после нагревания становиться пластичной, а после охлаждения сохранять принятую форму. На этом принципе построено оборудование для ламинирования фасадов - вакуумных и вакуумно-пневматических прессов.
Мембранно-вакуумный пресс - пресс для покрытия деталей различными финишными и декоративными покрытиями. Пресса бывают двух разных типов – более простые и дешевые вакуумные, использующие атмосферное давление и пресса с дополнительным давлением 1-8 кг/см 2, которые значительно сложнее и дороже вакуумных. Оба вида прессов могут оснащаться мембранами для прессования пористых материалов или шпоном и работать без мембраны с пленками ПВХ. Пресса с дополнительным давлением прессуют детали при давлении 0,6-8,5 кг/см2, вакуумные пресса могут дать максимальное давление на деталь не более 0,95 кг/см2 , впрочем как показывает практика его вполне хватает для большинства случаев прессования различных изделий, за исключением случаев покрытия шпоном деталей со сложным профилем. При работе со шпоном желательно применение прессов с дополнительным давлением в 5-8 кг/см2.
Остановимся подробнее на работе вакуумного пресса.
Конструктивно пресс состоит из стола, на котором размещаются заготовки; нагревателя, используемого для разогрева пленки; а также вакуумной системы, обеспечивающей создание равномерного давления на пленку за счет атмосферного давления или нагнетания избыточного давления.
Обычно процесс ламинирования в вакуумном прессе выглядит так:
- Заготовки с предварительно нанесенным и просушенным клеевым слоем равномерно размещаются на плоскости стола на специальных подкладках, соразмерных с заготовкой, для обеспечения возможности растяжения пленки и более полного облегания ею заготовки. С той же целью между заготовками сохраняются специальные технологические зазоры.
- Над всей плоскостью стола закрепляется и фиксируется прижимной планкой ПВХ пленка. Декоративная пленка обжимается по рельефу с помощью эластичной мембраны (в мембранных прессах) или с помощью создания вакуума под пленкой (в вакуумных прессах).
- Далее происходит нагрев пленки. Разные конструкции прессов предполагают разный принцип совмещения стола и нагревателя. В одних прессах подвижным является стол, в других - нагреватель. По принципу нагревания различают контактный, когда пленка непосредственно соприкасается с нагревателем, и бесконтактный, или инфракрасный, способ прогрева. Конечный результат должен обеспечить равномерный прогрев пленки до определенной температуры, рекомендованной производителем декоративной ПВХ пленки. Температура нагрева в мембранном прессе достигает – максимум - 160С, минимум - 140С.
-
После нагрева пленки начинается этап вакуумирования (т.е. непосредственно прессования). Под этим подразумевается удаление воздуха из полости между поверхностью стола и натянутой над заготовками пленкой. В результате атмосферное давление с усилием (например, 950 кг/м2) равномерно прижимает разогретую пленку к поверхностям уложенных на столе заготовок, а температура, накопленная пленкой, активирует клеевой слой.
По окончании периода выдержки под давлением (1,5-3 мин.) процесс приклеивания пленки заканчивается, хотя прочность клеевого шва достигает максимального значения только спустя несколько суток.
- После завершения этапа прессования и остывания пленки, заготовки обрезаются по контуру детали от излишков пленки.
Основные сферы применения декоративных ПВХ пленок для мембранно-вакуумного прессования
Столешницы: | ![]() |
Фасады МДФ: | ![]() |
Дверные и декоративные накладки: | ![]() |
Декоративные элементы оформления: | ![]() |
Таким образом, основное назначение ПВХ пленок при технологии мембранно-вакуумного прессования (3-D - ламинирование) – это облицовывание рельефной мебельной поверхности.
Ниже приведены примеры использования декоративных мебельных пленок ПВХ по технологии мембранно-вакуумного прессования.
Каширование мебельных поверхностей
Термин "каширование" происходит от французского cacher, что означает в переводе "прятать", "закрывать", "скрывать". В общем случае каширование - это процесс укрытия поверхности основного материала облицовочными пленками с целью улучшения его внешнего вида. В мебельной промышленности под кашированием понимают процесс облицовывания пластей рулонными пленочными материалами с использованием вальцовых прессов и последующим отверждением клеевого слоя различными способами.
В общем случае каширование предусматривает следующие операции:
- очистка кромок и пластей детали от пыли;
- нанесение клея на пласти детали;
- удаление влаги из клеевого слоя;
- размотка пленки из рулона и ее накатывание на пласти деталей;
- разделение (разрубание) непрерывного полотна пленки в разрывах между деталями;
- повторное прикатывание пленки;
- отверждение клеевого слоя.
В зависимости от степени температурного воздействия на клеевой слой технологические процессы каширования условно разделяются на холодное, теплое и горячее каширование.
При холодном кашировании удаление излишней влаги из клеевого слоя проводится при температуре цеха, а отверждение клея после накатывания пленки - в стопе, в специальном холодном прессе или без пресса, с нагружением сверху для прижатия пленки на верхних деталях стопы. Время отверждения клея - от нескольких часов до суток. Как правило, именно этот способ применяется для облицовки гладких мебельных поверхностей ПВХ пленками.
Теплое каширование предусматривает промежуточный нагрев клеевого слоя для удаления из него влаги с целью снижения времени последующего отверждения клея и снижения разбухания верхнего слоя плиты из-за впитывания. Окончательное приклеивание также производится в стопах, но время выдержки при этом снижается до нескольких часов.
Горячее каширование включает практически те же операции, что и теплое, но накатывание и прикатывание рулонного облицовочного материала производится горячими валами, нагреваемыми до температуры 120-160 С.
В некоторых моделях оборудования дополнительно используются нагреваемые до 160-180 гр. C валы, устанавливаемые перед станком для нанесения клея, что позволяет вдавить в плиту воткнувшиеся мелкие частицы, не удаленные щеточным станком, "припаять" частично отслоившиеся стружки ДСП за счет расплавления лигнина, выровнять температуру на поверхности и нагреть пласти для ускорения выпаривания влаги.
После первичного нанесения клеевого слоя и его частичного высушивания сверху может наноситься слой отвердителя. Тогда после накатывания и прикатывания пленки горячими валами сразу же достигается ее приклеивание.
Такая технология позволяет использовать клеи на основе карбамидных смол и обеспечивает практически мгновенное склеивание, исключающее промежуточную выдержку деталей перед последующей обработкой.
Quickstep
Одной из разновидностей горячего каширование является способ Quickstep. Способ был предложен в начале 70-х годов фирмой Bison для облицовывания плит пленками с заранее нанесенным слоем клея-расплава.
Технологическая линия для облицовывания этим способом состоит из комбинации обычной линии холодного каширования, разгонного ленточного транспортера и короткотактного однопролетного пресса, обеспечивающего необходимые давление и температуру при облицовывании.
В настоящее время способ Quickstep применяется для облицовывания с использованием любых клеев: на основе ПВА-дисперсий и карбамидных, ускоренного отверждения.
Линии холодного каширования применяются в производствах с относительно небольшой производительностью, при облицовывании достаточно толстыми пленками (до 130 г/кв. м), с использованием относительно дорогих клеев на основе ПВА-дисперсий. Возможность разбухания крупной стружки на поверхности ДСП из-за отсутствия удаления влаги из клеевого слоя делает более предпочтительным облицовывание на таких линиях материалов с анизотропной структурой - типа ДВП или МДФ.
Линии теплого каширования за счет наличия зоны выпаривания влаги из клеевого слоя позволяют облицовывать и древесностружечные плиты, обеспечивая более высокое качество поверхности.
Линии типа Quickstep дают наиболее высокое качество облицовывания за счет использования плоского пресса, обеспечивающего выравнивание прессуемой поверхности и более равномерный нагрев. Однако производительность таких линий ниже и ограничивается скоростью подачи проходного участка (каширование) 7-10 м/мин. Но такие линии могут обеспечивать применение облицовочных пленок практически любой массы (60-140 г/кв. м), любых клеев (ПВА-дисперсий и карбамидных) и практически полностью исключают появление дефектов поверхности от разбухания стружки. Кроме того, при оснащении плит пресса специальными матрицами возможно тиснение структуры поверхности на облицованной пласти, что практически невозможно при использовании только вальцовых прессов.
Линии горячего каширования на базе вальцовых или ленточных прессов обладают наибольшей производительностью (до 50 м/мин.), но требуют весьма тщательного соблюдения технологических режимов: расхода клея и отвердителя, температуры нанесения и отверждения клея и др., но главное - плотности и разной толщины облицовываемых плит.
Во всех случаях клей наносят преимущественно на плиту кистью (или валиком) при ручном методе, или клеенаносящими вальцами на линиях каширования, где пленка непрерывно разматывается с рулона и прижимается к поверхности плиты. Клей на линиях каширования непрерывно подается на вальцы либо самотеком, либо с помощью насоса.
При кашировании толщина пленки обычно составляет 150 – 200 микрон, при этом используется линия каширования.
Облицовка профиля
Принцип облицовки профильных погонажных изделий в каком-то смысле аналогичен кашированию мебельных поверхностей. Вместе с тем, оборудование для каширования плит (линии каширования) и для профильных погонажных изделий (установки для облицовки погонажа) заметно отличаются по конструкции. Основной особенностью последних является наличие прижимных валков для более точной облицовки изгибов профиля. Кроме того, говоря об облицовки профильных изделий (особенно это касается ПВХ профиля), часто упоминают термин «ламинирование». Однако главный признак ламинирования - отсутствие в процессе облицовывания такого этапа, как нанесение клея, что недопустимо в нашем случае, т.к. речь идет о ПВХ пленках без клеевого слоя. Таким образом, называть процесс окутывания профиля пленкой «ламинированием» – не может быть верным. Тем не менее, далее в тексте этот термин встречается в отношении облицовки оконного ПВХ профиля и пластиковых подоконников, поскольку он общепринят и распространен среди участников рынка.
Процесс облицовки (ламинирования) включает несколько стадий:
- обработка пленки клеем
- прохождение пленки через сушильный канал
- подогрев профиля
- приклеивание пленки при помощи прижимных валков
Таким же способом декорируются поверхности профильно-погонажных изделий из ДВП, ДСП, применяемые преимущественно для отделки внутренних помещений.
Схема технологического процесса облицовки профиля пленками ПВХ
Помимо всех преимуществ, которые дает ПВХ пленка облицованным изделиям, ее применение позволяет скрывать дефекты экструдированного профиля, дает возможность работать на менее качественном или вторичном сырье и, наконец, не прилагать особых усилий по достижению определенного цвета основы.
Уровень и структура потребления
По итогам 2005 года объем российского рынка облицовочных ПВХ пленок составил порядка 26,75 млн. кв.м., что в тоннажном выражении оценивается в 13-14 тыс. тонн. Из них на внутреннее производство приходится чуть более 1%, что в натуральном выражении составляет 0,3 млн. кв.м., соответственно, на долю импорта в структуре емкости рынка приходится 99% (26,45 млн.кв.м.).
Структура емкости российского рынка облицовочных ПВХ пленок в 2005 году
Учитывая, что средняя стоимость декоративной ПВХ пленки отечественного производства на российском рынке составляет 1,7$/кв.м., а импортной – порядка 4$/кв.м., текущую емкость российского рынка ПВХ пленок для облицовки поверхностей в денежном выражении можно оценить в USD 106,31 млн
Оценка объема российского рынка ПВХ пленок
Внутреннее производство | 0,3 | 510 |
Импорт | 26,45 | 105,8 |
Общий объем рынка | 26,75 | 106,31 |
Производство декоративных ПВХ пленок на территории СССР
Российский рынок декоративных ПВХ пленок практически полностью является импортозависимым и развивается за счет поставок из-за рубежа. К настоящему времени на территории бывшего СССР действует всего два предприятия по производству декоративных облицовочных пленок – в России (Мосстройпластмасс) и на Украине (Славянский завод Торэласт).
Отсутствие отечественного производства полимерных пленок для облагораживания поверхностей неслучайно, этому способствует ряд факторов. Во-первых, в СССР мебельные фасады (первоочередная сфера применения ПВХ пленок) производились главным образом из массива, который всегда ассоциировался у покупателей с благосостоянием, солидностью и красотой. Однако массив не всегда применим, например, в производстве кухонной мебели - он часто рассыхается, лак отстает, мебель теряет внешний вид. В результате наибольшее распространение получили фасады из плит МДФ. Фасады из МДФ очень красивы и разнообразны, поскольку материал позволяет делать красивую филенку (выпил) и закругленные углы. Для облицовки такой поверхности необходим материал, способный при приклеивании в точности повторить рисунок (выпил) на древесной плите.
На сегодняшний день это стало возможным только благодаря гибким полимерным пленкам, которые при высокой температуре расплавляются и гладко облегают неровную (закругленную) поверхность. Т.е. изготовление фасадов, облицованных полимерной пленкой – довольно молодое направление в мебельной индустрии, соответственно и потребность в собственном производстве ПВХ пленок еще до конца не осознана отечественными потенциальными производителями. Примером этого может служить украинское предприятие Торэласт, которое, имея оборудование с 70-х годов, занялось производством аналогичных пленок лишь в 2004-2005 гг. То же самое можно отметить и в отношении пленок для ламинирования оконного/дверного пластикового профиля. Мода на цветные окна стала распространяться на российском рынке сравнительно недавно.
C текущей ситуацией и прогнозом развития российского рынка декоративных ПВХ пленок можно познакомиться в отчете Академии Конъюнктуры Промышленных Рынков «Рынок декоративных ПВХ пленок для облицовки поверхностей в России».
Об авторе:
Академия Конъюнктуры Промышленных Рынков оказывает три вида услуг, связанных с анализом рынков, технологий и проектов в промышленных отраслях - проведение маркетинговых исследований, разработка ТЭО и бизнес-планов инвестиционных проектов.
- Маркетинговые исследования
- Технико-экономическое обоснование
- Бизнес-планирование
vikont-m.ru
Способы нанесения покрытий и используемое для этого оборудование
Методы нанесения полимерного слоя на подложку можно разделить на намазывание, погружение, экструзионное нанесение покрытия, а также нанесе ние или каширование на валковой машине.
Намазывание
Принцип состоит в нанесении полимерного слоя на движущуюся подложку с последующим его выравниванием неподвижным ножом (раклей).
Выбор метода во многом зависит от вязкости полимерной массы и от толщины наносимого слоя. Поскольку однократным наложением слоя, как правило, не удается получить удовлетворительный результат, то процесс повторяется несколько раз. Первый слой служит в качестве адгезива; следующий слой придает материалу необходимые прочность и мягкость. Защитный (покровный) слой почти всегда окрашен и соответствует декоративным требованиям, предъявляемым к поверхности комбинированного материала (цвет, фактура, рисунок). Перед раклей образуется запас полимерной массы, которая равномерно поступает в зазор между ней и подложкой, образуя слой требуемой толщины. Ракля способна взаимодействовать с различными подложками. На практике с положительной стороны зарекомендовало себя несколько ракельных устройств, а именно валковая, офсетная и воздушная ракля.
В качестве валка может выступать как гладкий стальной валок, так и валок с нанесенным на него резиновым покрытием.
При использовании валкового и офсетного методов режущая кромка ракли притуплена, и ее задняя сторона имеет конфигурацию, не допускающую образования капель на отводимом полотне.
Воздушная ракля во избежание повреждений подложки имеет закругленную кромку радиусом от 1 до 2 мм. Метод намазывания в основном используется для нанесения покрытий на ткань. На гладкие ткани покрытие наносится валковой раклей, а на более грубые ткани — офсетной. Воздушная ракля применяется для нанесения лишь очень тонких слоев.
Нанесение покрытия валком
Устройство, используемое в данном методе, состоит из многовалковой системы, которая превращает наносимую массу в пленку определенной толщины, и укладывает ее на подложку, действуя по реверсивному принципу.
Именно поэтому такой метод называется Reverse-Roll-Coating. Он обладает некоторыми преимуществами, и особенно хорош при работе с пастами, обладающими высокой текучестью. К преимуществам описываемого способа относятся следующие:
• масса наносимого слоя довольно точно дозируется за счет регулировки зазора между валками и числа их оборотов;
• метод отличается высокой производительностью, поскольку в этом случае (в отличие от метода нанесения намазыванием) используется не ракля, а метод наложения пленки.
Нанесение покрытия методом погружения
В этом случае подложка протягивается через ванну, наполненную ПВХ-пастой низкой вязкости. Лишняя паста соскребается.
Такой способ нанесения покрытия в основном используется при обработке тканей с крупными ячейками или же в том случае, если при обработке синтетических тканей необходимо избежать образования адгезионного слоя. Двухстороннее I анесение покрытия обеспечивает защиту ткани с двух сторон.
Нанесение трафаретной печатью
Этот метод основан на использовании перфорированного валкового шаблона, через который ПВХ-паста продавливается на подложку с помощью гибкой ракли.
Для этого полотно, на которое предполагается нанести покрытие, протягивается между вращающимся гладильным валком и валком противодавления. Гальваническим методом изготавливают специальные никелевые шаблоны с различным размером отверстий и с участками, на которых отверстия вообще отсутствуют. Это дает возможность наносить на подложку рельефные рисунки, например, при изготовлении обоев. Подача пасты осуществляется постоянно через находящуюся в шаблонном валике трубу с продольными прорезями. Наряду с упомянутым изготовлением обоев данный метод может быть использован при любом нанесении покрытия. За счет вертикального принципа работы он особенно хорош при двухстороннем нанесении покрытия (например, в изготовлении декоративных холстов).
Экструзионное нанесение покрытия
Метод экструзионного нанесения покрытия используется в основном для нанесения ПЭ или ПП на бумагу или на тонкое листовое железо (полимерная жесть).
Принцип действия данного метода состоит в том, что экструдируемый расплав полимера из щелевой головки выдавливается на движущуюся подложку.
Нанесение расплава на подложку происходит в зазоре между валками. За счет встречного движения охлажденных валков расплав под давлением соединяется с подложкой.
Нанесение покрытия каландрованием
Мы отметили, что каландр используется в основном для изготовления листов (пленки), однако известно применение каландра и для нанесения полимерного расплава на подложку.
При нанесении покрытий таким методом вместе с расплавом во второй или третий валковый зазор поступает подложка.
В этом случае рекомендуется использование S- или F-образных каландров. Здесь расплавление полимера происходит в первом валковом зазоре. Такой метод рекомендуется использовать при прямом (без участия паст или растворов) нанесении полимеров на подложку.
Косвенное нанесение покрытий
Этот метод хорошо подходит для нанесения покрытий из ПВХ и полиуретана. В процессе изготовления искусственной кожи, соответствующей по качеству натуральной (эластичность, мягкость, фактура), необходимо использовать подложки, которые были бы мягче и эластичнее большинства тканей, например, односторон i iee трикотажное полотно и нетканые материалы. Их общий недостаток — сложность прямого нанесения покрытия.
При косвенном нанесении паста ПВХ наслаивается на покрытую полисилоксаном или меламиновой смолой антиадгезионную бумагу, а подложка вдавливается в пасту с помощью валка
После завершения желатинизации антиадгезионный материал удаляется.
Преимущество такого процесса состоит в возможности использовать подложки с относительно крупными ячейками. Покрытие из МФС наносится на бумагу очень тонким слоем, поэтому тиснение поверхности антиадгезионной бумаги отсутствует и не может передаться получаемому полимерному покрытию. В этом случае для получения рельефной поверхности и тиснения рисунка на поверхности используют каландр.
Полотно бумаги с нанесенным на него антиадгезионным слоем может проходить через соответс твующую установку от 5 до 7 раз.
Термокамера
Все подложки, на которые наносится i юкрытие из пластифицированного ПВХ, проходят через нагревательную камеру для желатинизации. Нагрев осуществляется различными способами: инфракрасным излучателем, горячим воздухом или газом. При ис1 юльзовании пасты из ПВХ рекомендуется нагрев горячим воздухом, который подается в термокамеру через форсунки. В зависимости от свойств и толщины наносимой массы полимера температуры желатинизации различны и составляют для вспенивающегося ПВХ 200 °С, а для обычных ПВХ-покрытий — от 170 до 180 °С.
При таких температурах пластификатор быстро проникает в частицы ПВХ, что приводит к их разбуханию и объединению, происходит образование гелеобразного слоя, в котором пластификатор образует с ПВХ однородную массу.
В зависимости от скорости прохождения подложки с нанесенным покрытием через термотуннель его длина может составлять от 15 до 35 метров. Транспортировка подложки внутри туннеля осуществляется рольгангом При перемещении подложки внутри камеры зачастую возникает необходимость использовать игольчатые зажимы. Если используются полимерные растворы, то термокамера служит для удаления и вытяжки (отсасывания) растворителя.
Охлаждение
Выходящую из термокамеры подложку с нанесенным на нее покрытием перед наматыванием необходимо охладить. Для этого полотно огибает несколько валков с водяным охлаждением (от 2 до 6 валков). Затем равномерно наматывается в рулоны.
plenka-mos.ru
Поливинилхлорид температура плавления - Справочник химика 21
Так, обычный полиэтилен плавится ири 105° С, а вулканизированный при помощи радиации размягчается выше 200° С [13—15]. Полиэтилен становится после облучения нерастворимым в органических растворителях, утрачивает резкую температуру плавления и превращается в прозрачный эластичный материал [16]. Облученный поливинилхлорид также имеет повышенную термостойкость [12]. [c.178]В табл. 13 указаны свойства некоторых пластмасс. Преимущество пластмассовых форм — высокая коррозионная стойкость, возможность механической обработки, а в некоторых случаях хорошая растворимость в органических растворителях, низкая температура плавления, низкая температура размягчения и т. д. Известно применение следующих полимерных материалов [9, 23, 24, 761 эпоксидных смол (усадка 0,2 %), поливинилхлорида, акрилатов, полиэтилена, сополимера дивинила, полиметилметакрилатов (органическое стекло), полистирола, целлулоида, эластичных композиций на основе поливинилхлорида, искусственной кожи, стиракрила. Следует учитывать, что процесс отверждения стиракрила (например, марки Т) происходит с выделением теплоты, поэтому заливку в форму, смазанную силиконовым маслом или 3 %-ным раствором полиизобутилена в бензине, следует выполнять небольшими порциями стиракрила. Для увеличения проводимости, механической прочности, уменьшения усадки эпоксидные составы наполняют порошками железа, меди, алюминия (до 75 %). Форму для заливки эпоксидной смолы также смазывают, как и при работе со стиракрилом. Форму из полистирола, уложенную на деревянный шаблон [761, используют для изготовления полусферической никелевой диафрагмы диаметром 1,5 мм и толщиной 0,13 мм. [c.25]
Чистый поливинилхлорид имеет относительно высокую температуру плавления, что затрудняет его переработку. Он используется для [c.723]Введение поливинилхлорида как обычного наполнителя. Смешение происходит при температуре ниже температуры плавления поливинилхлорида. ПВХ вместе с остальными ингредиентами вво- [c.64]
Продукт хлорирования поливинилхлорида лучше растворим в органических растворителях, чем исходный полимер, и служит для производства волокна хлорин. Вводя в полиамиды метилольные группы, можно регулировать температуру плавления, раствори- [c.608]
Масштабы производства поливинилхлорида измеряются миллионами тонн в год и продолжают увеличиваться быстрыми темпами. Качество поливинилхлорида — его термостойкость, долговечность зависит от качества исходного мономера — винилхлорида. К чистоте последнего предъявляются очень высокие требования. Винилхлорид при обычных условиях — газ, конденсирующийся при температуре — 12 "С. Температура плавления винилхлорида -160 "С. [c.169]
Вязкость однофазных растворов полимеров, в которых происходит незначительная кристаллизация полимера, может возрастать, и такие растворы иногда способны образовывать упругие гели без отделения растворителя. Образование геля в этом. случае обусловлено не сшиванием макромолекул химическими поперечными связями, а кристаллизацией, протекающей в небольшом масштабе. При четко экспериментально определяемой "температуре плавления геля" раствор вновь начинает течь. К таким системам относятся раствор поливинилхлорида в диоктилфталате, растворы полиакрилонитрила и полиметилметакри-лата в диметилформамиде, раствор нитроцеллюлозы в этиловом спирте, а также растворы метилцеллюлозы, желатины,агар-агара и поливинилового спирта в воде. Вопрос о том, являются ли гели однофазными и двухфазными системами, был рассмотрен Паулом [ 178], но автор не пришел к однозначному выводу. [c.328]
Формированию более совершенных кристаллических структур, а также повышению скорости кристаллизации способствует регулярность строения полимерных цепей. Так, полиэтилен кристаллизуется очень быстро и дает хорошо оформленные кристаллы. Например, при 123°С полиэтилен высокой плотности кристаллизуется за 20 мин, хотя эта температура на 14° С ниже температуры плавления его кристаллов. Наличие полярных заместителей, как правило, способствует лучшей кристаллизации благодаря повышению межмолекулярного взаимодействия. Однако при этом будут возрастать времена релаксации и особенно при нерегулярном пространственном расположении заместителей скорость и степень кристаллизации могут уменьшаться (атактический поливинилхлорид). Наличие разветвлений в макромолекулах, а также громоздких нерегулярно расположенных заместителей снижает степень кристаллизации вследствие увеличения времени релаксации в таких полимерах по сравнению с регулярно построенными неразвет-вленными макромолекулами. [c.120]
Низкотемпературная полимеризация винилхлорида под влиянием радикальных инициаторов в последние годы приобретает все большее значение в связи с тем, что этот способ полимеризации позволяет получать стереорегулярный кристаллический поливинилхлорид, который отличается от обычного атактического поливинилхлорида повышенной плотностью, более низкой вязкостью, хорошими волокнообразующими свойствами, повышенным модулем Юнга, температурой стеклования и температурой плавления. Так, например, полимеризация винилхлорида при температурах от +50 до —80°С приводит к получению полимеров, у которых по мере снижения температуры полимеризации увеличивается длина молекулярной цепи микрокристаллов от 40 до 85 А и соответственно возрастает плотность от 1,378 до 1,393 Модуль Юнга у поливинилхлорида, полученного при —15° С, в полтора раза выше, чем у обычного полимера. [c.462]
Понижение температуры реакции приводило также к возрастанию степени полимеризации. При уменьшении температуры полимеризации от +125 до —80°С было отмечено , что температура стеклования увеличивается от 70 до 100° С, а темпера-тура плавления от 155 до 300° С. Температура плавления поливинилхлорида находилась выше температуры термической деструкции и поэтому была определена из концентрационной зависимости Тт пластифицированных диоктилфталатом образцов поливинилхлорида путем экстраполяции к нулевой концентрации пластификатора. [c.462]
Так, при действии на поливинилхлорид раствора амида калия в жидком аммиаке при 20° С получают черный порошок, нерастворимый 1в бензоле с температурой плавления 400—410° С, который дает сигнал ЭПР 34. [c.481]
Большое влияние оказывает структура волокна и на его термостойкость. В отличиё от природных волокон, которые вследствие своей полярности разлагаются без плавления, синтетические волокна в большинстве случаев термопластичны. Некоторые из них достаточно устойчивы при нагревании выше температуры плавления, что позволяет проводить формование волокна прямо из расплава полимера (таковы, например, найлон-6, найлон-6,6, полиэтилентерефталат и полипропилен). Формование волокон из термически нестойких полимеров, особенно полиак-рилонитрила, ацетатов целлюлозы, поливинилового спирта и поливинилхлорида, производится более трудоемким способом полимер растворяют в подходящем растворителе и полученный раствор выдавливают через отверстия фильеры в поток горячего воздуха, вызывающего испарение растворителя, или в осадительную ванну. Безусловно, формование из расплава (там, где оно возможно) является наиболее предпочтительным методом получения волокна. Низкоплавкие волокна во многих случаях имеют очевидные недостатки. Например, одежда и обивка мебели, изготовленные из таких волокон, легко прожигаются перегретым утюгом, тлеющим табачным пеплом или горящей сигаретой. Желательно, чтобы волокно сохраняло свою форму при нагревании до 100 или даже 150 °С, так как от этого зависит максимально допустимая температура его текстильной обработки, а также максимальная температура стирки и химической чистки полученных из него изделий. Очень важным свойством волокна является окрашиваемость. Если природные волокна обладают высоким сродством к водорастворимым красителям и содержат большое число реакционноспособных функциональных групп, на которых сорбируется красящее вещество, то синтетические волокна более гидрофобны, и для них пришлось разработать новые красители и специальные методы крашения. В ряде случаев волокнообразующий полимер модифицируют путем введения в него звеньев второго мономера, которые не только нарушают регулярность структуры и тем самым повышают реакционную способность полимера, но и несут функциональные группы, способные сорбировать красители (гл. Ю). Поскольку почти все синтетические волокна бесцветны, их можно окрасить в любой желаемый цвет. Исключение составляют лишь некоторые термостойкие волокна специального назначения, полученные на основе полимеров с конденсированными ароматическими ядрами. Матирование синтетических волокон производится с помощью добавки неорганического пигмента, обычно двуокиси титана. Фотоинициированное окисление [c.285]
При изготовлении оболочек подземных кабелей связи применяются главным образом свинец и алюминий, а также поливинилхлорид и полиэтилен. Для свинцовых оболочек используется свинец марки С-3, чистотой 99,9%. Для повышения стойкости свинцовых оболочек против межкристаллитной коррозии к кабельному свинцу указанной марки дается присадка сурьмы в количестве от 0,4 до 0,8% или олова в количестве от 1 до 3%. Свинец выпускается в виде гладких с плоским основанием чушек весом 30—40 ке каждая. Температура плавления свинца 327° С. [c.72]
Получение волокон из сополимеров. Первоначально заменой гомополимеров на сополимеры стремились облегчить растворение или плавление основного сырья, так как нарушение регулярности расположения функциональных групп в макромолекулярной цепи уменьшает межмолекулярное взаимодействие. Кроме того, вследствие этого снижается температура плавления, увеличивается набухание, уменьшается вязкость раствора и расплава полимера (рис. 13.2). Например, ни поликапроамид (капрон, найлон 6), ни полигексаметиленадипамид (анид, найлон 6,6) не растворяются в метиловом спирте и плавятся соответственно при 216 и 256° С, тогда как сополимер, полученный из капролактама (50 7о) и соли АГ (50%), легко растворяется в этом растворителе и плавится при 160° С. По той же причине повышается растворимость в ацетоне триацетата целлюлозы при частичном омылении эфирных групп и поливинилхлорида при дополнительном его хлорировании. Сополимер акрилонитрила с винилхлоридом в соотнощении от 60 40 до 40 60 растворяется в ацетоне и во многих других растворителях, тогда как оба гомополимера очень трудно растворяются в большинстве органических растворителей. [c.359]
Вышеприведенные синтетические полимеры формуются из расплава. В дальнейшем будут рассмотрены некоторые полимеры, которые формуются из раствора. Формование синтетических волокон из раствора проводится в тех случаях, когда температура плавления или размягчения полимера слишком высока или если расплавы недостаточно стабильны. В настоящее время наиболее важными представителями этого класса являются волокна из полиакри-лонитрила, поливинилхлорида и их сополимеров. В связи с этим наибольший интерес представляет вопрос о действии различных растворителей (обычно растворитель подбирают эмпирически). Рассматривая эту проблему, необходимо учитывать, что при взаимодействии растворителя с каким-либо соединением прежде всего следует различать три вида сил [c.16]
Наличие экстремума на кривой зависимости теплоемкости от температуры позволяет с достаточной точностью определять температуру плавления кристаллических областей полимеров. Небольшое экстремальное повышение теплоемкости в ряде случаев наблюдается и у аморфных полимеров у полистирола оно отмечается в области 110° С, у поливинилхлорида — при 60, 90 и 115° С [35]. [c.18]
Температура сварки должна быть выше температуры текучести кристаллического полимера или температуры плавления аморфного полимера, но ниже температуры его деструкции. При кратковременной сварке (0,05—0,2 с) температура сварки может превышать температуру деструкции полимера [6, с. 58]. Так, температура сварки из полиэтилена низкой плотности лежит в пределах 115— 145 °С, сарана — 138—149 °С, поливинилхлорида — 180—210 °С. Температура нагревателя должна иметь более высокую температуру, верхний предел которой определяется производительностью упаковочного автомата и видом применяемого упаковочного материала. Так, в автоматах для розлива молока в бумажные пакеты (производительность 60 упаковок в минуту) температура нагревателя для продольного шва составляет 280—290 °С, в автоматах для изготовления пакетов из полиэтилен-целлофановой пленки (производительность 200 упаковок в минуту) температура нагревателя составляет 170—180 °С. [c.122]
Значительное влияние на площадь контакта оказывает температура. По данным работ [24, 26] резкое возрастание площади контакта наблюдается в области температуры стеклования Т - На рис. 3.11 приведены зависимости площади контакта от температуры для полиэтилена низкого давления и поливинилхлорида. В области температур ниже Гс площадь фактического контакта слабо увеличивается с ростом температуры. Начиная от температур 70° С для поливинилхлорида и 110° С для полиэтилена наблюдается интенсивный рост площади фактического контакта с увеличением температуры. Для поливинилхлорида температура стеклования = 70° С, а полиэтилен НД имеет температуру плавления кристаллической фазы (90% всего объема полимера) 120° С. С ростом температуры доля кристаллической фазы в полиэтилене уменьшается. При температурах, близких к температуре плавления, наряду с вынужденно-эластической деформацией развивается пластическая деформация. В этой области температур площадь фактического контакта растет [c.67]
Пластмассовые изделия, на которые наносятся изображения методом горячего тиснения, изготовляют обычно из полистирола, полиметилметакрилата (например, дакрила), сополимеров стирола, полиэтилена, некоторых марок поливинилхлорида или из других термопластичных материалов (субстратов), обладающих достаточной адгезией к применяемой фольге и отличающихся температурой плавления (размягчения), близкой к вышеперечисленным термопластичным материалам. [c.80]
Отлив из раствора (схема 2.1) применяют для формования пленок из полимеров, которые растворяются в органических растворителях или воде, например из производных целлюлозы, поливинилхлорида, поливинилового спирта. Этот способ особенно применим к легкорастворимым полимерам, которые нестойки в расплавленном состоянии или разлагаются при нагревании ниже температуры плавления. [c.36]
Хлорированные углеводороды отличаются повышенной растворяющей способностью и огнестойкостью. Примером алифатических соединений этого типа является хлорированный парафин, который может содержать до 50% хлора. Он представляет собой бледно-желтую химически инертную жидкость, выделяющую при высоких температурах хлористый водород применяется в качестве растворителя поливинилхлорида. Из ароматических соединений следует отметить ряд хлорированных дифенилов. С увеличением содержания хлора повышаются их температуры плавления и кипения, а также вязкость. Продукты с минимальным содержанием хлора являются подвижными, сравнительно летучими жидкостями, кипящими приблизительно при 275 °С. Высокохлорированные продукты представляют собой смолообразные или кристаллические твердые вещества. [c.335]
Переработка непластифицированного поливинилхлорида связана с трудностями из-за низких теплостойкости и теплопроводности, а также узкого интервала температур плавления полимера, за которым наступает его деструкция. [c.275]
Существенное различие в цифровых коэффициентах уравнений (134) и (135) объясняется следующим. После прохождения калибрующего приспособления температура трубы должна быть достаточно низка, чтобы размеры трубы при ее транспортировке к охлаждающей ванне не исказились. Трубы из жесткого поливинилхлорида экструдируются при температуре 170— 190° С, которая превышает температуру экструзии труб из полиэтилена низкой плотности (125—130°). Кроме того, поливинилхлорид, в отличие от полиэтилена, не имеет определенной температуры плавления, а размягчается в некотором интервале температур. Поэтому при переработке поливинилхлорида требуется более глубокое охлаждение и, следовательно, большая длина калибрующего приспособления, чем при переработке полиэтил,ена, что и вызывает различие в числовых коэффициентах указанных выше уравнений. [c.144]
Наиболее очевидный случай неоднозначности значений вязкости образцов с одинаковыми молекулярными характеристиками — это следствие сохранения в расплаве остатков кристаллической структуры и ее высших форм, которые могут быть различными. Это особенно типично, например, для поливинилхлорида, поскольку из-за очень низкой степени кристалличности и большой дефектности кристаллов он может течь при температурах, лежащих ниже равновесной температуры плавления кристаллической фазы . Другой очень своеобразный случай наблюдался Г. П. Андриановой , которая обнаружила, что вязкость полистирола зависит от концентрации, и качества (сродства к макромолекулам) того растворителя, из которого был получен образец сублимацией растворителя. Этот факт можно трактовать, как следствие сохранения в расплаве некоторой структуры, которой обладал полимер в растворе и которая зависела от природы растворителя и концентрации раствора, причем структура оказалась весьма устойчивой к последующим термомеханическим воздействиям на материал. В этой связи следует также заметить, что структурные перестройки в цасплаве вообще происходят гораздо медленнее, чем осуществляется механическая релаксация. [c.181]
Если линейный полимер находится в кристаллическом состоянии, то ниже температуры плавления — кристаллизации 7к он находится в твердом состоянии, но обладает различной жесткостью ниже и выше температуры стеклования Тс (кривая типа 2). Это связано с тем, что аморфная часть полимера в силу принципа автономности элементов суперсетки (см. 3) также молрелаксационных состояниях. Однако наличие кристаллической фазы смещает границы релаксационных состояний и вообще существенно изменяет структуру аморфньгх участков по сравнению со свободной аморфной фазой. В тех случаях, когда полимер слабо закристаллизован, то выше Тс он деформируется практически как некристаллический полимер. Типичный пример— Обычные марки поливинилхлорида. [c.70]
Температура конформационно1и перехода блок-сополимера стир л — изопрен в различных растворителях (258). Степень кристалличности и температура плавления блок-сополимеров политетрахлорбисфенол А-адипината и полистирола и данные о росте нх сферо-литов (259). Кинетические параметры кристаллизации, степень кристалличности и теплота плавления смесей поли-е-капролактона с поливинилхлоридом (259). Микроструктура и ми-крофазовое расслоение в блок-сополимерах стирол — бутадиен — стирол типа Агп-Вп т (260). Структурные параметры сополимеров стирол—диметилсилоксан при 298 К (260). Площадь поверхности доменов полистирола и их диаметр в сополимере стирол — диметилсилоксан и в смесях полистирола с полидиметилсилоксаном (260). Размеры доменов и толщина межфазного слоя в блок-сополимерах стирол — изопрен (261). [c.9]
Механо-химические процессы, происход ВО й при смешений и температура так е влияют на свойства смтсй .Свойства смесей полистирола, полиэтилена и поливинилхлорида с каучуками различны, если пластики совмещены ниже температуры плавления или вводятся на стадии латекса. Высокие температуры при совмещении каучуков и пластиков, например СКН и ПВХ, в ряде случаев приводят к структурированию каучуков и препятствуют получению однофазной системы [c.24]
После прекращения облучения повышенные значения tg б могут сохраняться довольно долго, если полимер не подвергается после облучения отжигу. Например, у облученного полиэтилена высокой плотности [77] после прекращения облучения сохраняются повышенные значения tgб и е при частотах 60—1000 Гц в области температур 353—393 К (причем е и tg б тем больше, чем ниже частота и чем выше температура). При прогреве облученного полиэтилена выше температуры плавления tg б и е/ резко и необратимо уменьшаются. Это явление объясняют большим временем жизни носителей тока в кристаллических областях полимера. Однако увеличение е и б полиэтилена после облучения может быть связано и с наличием долгоживущих в кристаллических областях продуктов радиолиза — пероксидов. К обратимым изменениям диэлектрических характеристик в процессе облучения могут привести продукты раднолиза и у полярных полимеров. Например, при мощности дозы более 25,8 мА/кг у поливинилхлорида и политрифторхлорэтилена наблюдали небольшой обратимый сдвиг максимумов tg б в сторону более высоких частот, приписываемый пластифицирующему действию продуктов радиолиза [78]. [c.95]
Переход полимера из твердого в жидкое состояние (расплав) может происходить либо при температуре стеклования Тс (для некристаллизующихся полимеров типа атактических полистирола, полипропилена, поливинилхлорида и т. п.), либо при температуре плавления Гпл (для кристаллизу- [c.6]
На основании представлений, развитых в предыдущем разделе, можно установить связь между свойствами многих важных в промышленном отношении тер мо пластиков и эластомеров и их химическим строением. Теперь должно быть понятно, почему простые линейные полимеры типа полиэтилена, полиформальдегида и политетрафторэтилена представляют собой кристаллические вещества, обладающие довольно высокими температурами плавления. Полученные обычным способом поливинилхлорид, поливинилфторид и полистирол обладают гораздо меньшей степенью кристалличности и имеют более низкие температуры плавления у этих полимеров физические свойства сильно зависят от стереохимической конфигурации. Полистирол, полученный методом свободнорадикальной полимеризации в растворе, является атактическим. Этот термин означает, что если ориентировать углеродные атомы полимерной цепи, придав ей правильную зигзагообразную форму, то фенильные боковые группы окажутся распределенными случайным образом по одну и по другую сторону вдоль цепи (как это показано на рис, 29-7). При полимеризации стирола в присутствии катализатора Циглера (разд. 29-5,А) образуется изотактический полистирол, отличающийся от атактического полимера тем, что в его цепях все фенильные группы распо- [c.498]
Здесь будут коротко рассмотрены чрезвычайно многочисленные искусственные материалы. Они весьма ценны для препаративной неорганической химии прежде всего благодаря их большой устойчивости к HF и сильным щелочам. Однако их пригодность, особенно при высоких температурах, следует испытывать в каждом отдельном случае. Нежесткие термопластичные. ) искусственные материалы, как винидур, оппанол, тролитул, плексиглас [198], можно сгибать не только при нагревании, но и сваривать при температуре течения [1991 . Для этого сварочные стержни из того же материала нагревают горячим сжатым воздухом. Температура плавления твердого поливинилхлорида (ПВХ) 175°, температура горячего воздуха должна быть в этом случае 200—250°. Для оппанола температура горячего дутья должна быть 250—-300°, для плексигласа 300—350°. В ряде случаев применяют также паяльники в виде куска чистого серебра или меди. В случае, если диэлектрические потери материала незначительны, как у полистирола или полиэтилена, их тонкие листки лучше всего сваривать токами высокой частоты под механическим давлением. [c.48]
Как правило, полимеры сравнительно редко применяются в чистом виде. Вызвано это тем, что большинство полимеров нуждается в дополнительной модификации для придания им необходимых технологических и эксплуатационных свойств. Кроме того, многие полимеры не могут быть переработаны в изделия в чистом виде (например, поливинилхлорид), поскольку температура их термического разложения ниже температуры плавления или размягчения. Немаловажное значение имеет снижение полимероемкости изделий, что достигается введением в полимеры различных наполнителей. Для придания изделиям специальных свойств, таких, как морозостойкость, биОстойкость, ударостойкость и т. п., применяются специальные добавки. [c.22]
Полиамидные смолы имеют линейное строение молекул, а следовательно, они термопластичны. Эти смолы представляют собой твердые высокоплавкие вещества с микрокристаллической структурой и температурой плавления от 180 до 250°. Они имеют рогоподобный вид и несколько просвечивают. Их удельный вес колеблется в пределах 1,10—1,15. По сравнению с некоторыми другими синтетическимп смолами (поливинилхлоридом, полистиролом) полиамидные смолы обладают более высокой водопоглощаемостью (до 8%). Они относительно стойки к действию щелочей, но чувствительны к кислотам, при действии которых гидролизуются. Ценным свойством является [c.146]
Хорошим методом соединения между собой изделий из полиамидов или полиуретанов является также сварка—процесс, в принципе похожий на автогенную сварку металлов,—в том виде, как он давно и в разнообразных формах с успехом применяется для сварки других пластических масс, прежде всего поливинилхлорида. При сварке полиамидов нужно обратить внимание на их характерные особенности четко выраженную тештературу плавления и чувствительность расплава к кислороду. Сварка лучше всего осуществляется в токе горячего азота, температура которого должна быть выше температуры плавления свариваемого материала. Для предотвращения порчи материала от местных перегревов температура азота не должна превышать температуру плавления применяемого материала более чем на 30—50°. Естественно, что при этом процессе толстостенные части выдерживают более высокую температуру, чем тонкостенные и тем более пленки. [c.232]
Небольшие дефекты покрытий из полиэтилена, пентапласта, полипропилена, сополимеров этилена с пропиленом, поливинилхлорида и ряда фторполимеров можно заделывать следующим образом. Места дефектов зачищают до металла с плавным переходом на материал покрытия и место дефекта на металле (свищи, раковины) зачеканивают. Стенку изделия снаружн подогревают газовой горелкой до температуры плавления полимера, на место дефекта вручную насыпают порошок, утрамбовывают его и оплавляют, подогревая газовой горелкой с наружной стороны изделия. [c.259]
Можно было ожидать, что с увеличением когезионной энергии температура плавления полимеров должна возрастать. Как видно из табл. 1, в некоторых случаях это положение оправдывается (в ряду полиэтилен, поливинилхлорид, найлон 66). Однако таким образом нельзя объяснить высокую температуру плавления полиэтилентерефталата и тефлона, а также большое различие в температурах плавления полиэтиленадипамида и полиэтилентерефта- [c.8]
Ниже температуры стеклования аутогезионная связь у аморфных полимеров не образуется, поскольку скорость диффузии очень мала, а энергия активации процесса, напротив, высока (например, ниже 60° С для поливинилхлорида = 50 -т- 90 ккал1моль) [146]. Кристаллические полимеры точно так же не способны к аутогезии ниже температуры плавления [147, 148]. [c.70]
После прекращения облучения повышенные значения tgo могут сохраняться довольно долго, если полимер не подвергается после облучения отжигу. Например, у облученного полиэтилена высокой плотности [217] после прекращения облучения сохраняются повышенные значения tg o и е при частотах 60—1000 Гц в области температур 353—393 К (причем е и tg o тем больше, чем ниже частота и чем выше температура). При прогреве облученного полиэтилена выше температуры плавления tg o и е резко и необратимо уменьшаются. Это явление объясняют большим временем жизни носителей тока в кристаллических областях полимера. К обратимым изменениям диэлектр 1ческих характеристик в процессе облучения могут привести продукты радиолиза. Например, при мощности дозы более 25,8 мА/кг (100 Р/с) у поливинилхлорида и политрифторхлорэти- [c.142]
Изготовление плоской пленки на каландре. Каландрование, применяемое в основном для изготовления пленки из поливинилхлорида, в настоящее время в опытном порядке используется и для производства пленки из полиэтилена. Хотя мягкий полиэтилен вследствие невысокой температуры плавления склонен легко прилипать к поверхности металлическах валков, его все же можно каландровать " . Значительно благоприятнее условия переработки твердого полиэтилена. Сорта полиэтилена, предназначенные для каландрования, должны содержать антиоксиданты, так как горячий расплав с температурой около 150°С соприкасается с воздухом в течение 15 мин и более. [c.142]
Полидихлорметиленоксипропилен (пентон) — новый кристаллизующийся полимер, впервые синтезированный в середине 50-х годов текущего столетия. Содержит 45,5% хлора, который входит в состав хлорметильных групп, присоединенных к атому углерода в цепи, не содержащей дополнительных атомов водорода. Вследствие этого при нагревании полимера исключается возможность отщепления хлористого водорода, ускоряющего термическую деструкцию полимера, как это наблюдается в поливинилхлориде [8]. Расплав полимера имеет сравнительно низкую вязкость, что облегчает его переработку в изделия методом литья под давлением. Температура плавления кристаллических структур пентона соответствует 180°. При нагревании полимера до 285° он размягчается без деструкции. В вязкотекучем состоянии пентон легко формуется, образует пленки и волокна, легко подвергается ориентации [9]. [c.507]
Полипропиленовые пленки, полученные экструзией через плоскую щель, жесткие поливинилхлоридные пленки, которые легко разлагаются при температурах, близких к температурам плавления, пленки из поливинилового спирта, полиэфира с высокой тем-пературой плавления, поликарбонатные пленки, пленки из фторопластов трудно соединить методом сварки при нагревании. Наиболее трудно осуществить сварку при нагревании термоусадочных пленок. Так как пленки из поливинилхлорида, сарана, полистирола, полиэтилена, полиэтилентерефталата уже при низких температурах усаживаются, их. в рку необходимо проводить такими методами, при которых 1срмоусадки не происходит, — импульсным, ультразвуковым и газопламенным. [c.110]
Специальные порошкообразные адсорбенты на основе полиэтилена могут быть получены в результате радиационной полимеризации этилена в газовой или жидкой фазе (в присутствии разбавителя, не растворяющего полиэтилен) при температуре ниже температуры плавления полимера [408]. Поверхностная модификация полученного таким способом продукта, повышающая эффективность адсорбции газов, может осуществляться либо нанесением на его порошок или гранулы других полимеров (полистирола, поливинилацетата, поливинилхлорида, полиметилметакрнлата, найлона, полибутадиена и др.) из растворов, не растворяющих полиэтилен, либо привитой полимеризацией с ним виниловых мономеров (стирола, винилацетата, винилхлорида, винилиденхлорида, акриловой кислоты и др.) [409, 411]. Полимеризованный при мощности поглощенной дозы у-излучения 100 рад/с, температуре 30 °С и давлении 400 кгс/см порошкообразный полиэтилен с молекулярным весом плотностью [c.240]
chem21.info
Пленка ПВХ - что это такое?
16.12.2015
Поливинилхлорид (ПВХ, полихлорвинил, винил, вестолит, хосталит, виннол, корвик, сикрон, джеон, ниппеон, сумилит, луковил, хелвик, норвик и др.) —бесцветная, прозрачная пластмасса, термопластичный полимер винилхлорида. Отличается химической стойкостью к щелочам, минеральным маслам, многим кислотам и растворителям. Не горит на воздухе и обладает малой морозостойкостью (−15 °C). Нагревостойкость: +66 °C.
— ru. wikipedia. org
ПВХ - это давно известный строительный материал. Словосочетание «Профиль — ПВХ» уже довольно крепко вошло в нашу жизнь, но, не все знают (конечно, не считая химиков), что собственно означают эти три буквы. ПВХ -это аббревиатура полезнейшего материала — поливинилхлорида.
Испокон веков, когда ученые или исследователи пытаются изобрести, что-то (прибор или же материал), они движутся не мыслями об удобствах и экономии, а желанием получить больше знаний или же усовершенствовать свое изобретение и могут не заметить многих открытий, совершенных случайно. Так произошло и с горным инженером и химиком Реньо, первым получившим поливинилхлорид. Это случилось в 1835 г., когда Анри Виктор Реньо трудился в Гиссене, в лаборатории Юстуса фон Либигса. В растворе, содержащем винилхлорид, который несколько дней стоял в пробирке на подоконнике, случились трансформации: образовался порошок белоснежного цвета. Этому содействовал солнечный свет, вступивший в реакцию с веществом в пробирке. Собственные испытания Реньо продолжил в Лионе (Франция). Он пытался проводить с порошком различные эксперименты, но ни вызвать какой-нибудь особенной реакции, ни растворить его Реньо не сумел. В итоге ученый, записав и опубликовав собственные исследования, престал увлекаться приобретенным невзначай, веществом. Так, Анри Виктор Реньо в первый раз получил поливинилхлорид, сам того не понимая. История открытия поливинилхлорида довольно увлекательна и драматична. Его открывали и забывали, вслед за этим снова открывали.
Так происходило несколько раз. В итоге это достаточно несложное соединение имеет 4 открывателей, а признание к нему пришло только через век.В первый раз более детально продукт полимеризации винилхлорида был изучен в 1878 году, впрочем итоги данных исследований достоянием промышленности так и не стали. Случилось это только в следующем веке.
В 1912 г. стартовали новые исследования по поиску возможностей для промышленного выпуска поливинилхлорида (ПВХ). Ученый Фриц Клатте, служащий германской хим. компании «Грайсхайн Электрон», соединил ацетилен с хлороводородом и, получившийся раствор, поставил на полку. Через некоторое время он заметил, выпавший, осадок. Так как химия, в то время, уже довольно много знала о строении вещества, ученый понял, что это полимер (винилхлорид). В 1913 году Фрицем Клатте первым был получен патент на производство поливинилхлорида (ПВХ). Он планировал ПВХ применить взамен целлулоида, потому что по сравнению с ним ПВХ был, сложно воспламеняем. Начало первой мировой войны воспрепятствовало Фрицу Клатте исследовать ПВХ и сферу его применения детальнее, производство было замороженно. Не смотря на это, Клатте заслуженно является родоначальником промышленного изготовления поливинилхлорида.В больших масштабах создание поливинилхлорида стартовало в Германии в тридцатые годы. В 1931 г. группировка pASF выпустила 1-ые тонны ПВХ. В 1938 г. в германском мегаполисе Биттерфельде была запущенна линия, предназначенная для изготовления 1,5 тыс. тонн поливинилхлорида в год. Фирмой вещество было патентовано в Германии, но практического применения не нашло; в 1925 г. срок на патент истек. В это же время над получением полимера трудился американский ученый Уолдо Силон. В 1926 г. у него получается получить поливинилхлорид и Силон заново его описывает. В том же году американская фирма, в которой трудился ученый, получает патент на поливинилхлорид, впрочем, в отличие от германцев, довольно быстро находит сферу его использования. Инициатива снова же шла от Силона, порекомендовавшего производить из полимера занавески для ванн. Дальше участь ПВХ начала складываться довольно успешно: в 1931 г. концерн BASF запустил 1-ое производство (многотонное) по выпуску продукции из поливинилхлорида, изготавливали буквально все — от детских бутылочек до автозапчастей.После Второй мировой войны ПВХ получил статус самого популярного материала для производства пленок, покрытий для пола, профилей, труб и множества разнообразных пластмассовых изделий.В середине двадцатого века поливинилхлорид начали использовать и для изготовления окон. В начале в США, а вслед за тем и в Германии были получены патенты на 1-ые оконные профили с использованием поливинилхлорида.Этот такой знакомый и привычный пластик вправду незаменим для изготовления множества нужных вещей.
Поливинилхлорид (ПВХ) — универсальный термопластик, получаемый из этилена и хлорида натрия методом полимеризации винилхлорида. Создание поливинилхлорида считается одним из самых наукоемких и трудных.
На текущий момент поливинилхлорид (ПВХ) — самый нужный дизайнерами и конструкторами материал и это объясняется его уникальными качествами:Универсальность. Поливинилхлори имеет привлекательный внешний вид, может быть как жестким, так и гибким, легко подвергается резке, сварке, формованию, склеиванию.
Долговечность. Материалы из ПВХ имеют все шансы работать больше 100 лет.Погодостойкость. Поливинилхлорид не может быть как жестким среды: солнечных лучей, влажности, высокой и низкой температуры воздуха, природных микрооганизмов, насекомых и в следствие этого, именно он,применяется для изготовления кровельных покрытий.Огнезащищенность. По причине присутствия в молекуле хлора, ПВХ считается трудновоспламеняемым материалом, из-за чего изделия из него не поддерживают горения.Барьерные качества. Поливинилхлорид имеет очень низкую проницаемость по отношению к газам, парам и жидкостям. ПВХ пластики имеют необходимую механическую прочность, хорошие электроизоляционные качества, хорошую хим. стойкость: не растворяются в керосине и бензине, стойки к воздействию щелочей и кислот.Энергоэффективность. Поливинилхлорид имеет высокую теплотворную способность (в мусоросжигателях, при его утилизации, выделяется большое количество тепла для подогрева помещений (жилых и промышленных), и нет загрязнения окружающей среды)Экономичность. Поливинилхлорид — самый дешевый крупнотоннажный полимер, изделия из него обладают лучшим соотношением цена-качествоГигиеничность. Это самое весомое, на текущий момент, свойство ПВХ, из него производят сосуды для хранения плазмы и крови. Сроки хранения крови в сосудах из иных материалов гораздо меньше, а это означает, что появляется надобность в большем числе доноровЭкологичность. Поливинилхлорид только 43% состоит из производных нефти, а это сберегает невозобновляемое природное сырьеВозможность вторичной переработки. ПВХ больше других полимеров, подходит для вторичной переработкиБезопасность. Поливинилхлорид абсолютно неопасный материал и это подтверждено скрупулезными научными исследованиями
Пленка ПВХ - одно- и многослойные жесткие пленки для мембранно-вакуумного прессования. Пленки производятся из твердого ПВХ, который не содержит испаряемых пластификаторов. Материал имеет повышенную тепловую и химическую стойкость, водоустойчивость, он трудно воспламеняем и нетоксичен.Пленка ПВХ имеет хорошие качества прессования, она устойчива к солнцу, плохой погоде, царапанам. Пленка не отслаивается, даже при самых плохих погодных условиях.ПВХ используется для облицовывания фрезерованных плоскостей мебельных фасадов из плит МДФ, отделки дверей, дверных рам, внутренних интерьеров. Пленки безупречно приклеиваются, великолепно выглядят в интерьерах. Крашение, тиснение и хорошая восприимчивость к нанесению печатных рисунков дают возможность получать различные декоративные решения.Мебельные, термопластичные пленки ПВХ, предусмотрены для переработки на мембранно-вакуумных прессах. Пленки производятся из твердого ПВХ, который не содержит испаряемых пластификаторов. За счет чего, пленки имеют увеличенные тепловую и хим стойкость, устойчивость к механическим повреждениям, цветоустойчивость. Благодаря этим свойствам они обширно используются для производства мебельных фасадов, дверных накладок, мебели для ванных комнат.ПВХ пленка имеет следующие преимущества:- не состаривается- устойчива к механическим и хим. повреждениям- устойчива к влиянию атмосферы и низкой температуры- устойчива к УФ-лучам (высокая светостойкость)- имеет большую прочность- невосприимчивость к образованию пятен- легко очищается
Мембранное или вакуумное прессование - это процесс, при котором давление равномерно прижимает разогретую пленку к поверхностям, уложенным на столе заготовок, а температура, накопленная пленкой, активирует клеевой слой. Технология мембранно-вакуумного прессования дает возможность облицовывать ПВХ пленками самые трудные глубокие профили фасадных деталей и погонажных изделий. С помощью подобной технологии можно изготавливать непрерывные линии профиля и придавать изделиям округленные формы. Как итог поверхности имеют увеличенную износоустойчивость, увеличивающую срок эксплуатации изделий. Процесс 3D ламинирования фасадов возможен, из-за особенности ПВХ пленки вследствие нагревания делаться пластичной, а после охлаждения сохранять принятую форму. На данном принципе построено оборудование для ламинирования фасадов - вакуумных и вакуумно-пневматических прессов.
"Магазин хороших дверей" предлагает пленки ПВХ для отделки Ваших межкомнатных и входных дверей методом мембранного и вакуумного прессования в нашем каталоге.
good-doors-shop.com